Introduction
At present, alumina (Al2O3) is produced from bauxite ores through alkali pressure leaching by the Bayer process. In addition, many attempts have been made to utilize raw materials such as nepheline-syenites, coal fly ash, shale, and kaolinitic clays to obtain alumina (Bazin et al. Reference Bazin, El-Ouassiti and Ouellet2007; Numluk and Chaisena Reference Numluk and Chaisena2012). Among these materials, kaolinite has been the most studied (Habashi Reference Habashi1999). Pyrophyllite (Al2(Si4O10)(OH)2), however, is another aluminosilicate clay mineral with a dioctahedral 2:1 structure and theoretically contains 28.3% Al2O3, and thereby also has much potential in this field. Due to its excellent thermal properties, the greatest use for pyrophyllite has been in the refractory and ceramic industries (Sánchez-Soto & Pérez-Rodriguez Reference Sánchez-Soto and Pérez-Rodriguez1998). However, only a limited number of studies can be found in the literature on the aluminum extraction from pyrophyllite and its utilization as an alumina source, the most recent of which were conducted by Erdemoğlu et al. (Reference Erdemoğlu, Birinci, Uysal, Porgalι and Barry2018) and Barry et al. (Reference Barry, Uysal, Birinci and Erdemoğlu2019).
The alumina extraction process from clays consists of four main steps: (1) heat treatment (i.e. calcination) of the clay for thermal activation, (2) acid leaching of the thermally activated clay, (3) precipitation of aluminum salt from the leaching solution, and (4) roasting the salt for final Al2O3 (Gupta and Mukherjee Reference Gupta and Mukherjee1990; Habashi Reference Habashi1999).
Because heat treatment transforms the clay minerals into a disordered metastable state by the effect of dehydroxylation, thus enhancing the solubility of Al3+ (Kyriakogona et al. Reference Kyriakogona, Giannopoulou and Panias2017) and Fe3+ (Hulbert & Huff Reference Hulbert and Huff1970), it is generally required before acid leaching. During the thermal treatment, the structure of the clay minerals is modified to a non-crystalline metastable phase (D'Eliaa et al. Reference D'Eliaa, Pinto, Eramo, Giannossa, Ventruti and Laviano2018). During heating of the phyllosilicates, four different processes may occur separately or concurrently: (1) oxidation of cations; (2) successive transformation of the structural OH groups to a vapor phase to form a dehydroxylated phase; (3) migration of the cations to different sites; and (4) disintegration of the structure (Li et al. Reference Li, Zeng, Luo, Liu, Jiang and Qiu2014; Birinci et al. Reference Birinci, Uysal, Erdemoğlu, Porgalι and Barry2017). Also, their structure appears as amorphous and soluble in dilute acids (Habashi Reference Habashi1999). Summaries of the thermal transformation stages of pyrophyllite have been presented by many researchers (e.g. Mackenzie et al. Reference Mackenzie, Brown, Meinhold and Browden1985; Sánchez-Soto et al. Reference Sánchez-Soto, Sobrados, Sanz and Pérez-Rodríguez1993; Zhang and Wang Reference Zhang and Wang1998; Li et al. Reference Li, Zeng, Luo, Liu, Jiang and Qiu2014).
The recovery of alumina from kaolinitic clays has received much attention: Al-Ajeel and Al-Sindy (Reference Al-Ajeel and Al-Sindy2006) reported that dissolution of aluminum from a kaolinitic clay sample reached a maximum if the clay was calcined at 720°C, while Al-Zahrani and Abdul-Majid (Reference Al-Zahrani and Abdul-Majid2009) found that maximum extraction from kaolinitic clay was obtained by heating the clay at 600°C. Altıokka and Hoşgün (Reference Altιokka and Hoşgün2003), Altıokka et al. (Reference Altιokka, Akalιn, Melek and Akyalçιn2010), and Olaremu (Reference Olaremu2015) investigated the dissolution kinetics of kaolin in acid solutions, and applied a calcination procedure for kaolin at 700, 800, and 750°C, respectively, before leaching. Lima et al. (Reference Lima, Angélica and Neves2014) and Adekitan and Ayininuola (Reference Adekitan and Ayininuola2017) concluded that maximum dissolution of aluminum was achieved from metakaolin obtained at 650–900°C. The differences between the reported calcination temperatures at which most aluminum extraction occurred may be due to the source and nature (mineral paragenesis, amount of contents, etc.) of the clay samples studied. Therefore, the optimum temperature may depend on the clay variety. Incidentally, in the above-mentioned studies, discussions on the extraction of alumina from kaolinitic clays were based only on the thermal transformations of kaolinite.
Aluminum extraction from thermally activated pyrophyllite has been studied by several researchers. Wu et al. (Reference Wu, Chen, Zhao and Li2012) determined no change in the basic structure of pyrophyllite at temperatures <480°C. At 480–700°C, dehydroxylation reactions occurred and the physical and chemical structures of pyrophyllite were partially decomposed by removal of structural hydroxyl groups. In addition, the researchers found that the calcination temperature at which alumina recovery was highest was 700°C. Birinci et al. (Reference Birinci, Uysal, Erdemoğlu, Porgalι and Barry2017) reported that aluminum recovery by acid leaching from clay ore containing mainly pyrophyllite increased from 12.5% to 35.6% when the ore was calcined at 800°C. By applying leaching conditions which were identical to those reported by Birinci et al. (Reference Birinci, Uysal, Erdemoğlu, Porgalι and Barry2017), 52.45% of aluminum was extracted by Aydoğmuş and Erdemoğlu (Reference Aydoğmuş and Erdemoğlu2019 when pyrophyllite concentrate containing pyrophyllite almost exclusively, as obtained by froth flotation, was calcined at 900°C. Moreover, when pyrophyllite concentrate, as obtained by attrition-scrubbing, was calcined at 850°C, 67.88% of aluminum was recovered by acid leaching (Aydoğmuş Reference Aydoğmuş2019). The reasons for these poor aluminum recoveries obtained by leaching after heat treatment were not discussed in detail, however, and no reports have been made of the use of ores containing both kaolinite and pyrophyllite.
The objective of the current study was to investigate the effects of calcination of pyrophyllite ores with complex mineralogical composition on aluminum extraction by acid leaching, and to relate the mineralogy of the ore to changes in calcination products prior to the leaching process.
Materials and Methods
Material
The pyrophyllite ore sample used in the study was from the Pütürge clay deposits in Malatya (Turkey). The lump ore sample was first crushed to <4.75 mm by a jaw crusher (Fritsch Pulverisette 1, Idar-Oberstein, Germany) with manganese steel crushing jaws and lateral walls. Then, the crushed ore was milled to <0.5 mm using a laboratory-scale ball mill (manufactured by Ünal Engineering and Machinery Industry, İzmir, Turkey) with a porcelain jar and balls. After every 5 min of milling operation, the jar was opened and the mill content was screened to collect the <0.5 mm particles, by using an ASTM-E11 type test sieve. Particles >0.5 mm were returned to the porcelain jar to continue the milling. The milled ore was divided into small lots using a rotary sample divider prior to calcination and leaching tests. The lots were stored in small polyethylene bottles with screw caps.
Methods
The calcination tests were performed in a muffle furnace (Protherm PLF130/5, İstanbul, Turkey) with a maximum heating temperature of 1300°C under non-isothermal conditions. Each sample with a particle size <0.5 mm was oven dried at 105°C and then calcined at various temperatures in the range 200–1300°C with constant calcination time (30 min) and heating rate (10°C·min−1). After cooling in a desiccator, the calcination products were packaged for use in analytical studies and leaching experiments.
To evaluate the performance of thermal treatment, the dehydroxylation degree, D tg (Rahier et al. Reference Rahier, Wullaert and Van Mele2000), was calculated according to:

where M and M max are the residual mass loss at the applied temperature and the maximum mass loss at atmospheric temperature, respectively, and which reveals to the mass of bound hydroxyl ions in the raw ore.
The ore and calcination products were subjected to a batch-leaching test using HCl (Merck, 37%) solution. For each test, 10 g of the sample was subjected to 200 mL of 4 M HCl solution in a 500 mL, four-necked borosilicate glass reactor equipped with a thermocouple and a water-cooled condenser, which was then placed in an Mtops MS-DMS 633 (Duckye-Dong, Republic of Korea) stirring heater mantle. The temperature of the reactor was controlled by a programmable controller of the mantle. Magnetic stirring was used to mix the slurry, the stirring speed being kept constant at 600 rpm. After leaching, the slurry was vacuum-filtered to separate pregnant leach solution from undissolved material which was then washed three times with dilute HCl solution. The filtrate and washings were made up to a constant volume of 250 mL in a volumetric flask to obtain stock pregnant leach solution to be used for aluminum analysis.
Aluminum in the leaching solution was determined by the gravimetric method (Lundell and Knowles Reference Lundell and Knowles1929) based on precipitating the aluminum using 8-hydroxyquinoline. All of the major oxides of the ore, i.e. Al2O3, SiO2, Fe2O3, K2O, and TiO2, in the leached residues were analyzed by Bureau Veritas Mineral Laboratories (Vancouver, Canada) using inductively coupled plasma optical emission spectroscopy (ICP-OES) after LiBO2/Li2B4O7 fusion of the sample powders. For petrographic analysis to illustrate the mineral paragenesis of the ore, thin sections were prepared from some of the lump ore samples and investigated using a polarizing light microscope. The crystal structure analysis of the samples was carried out by X-ray diffraction (XRD) by an automated Rigaku RadB type (Tokyo, Japan) diffractometer using CuKα radiation (λ = 1.5405 Å) and operating at 40 kV and 40 mA in the range 2–80°2θ with a scanning rate of 2°2θ per min. The calibration of the XRD system was carried out using ZnO standard powder. The Jade 5.0 program was used for phase identification by matching ICDD PDF cards with the measured samples. The best-fitted peaks in the structure designated the phases present. The ICDD PDF number of the existing phases in the samples are presented in the Results and Discussion section below. Thermal characteristics of the ore and the calcination products formed during each calcination step were investigated by thermogravimetric analysis (TGA) using ~50 mg of powder in a platinum crucible, heated to 1200°C in a dry argon gas atmosphere, and using a Setaram Labsys S60 model TGA (Caluire, France) instrument equipped with a differential scanning calorimetry (DSC) rod. The microstructures of particles were observed using a LEO Evo 40 (Oberkochen, Germany) model scanning electron microscope (SEM).
Results and Discussion
Characterization of the Ore
Chemical and Mineralogical Analysis.
The ore contained 68.7% SiO2, 23.6% Al2O3, and 1.61% K2O as the main oxide components (Table 1). According to XRD analysis (Fig. 1), the ore contained pyrophyllite (Al2Si4O10(OH)2; PDF# 46-1308), quartz (SiO2; PDF# 46-1045), kaolinite (Al2Si2O5(OH)4; PDF# 29-1488), muscovite (KAl2(AlSi3O10)(F,OH)2; PDF# 07-0042), kyanite (Al2SiO5; PDF# 11-46), topaz (Al2SiO4(F,OH)2; PDF# 12-765), and diaspore (AlO(OH); PDF# 5-355). Reflections belonging to quartz were seen mainly at 20.89, 26.66, and 42.48°2θ. Reflections characteristic of pyrophyllite occurred at 9.66 and 29.16°2θ and kaolinite occurred with typical 2θ values of 12.38° and 19.97°. The strongest diagnostic reflection for muscovite appeared at 8.92°2θ. Kyanite showed characteristic peaks at 27.76, 29.93, and 36.04°2θ. At the same time, one of the peaks appeared at 27.76°2θ (3.2112 Å) on the XRD pattern (Fig. 1) and was labeled both for kyanite and topaz but may belong to K-feldspar or microcline (K(AlSi3O8)), consistent with Öner and Taş (Reference Öner and Taş2013) who demonstrated K-feldspar as a minor phase in some of the ore samples with sericite examined by microscopy, XRD, and FTIR.
Table 1 Average major oxide contents of the ore as determined by ICP-OES analysis.

Loss on Ignition at 1000°C: 4.5%

Fig. 1 XRD pattern of the ore (Prl: Pyrophyllite, Qz: Quartz, Kln: Kaolinite, Ms: Muscovite, Ky: Kyanite, Tpz: Topaz, Dsp: Diaspore).
From studies by Bozkaya et al. (Reference Bozkaya, Yalçιn, Basibüyük and Bozkaya2007) and Öner and Taş (Reference Öner and Taş2013), kyanite is the primary source material and porphyrobalasts of kyanite are often decomposed to form pyrophyllite. Muscovite is also partially altered to pyrophyllite and kaolinite along fractures and on the outer surfaces of the particle. According to Öner and Taş (Reference Öner and Taş2013), the mineral paragenesis in the pyrophyllite deposits suggests that the formation of minerals took place in two ways: (1) the transformation of kyanite into pyrophyllite by reaction with silicic acid-rich fluids (Bozkaya et al. Reference Bozkaya, Yalçιn, Basibüyük and Bozkaya2007) and quartz through retrograde metamorphism at high temperature; and (2) then pyrophyllite and probably muscovite were transformed into kaolinite and alunite through reactions with relatively low-temperature hydrothermal fluids.
The K2O content (1.61%) of the ore was relatively high due to the presence of mica minerals such as muscovite/sericite in the mineral paragenesis. Because no titanium-bearing minerals, such as rutile, were detected using petrographic and XRD techniques, the presence of TiO2 at a level of 0.48% was attributed to the presence of titanite (CaTiSiO5) (Uygun & Solakoğlu Reference Uygun and Solakoğlu2002). Titanium may also be derived from muscovite due to earlier replacement of octahedral Al3+ by Ti4+ (Brigatti et al. Reference Brigatti, Frigieri and Poppi1998).
Photomicrographs (Fig. 2) of the ore samples revealed that the ore is characterized by pyrophyllite, quartz, kyanite, kaolinite, diaspore, and muscovite. Pyrophyllite had a fibrous form in all samples. Kyanite in the samples seemed to be transformed to pyrophyllite, and its residues remained within the pyrophyllitized zones. Kaolinite and pyrophyllite were seen to have formed in fractures or cleavage planes in kyanite. Kaolinite occurred as parallel intergrowths with pyrophyllite plates. Topaz, fine-grained white K-mica, diaspore, and gibbsite accompanied the pyrophyllite and kaolinite. Topaz exhibited coarsely rounded to tabular prismatic aggregates. Diaspore occurred as anhedral grains within and surrounding kyanite. K-feldspar was not encountered in thin sections of the ore samples analyzed.

Fig. 2 Photomicrographs of selected ore samples (images on the left and right sides were taken under crossed polars and plane polarized light, respectively. Prl: Pyrophyllite, Ky: Kyanite, Qz: Quartz, Kln: Kaolinite, Ms: Muscovite, Tpz: Topaz, Dsp: Diaspore).
Thermal Analysis.
The raw ore and high-purity mineral samples of pyrophyllite and kaolinite were analyzed by thermogravimetric-differential scanning calorimetry (TG-DSC) to compare the thermal behavior of each mineral. Mass loss of the ore started at ~250°C and increased rapidly with increasing temperature to 3.9% at 900°C, while it was 1.2% both for pyrophyllite and kaolinite at 450°C (Fig. 3a). Overall mass loss of the quartz was 0.2%. A sharp peak with endothermic character at ~573°C, a broad peak with endothermic character at 610–620°C, and two very sharp peaks with exothermic character at ~1000°C and 1200°C were seen in the DSC curve of the ore (Fig. 3b). Broad endothermic peaks at 400–700°C, at which most of the mass losses occurred, for the ore, pyrophyllite, and kaolinite were indicative of the removal of OH groups existing in the structure of hydrous silicate minerals (Schomburg Reference Schomburg1985; Sánchez-Soto and Pérez-Rodriguez Reference Sánchez-Soto and Pérez-Rodriguez1989a). By evaluating the TG and DSC data together, the temperature range 450–900°C can be defined as the dehydroxylation zone for the ore.

Fig. 3 a TG and b DSC curves obtained for the ore and pyrophyllite, kaolinite, and quartz mineral samples.
An endothermic peak at 573.15°C in the DSC pattern of the ore appeared almost at the same temperature for quartz, but not on the DSC patterns of pyrophyllite and kaolinite (Fig. 3b). This endothermic peak was attributed to the transformation of α-quartz to β-quartz (Bragg and Gibbs Reference Bragg and Gibbs1925; Hansen Reference Hansen2018).
The exothermic peak appearing at 1000°C on the DSC curves of kaolinite was associated with the formation of mullite. The exothermic peak appearing at ~1000°C in the pyrophyllite DSC curve may be associated with kaolinite present as an impurity in the sample examined. This exothermic effect is characteristic of kaolinitic samples alone, and is not shown by pyrophyllite (Schomburg Reference Schomburg1985; Sánchez-Soto and Pérez-Rodriguez Reference Sánchez-Soto and Pérez-Rodriguez1989a; Pérez-Maqueda et al. Reference Pérez-Maqueda, Pérez-Rodriguez, Scheiffele, Justo and Sánchez-Soto1993). Conversely, Mikuni et al. (Reference Mikuni, Wei, Komatsu and Ikeda2005) stated that the exothermic peak found at this temperature suggested mullite formation from dehydroxylated pyrophyllite. A short exothermic peak at 1200°C, both for the ore and all of the minerals, is indicative of the mullite transformation, as well as the transformation of quartz to cristobalite with no aluminum in its structure (Ilić et al. Reference Ilić, Radonjanin, Malešev, Zdujić and Mitrović2016).
Characterization of the Calcination Products
SEM Analysis.
The micrographs (Fig. 4) obtained from SEM analyses of the calcination products revealed that the foliated structure of clay minerals in the ore roasted at 300°C was still present. Calcination at 700°C unfolded the layers of a muscovite-like mineral particle. At 1100°C, micro cracks appeared, and at 1200°C, a lot of powder appeared due to sintering of the mineral particles. Zhang & Wang (Reference Zhang and Wang1998) stated that expansion, dilation between the layers, and microcracks due to removal of OH groups from the structure take place when pyrophyllite is heated in the range ~500–800°C. Sánchez-Soto and Pérez-Rodriguez (Reference Sánchez-Soto and Pérez-Rodriguez1989b) reported that SEM examinations of the samples containing 90% pyrophyllite, 5% kaolinite, and 5% muscovite, heated to 1150°C, indicated no differences compared with the unheated material, showing that no visible changes in plate structures were caused by the heat treatment.

Fig. 4 SEM images of the calcination products obtained at various temperatures.
XRD Analysis.
XRD peak patterns (Fig. 5) of the ore and the calcination products obtained between 200 and 1300°C were compared. Peak patterns of the calcination products obtained at 200–500°C were very similar. Quartz was not affected by calcination temperature, while muscovite, kaolinite, and pyrophyllite were gradually decomposed. Kaolinite was no longer observed at 700°C. Calcination at 600°C caused a reduction in the intensity of pyrophyllite at 9.66°2θ and it was last observed at 1100°C. No trace of pyrophyllite was found in the calcination product obtained at 1200°C. Calcination up to 800°C, however, did not cause any displacement in the angular position of the pyrophyllite phase. A peak at 29.16°2θ on the XRD pattern of the calcination product obtained at 800°C was much sharper, suggesting the presence of a new phase – dehydroxylated pyrophyllite (Sánchez-Soto et al. Reference Sánchez-Soto, Sobrados, Sanz and Pérez-Rodríguez1993; Mikuni et al. Reference Mikuni, Wei, Komatsu and Ikeda2005). Li et al. (Reference Li, Zeng, Luo, Liu, Jiang and Qiu2014) reported that the XRD pattern of pyrophyllite changes when the heating temperature reaches 800°C and diffraction at 20–25°2θ becomes obscure; some diffractions disappear. In addition, major diffractions of dehydroxylated pyrophyllite remained with those of the unheated pyrophyllite, indicating that the layered structure was still preserved as dehydroxylated pyrophyllite. Mackenzie et al. (Reference Mackenzie, Brown, Meinhold and Browden1985) studied the thermal reactions of pyrophyllite and observed that dehydroxylated pyrophyllite appears after heating to 783°C, and survives further heating up to 1100°C.

Fig. 5 Changes in XRD patterns of the calcination products obtained at various temperatures with respect to the ore (Prl: Pyrophyllite, Qz: Quartz, Kln: Kaolinite, Ms: Muscovite, Ky: Kyanite, Tpz: Topaz, Mul: Mullite, Crs: Cristobalite).
The muscovite peak observed at 8.92°2θ in the ore was noted in the calcination products up to 900°C. Mariani et al. (Reference Mariani, Brodie and Rutter2006) stated that dehydroxylation of muscovite does not occur homogeneously. Therefore, as some OH was lost, the remaining OH became more tightly bound to the fivefold-coordinated Al cations, inhibiting or at least retarding further dehydroxylation. According to Gridi-Bennadji et al. (Reference Gridi-Bennadji, Beneu, Laval and Blanchart2008), as muscovite is heated to 1095°C and then to 1140°C the structure changes progressively and continuously to a high temperature form with an increasingly disorganized structure.
In addition to the existence of quartz and pyrophyllite peaks in the calcination product of 1000°C, a very small XRD peak of mullite at 16.4°2θ also appeared. No significant change was observed in the calcination products obtained at intermediate temperatures (600 to 1000°C); maintaining the initial crystal structure of pyrophyllite up to 1000°C was also reported by Mikuni et al. (Reference Mikuni, Wei, Komatsu and Ikeda2005). All diffractions of dehydroxylated pyrophyllite were lost at 1200°C (Fig. 5) and only quartz and mullite were present. At 1300°C, cristobalite with a peak at 22.2°2θ was detected.
Through assessment of the thermal transformation stages of pyrophyllite, kaolinite, and muscovite (Table 2), the temperature range for the existence of dehydroxylated phases of the minerals can be defined as 780–950°C, 400–700°C, and 475–950°C, respectively.
Table 2 Thermal transformation stages of pyrophyllite, kaolinite, and muscovite.
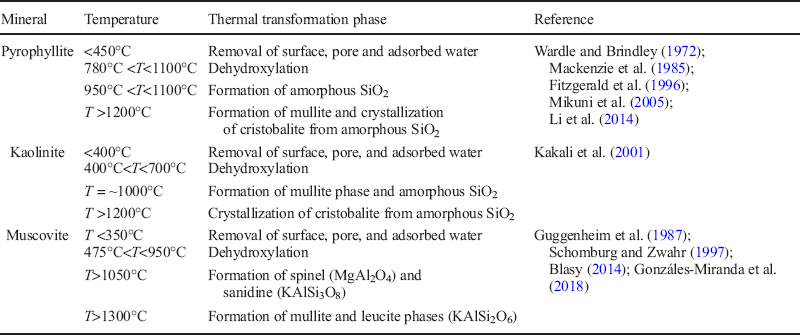
Leaching of the Ore and Calcination Products
Before examining the leaching of calcination products, the raw ore (i.e. uncalcined ore) was leached under conditions (Table 3) identical to those reported by Birinci et al. (Reference Birinci, Uysal, Erdemoğlu, Porgalι and Barry2017). Comparison of several major oxide contents of the uncalcined ore and the leaching residue (Table 3) showed that SiO2 and TiO2 contents increased while Al2O3, Fe2O3, and K2O contents decreased in the residue. Al2O3 content decreased from 23.60% in the uncalcined ore to 20.77% in the leaching residue, thus showing partial removal of aluminosilicate minerals from the ore during acid leaching and suggesting that pre-treatment such as calcination is required to increase aluminum extraction.
Table 3 Leaching conditions at low temperature (Birinci et al. Reference Birinci, Uysal, Erdemoğlu, Porgalι and Barry2017) and major oxides contents of the ore and leached residue.

Thereafter, each of the calcination product was also subjected to leaching under identical conditions (Table 3). The Al2O3, SiO2 (Fig. 6a), Fe2O3, K2O, and TiO2 the (Fig. 6b) contents of the leach residue were determined to estimate the extent of dissolution of aluminum-containing minerals during calcination and leaching. As the calcination temperature increased, variation in Al2O3 and SiO2 contents reversed of the leaching residues varied accordingly starting at 500°C up to 900°C. As the Al2O3 content decreased, SiO2 increased. Then, the trends of Al2O3 and SiO2 contents reversed dramatically after reaching minimum and maximum values, respectively, at 900°C. An increasing amount of aluminum leached from the calcination products resulted in reduction of the Al2O3 content of the leaching residue, but an increase in SiO2 content. Changes in Fe2O3 and K2O contents of the leaching residue with respect to calcination temperature suggested that muscovite, which may be the main source of Fe2O3 and K2O in the ore, can also be leached easily up to 900°C (Fig. 6b). The TiO2 content in the residues did not change until 800°C, but increased slightly from 0.58% at 700°C to 0.70% at 900°C, then decreased to 0.57% at 1000°C (Fig. 7b). This variation was suggested to be due to titanite (CaTiSiO5) (Uygun and Solakoğlu Reference Uygun and Solakoğlu2002), which was not leached in HCl solution and deposited in the leach residue, regardless of the temperature at which the ore was calcined.
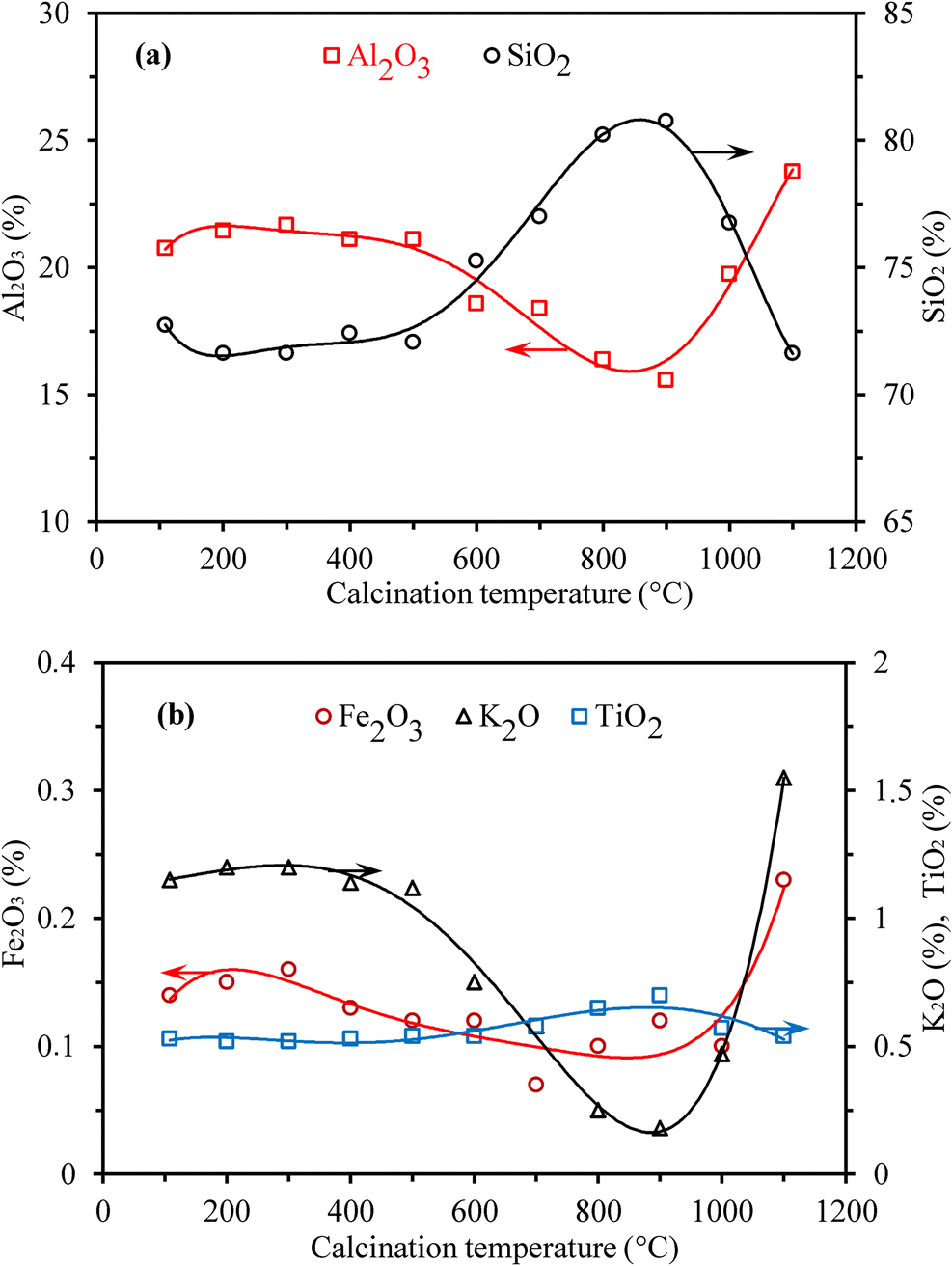
Fig. 6 Variation of a Al2O3, SiO2 and b Fe2O3, K2O and TiO2 contents of the leaching residue with respect to calcination temperature.

Fig. 7 Variation of AI concentration in the leaching solution and dehydroxylation degree of the ore with respect to calcination temperature.
When compared to the composition of the residue from calcination at 900°C, the SiO2 content decreased but the amounts of Al2O3, Fe2O3, and K2O in the residues obtained at 1000°C and 1100°C increased to values that are very close to the ore’s original composition. This suggested that the refractory structure of mullite-like phases formed at high temperatures blocked the leaching solution from penetrating the mineral structures to leach aluminum and transport it to the bulk solution.
Variation of aluminum concentration in the leaching solution with respect to calcination temperature was investigated (Fig. 7). Deviation of dehydroxylation degree (D tg) calculated using the mass-loss values recorded at 900°C during the TG analysis of the calcination product (Eq. 1) was also indicated in Fig. 7.
As indicated by the D tg curve, most (90.57%) of the mass loss occurred at temperatures between 400 and 950°C. Up to 500°C, the change in aluminum concentration in the solution was rather insignificant. As temperature increased to 900°C, however, the aluminum content in the solution increased to a maximum of 2.1 g L-1, which corresponded to an aluminum recovery of 35.6% from the residue. Calcination at higher temperatures resulted in a sharp decrease in the aluminum concentration. This recovery level is about triple that obtained without thermal treatment, but it is still below the ideal and may be due to the leaching conditions applied in this study, Hopefully this can be further after more research.
Consequently, the increase in aluminum extraction between 500 and 900°C can be attributed to formation of amorphous phases from which aluminum is easily leached, as acid attack simply broke the Al–O bonds and reformed new bonds (Kyriakogona et al. Reference Kyriakogona, Giannopoulou and Panias2017), all resulting from the destruction of the pyrophyllite, kaolinite, and muscovite structures by dehydration and dehydroxylation, giving rise to open foliation occurring in the course of thermal treatment. On the other hand, the decrease in aluminum extraction from calcination products obtained at temperatures above 900°C can be attributed to the sintering of previously foliated layers through re-crystallization to form mullite-like structures which are probably insensitive to acid attack during the leaching.
Conclusions
In order to investigate the effects of various mineral phases occurring during the heat treatment for thermal activation to increase aluminum recovery during HCl leaching, the thermal behavior of a local clay ore containing mainly quartz, pyrophyllite, kaolinite, and muscovite was investigated. The following conclusions were drawn:
(1) Calcination at temperatures between 400 and 900°C significantly increased the aluminum concentration in the leaching solution in direct proportion to the dehydroxylation degree (D tg). Aluminum recoveries obtained at calcination temperatures up to ~700°C are derived mainly from dehydroxylated kaolinite and muscovite which are ready to react with the acid to provide aluminum into the solution. Above 700°C, kaolinite transformed to a mullite-like structure which is resistant to acid attack. Dissolution of aluminum from pyrophyllite seemed to begin above ~780°C as it was still in the dehydroxylated structure. XRD peaks of muscovite and pyrophyllite appeared up to 1000°C and 1200°C, respectively. Not only aluminum, but also iron and potassium dissolution from the calcination products were diminished at temperatures >900°C as dehydroxylation of co-existing clay minerals was almost complete at this temperature. The maximum amount of aluminum recovered in the leaching solution was achieved when the calcination temperature was 900°C at which temperature D tg almost stopped increasing after reaching 90.57%.
(2) Further research on the thermal activation of clays with complex mineral parageneses and on the leaching conditions for this type of clay is needed to obtain good aluminum recoveries by acid leaching. Alternative activation methods (e.g. mechanical activation and chemical activation) to be applied before leaching may also be required.
Acknowledgments
The authors thank the Scientific and Technological Research Council of Turkey (TÜBİTAK) for financially supporting this study via Project No 214M432, İnönü University Scientific Research Project Unit for supporting the study through Project No 2015/44G, Çimsa Cement Inc. (Enis Solakoğlu, Tuğhan Delibaş, and Melike Sucu), and İçel Mining Inc. (İbrahim Altuntaş and Nihat Akkaya), for providing pyrophyllite ore samples from Pütürge (Malatya, Turkey). The support of Prof. Dr. Ömer Bozkaya (Department of Geological Engineering, Pamukkale University, Turkey) is also acknowledged gratefully.
Compliance with Ethical Standards
Conflict of Interest
The authors declare that they have no conflict of interest.