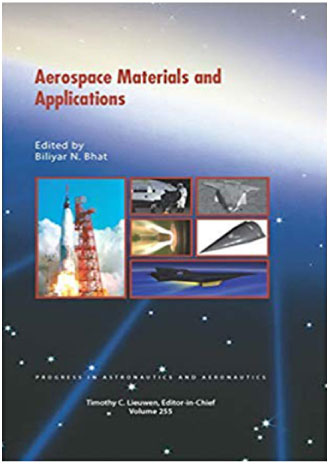
This book is Volume 255 in a world-renown series written for aerospace engineers, material scientists, academics and (when available) for upwardly mobile/high-flying students eager to acquire the theory and practical know-how dispensed by NASA personnel and other close associates.
The content of this 14-chapter book is expertly summarised in the Introduction Chapter 1. ‘Aerospace Materials Characteristics’ – Chapter 2 – runs and runs for almost 200 pages and accounts for almost one-quarter of the book. The text is divided into 12 parts, adjacent parts separated by a copious list of references. Metallurgical aspects and mechanical properties of aluminium alloys, titanium alloys, steels, superalloys and copper alloys are collectively covered in 74 pages. Damage tolerance, hydrogen embrittlement and behaviour of oxygen rich environments add a further 58 pages, whilst polymer matrix composites and ceramic materials extend the text to page 203, with acknowledgements and references completing the Chapter at page 208.
‘Material Selections for Aerospace Systems’ – Chapter 3 – is presented from a design perspective. The authors state: ‘The primary function of a structure is to transmit forces through space with the minimum possible weight and cost’ (page 209), subject only to balancing a variety of other conflicting requirements. Function, shape, process and life cycle are issues discussed. The methodology proposed acknowledges the original work of Ashby, Larson and Pranke and presents several case studies and mathematical formulae that disclose much that is relevant to the selection of metals, ceramics, glasses, elastomers, polymers and hybrid materials.
‘Advanced Nanoengineered Materials’ – Chapter 4 – traces the origin of nanotube technology to a paper written by S. Iijima published in Nature Vol 354, 7 November 1991, pp 56–58. The author also reports that a survey of materials scientists reveals that 78% claimed that nanotechnology was (is) their primary field of interest. See the S curve – Fig. 4.1 (page 276) – which shows the slow introduction of CFRP (1970–2000) into commercial aircraft, followed by a steep rise (2001 to date) with a similar pattern for the introduction of nanotechnology (c. 1991 to date). The chapter provides three case studies: the first relates to adhesives; the second to mission Jupiter; the third to unmanned aircraft systems. The chapter closes with a list of 137 references, more than enough to keep all true nano buffs happy for quite a while.
‘Subsonic Aircraft Materials Development’ – Chapter 5 – traces the evolution and widespread use of traditional metallic materials and notes the ‘slow’ introduction of composites into commercial aircraft structures. See Fig. 5.1 for structural materials used on Boeing commercial aircraft. See Section 5.2.7 for a summary of composite material developments, in both military and Boeing commercial aircraft. Fibre and metal laminates such as GLARE, ARALL and Titanium Graphite TiGr are discussed in Section 5.2.8.2. Composite process development, affordability and assembly issues are also addressed as well as in-service requirements. Hail impact, lightning attacks, temperature and moisture extremes, corrosion and repair are topics that conclude a long and informative spiel at Section 5.2.11.4. Taking two steps back, Section 5.2.9 provides an excellent résumé titled ‘Evolution of Structural Requirements’, which are impressively explained via Tables 5.3 and 5.4, supported by highly relevant text, relating to wing and fuselage design, followed by numerous brief sections on manufacturing methods and issues. The special needs of rotorcraft blades are considered in Section 5.3, where rotor blade fatigue, rotor blade allowables, sand erosion protection and field repair issues are discussed. Six pages on nanotechnology and four pages on additive manufacture conclude the chapter.
‘Materials for Spacecraft’ – Chapter 6 – opens by considering the space environment and the challenges facing materials scientists and designers. Spacecraft and material requirements are discussed and itemised over three pages, see Table 6.1. Flammability and outgassing is first discussed before structural materials, thermal control, radiation shielding, meteoroid debris shielding and optical requirements, and many other important issues are rigorously assessed, culminating in Section 6.15 ‘Lessons Learned’ and Table 6.2, which tabulates 17 tests for detecting deficiencies in design, improper materials selection, defects in material, improper processing, inappropriate assembly and inadequate service. Such are the challenges of spaceflight. The author concludes the chapter by quoting the late Professor Hawking: ‘To confine our attention to terrestrial matters would be to limit the human spirit’ (431).
‘Materials for Launch Vehicle Structures’ – Chapter 7 – initially refers to the operational requirements of early expendable launch vehicles (LVs), such as Atlas reusable systems and the resulting ‘space junk’ (435), concluding with a list of principal players (c. 1990–2009). Contemporary launch vehicle structures are then discussed, and material characteristics considered. Several short sections on contractual requirements, laws and regulations, safety verification and structural qualification follow, including Equation 7.1 (453), which shows how a specific margin of safety of over 22% is allowed. Pitfalls, controversies and engineering judgements are also discussed.
In ‘Materials for Exploration Systems’ – Chapter 8 – the author points out that ‘planting a flag and footprints … doing a survey, collecting samples and returning to earth is prohibitively expensive and creates no in-space infrastructure’ (505), for which reason the author would much prefer to support materials science experiments, conducted under low gravity conditions that space provides. The author suggests that instead of Apollo-type missions, which generate prohibitive recurring cost, ‘we must manufacture in space, we must use in situ space resources and we must have a workforce that is living in space’ (506). Section 8.2 addresses the task of materials processing in space. Section 8.3 considers how in situ propellant production may be achieved, concluding that pursuit of these proposals will facilitate human exploration and ‘eventual establishment of self-sufficient human settlement off Earth’ (526) – see author’s conclusion Section 8.4
‘Thermal Protection Systems and Hot Structures for Hypersonic Vehicles’ – Chapter 9 – provides a peep into NASA’s single-stage and two-stage orbit programmes. The essence of thermal management (passive, semi-passive and active) is clearly explained, and much physical and mechanical data imported. The design of leading edges of hypersonic vehicles warrants close attention. See page 551, where the X-43 Mach 10 leading-edge design is discussed in detail.
‘Aero Engine Materials’ – Chapter 10 – explains that although the working principles of large and small gas turbine engines are essentially the same, the designer of small engines may not (for manufacturing reasons) be able to provide internal blade cooling. One might also note from Fig. 10.1 that the increase in thrust / weight ratio (3.0 in 1956 and 7.5 in 1981) has stalled, it being much the same in 1996 (current ratio not given). Issues such as engine shutdown and fuel consumption are illustrated graphically, before engine evolution is considered in Sections 10.2 and 10.3, the main focus being on blade shape design.
‘Materials for Solid Rocket Engines’ (more often referred to as solid rocket motors) – Chapter 11 – emphasises the importance of using state-of-the-art sealing methodologies and explains why ‘Monolithic single-case configurations have often been the rocket designers dream’ (610), albeit the five-segment reusable solid rocket motor (RSRMV) developed for NASA’s space launch system (SLS) is used as a basis for further discussion. Figure 11.1 provides a schematic of the five primary components: casing, insulation, liner, propellant grain and ignitor motor. Section 11.2 details various chemical combinations typical of propellant grain, fuel source, oxidizer and binding agents. Section 11.3 covers motor casing design and construction. Section 11.4 covers insulation materials such as elastic polymers derived from nitrile butadiene rubber (NBR), and white asbestos fibres embedded in NBR rubber are also mentioned as a legacy material. Issues such as mechanical and thermal performance and processing are also discussed. Hybrid rocket propulsion systems are considered in Section 11.8, before Section 11.9 ‘Summary, Trends and Outlook’ concludes an informative chapter.
‘Materials for Liquid Propulsion Systems’ – Chapter 12 – notes that Earth-to-orbit launch vehicles may be propelled by either solid or liquid fuels. However, the authors point out that whilst solid rocket motors are cheaper to manufacture and are good value for cost, liquid propellant engines offer higher performance at greater cost. How liquid propellant rocket engines work is clearly explained in Section 12.2. This is followed by a historical review spread over several pages. The meat of the chapter (so far as technical buffs are concerned) lies in the extensive coverage of design considerations and material section issues (649–695).
‘Advanced Materials for Space Propulsion’ – Chapter 13 – addresses the requirements of separation from the LV and subsequent orbital manoeuvring and station keeping control. The authors explain that liquid storable and liquid cryogenic chemical fuels are used. See Table 13.1 for details of propellant combinations used to produce thrust via a de Laval nozzle, the geometry and pressure distribution of which are informatively explained, before specific propulsion systems are discussed, namely: the Hall system – Section 13.4, solar thermal system – Section 13.5, nuclear thermal propulsion – Section 13.6, solar sail propulsion – Section 13.7; tether propulsion – Section 13.8 and ending with Sections 13.9 ‘Advanced Propulsion’ Technologies’ and 13.9.5 ‘Very Advanced Propulsion Systems’.
‘Materials for Power Systems in Space Exploration’ – Chapter 14 – considers the design, working principle and use of six different sources of power, the choice of power source depending on the level of power and the duration for which it is required. All are clearly defined in Fig. 14.1. Thereafter the six options are discussed in detail. ‘Solar’ – Section 14.2 – describes photovoltaic (PV) cells as essentially p-n semi-conductor devices. ‘Fuel Cells’ – Section 14.3 – are electrochemical devices that utilise anodes and cathodes. ‘Batteries’ – Section 14.4 – informs the reader that lithium ion batteries are currently first choice, on account of their high specific energy and significantly lower weight. Radioisotope power systems (RPSs) are described in Section 14.5 and fusion power in Section 14.6. Specific material requirements and design features are of course well-covered. The chapter and book conclude with a pie chart – Fig. 14.30 – which shows the distribution of mass within a typical spacecraft: Power 28%; Structure 21.7%; Payload 26.7%; Guidance, Navigation and Control 8%; Communication 7.5%; Propulsion 3.7%; Thermal 3.4%. The author concludes by stating: ‘Power systems are key components of spacecraft, and advanced materials will enable future space power systems’ to reduce mass and increase payload and reduce launch cost (783).
The publishers deem this text suitable for aeronautical engineering professionals, materials scientists, senior technicians and technical managers already employed in the aerospace industry, but do not invite high-flying aero/material students to seek out and study the text, most of which is at a technical readiness level (TRL)A of 8–9 and much else at levels 6–7. All of which lies well within the grasp of those who, given time, will surely realise the ambitions expressed by those who have contributed to this excellent book.