Researchers increase efficiency of flat-panel solar thermoelectric generator
Nature Materials DOI: 10.1038/nmat3013
In what may be a route to the use of thermal solar energy on a small (less than industrial) scale, researchers at MIT, GMZ Energy, Boston College, and the Masdar Institute of Science and Technology in Abu Dhabi, United Arab Emirates, have reported the development of a flat-panel solar thermal to electric power conversion technology. The solar thermoelectric generator (STEG) consists of a wavelength-selective solar absorber flat panel, a pair of p- and n-type nanostructured Bi2Te3 thermoelectric elements, and two bottom electrodes that serve as heat spreaders, all enclosed in an evacuated glass chamber. This configuration enables thermal concentration sufficient to generate the necessary temperature differential of approximately 200°C across the thermoelectric device to achieve acceptable efficiencies. The researchers report an efficiency of 4.6% under AM 1.5 conditions, which they say is seven to eight times higher than the best previously reported value for a flat-panel STEG.
Scientists report flexible solar cells with record efficiency
Nature Materials DOI: 10.1038/nmat3122
Scientists at Empa, the Swiss Federal Laboratories for Materials Science and Technology, have reported flexible solar cells with a world record 18.7% efficiency. The group, led by Ayodhya N. Tiwari, overcame the low temperature deposition challenge posed by polymer substrates with low melting points, which in the past has limited the efficiencies of flexible solar cells. The quaternary copper indium gallium (di)selenide (CIGS) semiconductor system that absorbs light and converts it into electricity tends to suffer from composition grading when deposited at lower temperatures compatible with polymer films, because of inadequate interdiffusion of intermediate phases and preferential diffusion of gallium (Ga) toward the electrical back contact. By controlling the Ga and In evaporation flux during different stages of the evaporation process, the researchers were able to improve the composition profile to enable efficient charge-carrier collection and reduce interface recombination, resulting in the high efficiency reported.
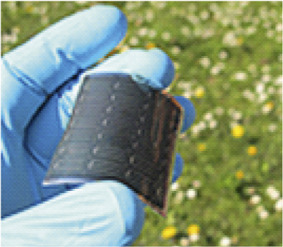
Flexible CIGS solar cells developed at Empa.
Iron “veins” serve as hydrogen transport pipeline
NIST Tech Beat DOI: 10.1016/j.ijhyolene.2011.04.196
When it comes to storing hydrogen for use in fuel cells or other devices envisioned for the “hydrogen economy,” it is not just the amount of hydrogen that a material can store, but also how fast it can store and release it that matters. A research team at the National Institute of Standards and Technology (NIST) led by Leo Bendersky has recently reported a thin-film architecture involving veins of iron running through fine-grained magnesium that meets both hydrogen capacity and charge/discharge requirements. Taking advantage of the immiscibility of Mg with transition metals such as Fe, they fabricated two-component thin films with Fe serving as a “pipeline” for hydrogen transport and Mg serving as an “accumulator.” To date, the researchers have been able to fully load the Mg-Fe thin film to 7% (by mass) of hydrogen in less than a minute at the moderate temperatures and pressures needed for a mass market product, as reported in the International Journal of Hydrogen Energy.
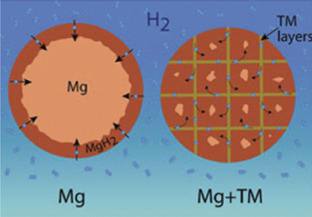
Particles of pure magnesium (left) can only collect a limited amount of hydrogen on their outer surfaces, and the process is slow. But when the magnesium is doped with iron (right), far more hydrogen is delivered through the iron layers, which also results in much faster charging. Credit: NIST
Carbon nanotubes reinforce lighter, tougher wind turbine blades
When it comes to wind turbine blades, lighter is better. Heavy blades require more wind to turn them, resulting in efficiency losses. But toughness cannot be sacrificed in the weight-loss process. Now Marcio Loos of Case Western Reserve University, along with colleagues at Bayer Materials Science in Pittsburgh and the Molded Fiber Glass Co. in Ashtabula, Ohio, has developed a polyurethane blade reinforced with carbon nanotubes that is lighter, more rigid, and eight times tougher than blades made of traditional epoxy and vinyl ester composites. Substituting carbon nanotubes for traditional carbon fibers or aluminum reinforcement in the composite increased the tensile strength by a factor of five over carbon fiber and 60 over aluminum. Fatigue, delamination, and fracture properties were also improved. Further research is under way to optimize the manufacturing process in order to maximize the nanotube dispersion in the resin, which might lead to ever better mechanical properties.