Introduction
Dealloying has emerged as a convenient and versatile method for making nanoporous metal with high structural definition. Dealloying is the selective dissolution of less noble elements from an alloy, leaving behind a porous structure. The current interest in interface-controlled phenomena displayed by dealloyed nanoporous metals and their potential applications reflects the relative ease of manufacturing nanoporous materials using a simple ambient-temperature corrosion process, as well as the general interest of the materials community in nanomaterials.
The interest in nanomaterials, one of the current trends in materials science, started out from the thought that pushing the characteristic scale of the microstructure down to the 2–5 nm range might maximize the number of defects in a material. New material behaviors were expected through mixing local properties of matter in the core of the defects into the more conventional behavior of crystalline matter.Reference Gleiter1,Reference Gleiter2 Owing to their modified atomic short-range order, grain boundaries were the defects of choice in early studies of “nanocrystalline” materials, and this class of solids remains the subject of active research.
Subsequently, it was recognized that a materials design strategy based on maximizing the number of operando tunable interfaces by manipulating electronic structure could yield additional new behavior.Reference Gleiter, Weissmüller, Wollersheim and Würschum3 This requires control of the space-charge region at interfaces by external stimuli. Nanoporous metals afford an implementation of this strategy—their pore space can be filled with electrolyte, and the capacitive coupling between the ionic and electronic conduction paths in the electrolyte and the metal, respectively, provide for control of interfacial electric charge (Figure 1).Reference Weissmüller, Viswanath, Kramer, Zimmer, Würschum and Gleiter4
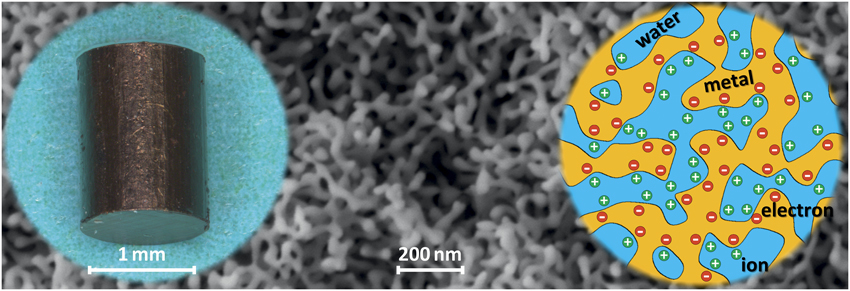
Figure 1. Nanoporous metal network structures with interface-controlled behavior. Dealloying can produce macroscopic samples, such as the millimeter-sized cylinder of nanoporous gold (NPG) on the left, exhibiting a uniform network structure with characteristic strut or “ligament” size in the nanometer range, as can be seen in the scanning electron micrograph of NPG in the background. Adding an aqueous electrolyte in the pore space as a second component creates a hybrid nanomaterial in which the constituent metal and water phases are intermixed at the nanoscale. Polarizing their interface creates space-charge regions, indicated on the right, which store energy or allow the behavior of the interface to be tuned.
Importantly, dealloying can be used to tune the characteristic structure size down to few nanometers, so that the suggested interface-controlled behavior of the nanomaterial can indeed be achieved. Various schemes for exploiting this behavior have emerged in the past decade, specifically, in such instances where the nanoporous metal is converted into a hybrid material by adding aqueous solutions in the pore space as a second phase, which is intermixed with the metal at the nanoscale. The interface between the fluid and the metal can store energy, provide functionality for sensing or actuation, or contribute strongly to the material’s mechanical behavior. In several instances, suggested operando tunable properties have been demonstrated based on this scheme.
Various aspects of dealloying as a preparation scheme for nanoporous metals have been the subject of an earlier issue of MRS Bulletin.Reference Erlebacher and Seshadri5 Since then, the preparation approaches have seen drastic progress due to liquid-metal dealloying strategies that enable dealloying of more application-relevant materials. Cutting-edge characterization techniques such as x-ray tomography and focused ion-beam serial sectioning can now reveal the complex topological structure of the material at the nanoscale in three dimensions. This promotes a substantially improved understanding of the mechanical behavior of these nanoporous metals, and the meshing of topology- and interface-related aspects in controlling strength and stiffness. Furthermore, new perspectives for exploiting the interface-controlled materials behavior of nanoporous metal in applications are emerging, specifically in the area of bioanalytical and biomedical applications, and in electrochemical energy conversion and storage. The articles in this issue of MRS Bulletin highlight these current trends, and this introductory article places them into perspective.
Dealloying—From corrosion science to the physics of dealloying mechanisms
Nanoporous gold and several of its congeners (variants of a common chemical structure) were discovered within the context of stress-corrosion cracking of noble metal alloys such as Ag-Au and Cu-Au.Reference Sieradzki and Newman6 The behavior of these alloys was of particular interest, since the electrochemical conditions for which cracking occurs is at least 500 mV more positive (depending on alloy composition) than the potential for hydronium ion or water reduction. Early transmission electron microscopy studies revealed that the corrosive attack of solid solutions of comparatively noble elements creates a layer that is enriched in the more noble element and exhibits porosity at an extremely fine scale.Reference Forty7 During extended attack, the porous layer thickens and can initiate brittle-like fracture of these otherwise ductile alloys.Reference Sieradzki and Newman6 This form of stress-corrosion cracking was an early motivation for the study of electrochemical dealloying.
In the context of stress-corrosion cracking, the mechanical properties of the porous layers hold obvious interestReference Sieradzki and Newman6 and motivated the first studies of the mechanical behavior of nanoporous metals.Reference Li and Sieradzki8 It has been hypothesized that the mechanism of this cracking involves the nucleation of a high-speed crack within a nanoporous layer that subsequently grows into the parent-phase material (which has not been dealloyed) for distances of the order of several microns prior to crack arrest by plastic processes.Reference Sieradzki and Newman9 At this point, a new nanoporous layer forms at the arrested position of the crack and the process repeats. The rate-limiting step in the overall cyclic cracking process is the formation of the nanoporous layer. Recent work has shown that nanoporous gold can support cracking at a velocity of 200 m/s, which is about 50% of the limiting crack velocity in this material (i.e., the Rayleigh wave velocity).Reference Sun, Chen, Badwe and Sieradzki10
Our current understanding of ambient-temperature electrochemical dealloying of alloys such as Ag-Au, Cu-Au, and Ni-Pt is based on the notion that connected preexisting atomic-scale paths of the more electrochemically reactive component (Ag in the case of Ag-Au alloys) must exist in the alloy for selective dissolution to occur to depths greater than a few tens of nanometers.Reference Sieradzki, Corderman, Shukla and Newman11–Reference Erlebacher13 Today, this general mechanism of dealloying is referred to as percolation dissolution.
Other possible mechanisms involving, for example, solid-state mass transport cannot account for the rather sharp compositional dependence of selective dissolution, known as dealloying thresholds.Reference Sieradzki, Corderman, Shukla and Newman11 The dealloying threshold signifies the composition of the more reactive component below which percolation dissolution and the evolution of nanoporous structures does not occur. In the case of Ag-Au alloys, this is about 60 at.% Ag.Reference Sieradzki, Corderman, Shukla and Newman11
Percolation of the more reactive component is a necessary condition for selective dissolution. But it is not a sufficient condition since the open space created by dissolution must allow for electrolyte penetration and the development of an electrochemical double layer. Standard percolation thresholds do not ensure that the open-vacancy spaces produced by dissolution are large enough, nor do they address effects of short-range ordering or clustering that likely affect the magnitude of percolation thresholds. There have been several suggestions in the literature addressing these issues within the context of so-called high-density percolation.Reference Sieradzki, Corderman, Shukla and Newman11,Reference Artymowicz, Erlebacher and Newman14
In addition to the dealloying threshold, another key parameter in characterizing dealloying is the critical potential, which defines the onset of percolation dissolution for an alloy at a composition above the dealloying threshold.Reference Sieradzki, Corderman, Shukla and Newman11,Reference Sieradzki12 In a description of a crystal surface as composed of terraces, step edges, and kinks,Reference Ibach15 the critical potential signifies the onset of dissolution of the more reactive component from highly coordinated terrace sites.Reference Erlebacher13,Reference Erlebacher, Aziz, Karma, Dimitrov and Sieradzki16 Below the critical potential, dissolution of the more reactive component only occurs from surface sites of low coordination, which is a process that eventually results in passivation, as the more noble component accumulates on the surface.Reference Erlebacher, Aziz, Karma, Dimitrov and Sieradzki16 Above the critical potential and for compositions below the dealloying threshold, terrace dissolution can occur, resulting in the injection of surface vacancy clusters only a few monolayers in depth.Reference Oppenheim, Trevor, Chidsey, Trevor and Sieradzki17,Reference Geng and Sieradzki18 Figure 2 shows a dealloying morphology diagram for Ag-Au alloys, which conveniently summarizes the above issues visually.

Figure 2. Morphology diagram for AgpAu1–p alloys electrochemically dealloyed at ambient temperature in acid electrolytes. The dashed white vertical line corresponds to the dealloying threshold, the black line is the compositionally dependent equilibrium Ag+/Ag electrode potential, and the red line corresponds to the compositionally dependent critical potential. Note: PD, percolation dissolution; SVCs, surface vacancy clusters.Reference Geng and Sieradzki18
Atomic-scale simulation of dealloyingReference Sieradzki, Corderman, Shukla and Newman11,Reference Erlebacher13,Reference Erlebacher, Aziz, Karma, Dimitrov and Sieradzki16 supports the morphology diagram of Figure 2 in the case of silver-gold alloys. For the “percolation dissolution” scenario, in which bulk nanoporosity can be formed, Figure 3 illustrates the important steps of the microstructure evolution during percolation dissolution.Reference Krekeler, Straßer, Graf, Wang, Hartig, Ritter and Weissmüller19

Figure 3. Kinetic Monte Carlo simulations, as established in Reference Sieradzki, Corderman, Shukla and NewmanReferences 11 and Reference Erlebacher13, of atomic-scale dealloying processes during percolation dissolution. (a) The planar surface prior to dealloying. (b–e) Illustration of the sequence of vacancy island nucleation, surface roughening, formation of a branched pore channel network, and coarsening. Gray and yellow spheres denote Ag and Au atoms, respectively.Reference Krekeler, Straßer, Graf, Wang, Hartig, Ritter and Weissmüller19
Intense interest in dealloying as a route to the manufacture of porous nanomaterials evolved only after it was shown that the dealloying pattern formation process could be understood in terms of modern concepts of driven processes in alloys far from equilibrium.Reference Erlebacher, Aziz, Karma, Dimitrov and Sieradzki16 That same study also suggested the use of nanoporous metals for sensing applications.
The article by McCue et al.Reference McCue, Karma and Erlebacher20 in this issue describes recent progress in our understanding of dealloying mechanisms based on the morphology of the dealloyed structures, providing considerable information on the transport processes involved in selective dissolution. McCue et al. discuss experimental and state-of-the-art simulation approaches aimed at identifying atomic-scale processes and the driving forces for various forms of dealloying. Liquid-metal dealloying, a process first described by C. Wagner,Reference Harrison and Wagner21 offers additional routes for the creation of nanoporous metals that are not easily accomplished by electrochemical dealloying. In this approach, a liquid metal that has a finite solubility for one alloy component and essentially zero solubility for the other(s) is used to dealloy the parent-phase alloy. These approaches may allow for the development of technologically relevant low-cost, low-weight nanoporous metals that have a variety of as yet unexplored applications.
Porous nanomaterials with interface-controlled functionality
An early demonstration of the potential of dealloying-made nanoporous metals as functional materials was provided in a study showing actuation with nanoporous gold.Reference Kramer, Viswanath and Weissmüller22 Later work showed that actuation occurs with other nanoporous metals made by dealloying,Reference Bai, Si, Zhang and Zhang23–Reference Shi, Markmann and Weissmüller28 and that actuation behavior could be similarly realized by employing gas phase adsorbates.Reference Biener, Wittstock, Zepeda-Ruiz, Biener, Zielasek, Kramer, Viswanath, Weissmüller, Bäumer and Hamza29 The actuation is driven by the variation of a capillary force, the surface stress, with the electric potential at electrode surfaces. This suggests coupling between electrochemistry and mechanics,Reference Haiss30,Reference Weissmüller, Alkire, Kibler, Kolb and Lipkowski31 which may be connected to stress-corrosion cracking, but which also motivates interest in the mechanical properties of nanoporous metals. Most importantly, nanoporous metal actuators exemplify interface-controlled behavior, in which the defining functional property, actuation, arises because interfacial parameters—in this case, the surface stress—control the response of the material to external stimuli such as variations in electrical or chemical potentials.
Sensing transducer schemes with these nanoporous metals confirm the potential of interface-controlled material behaviors for applications such as functional materials. As just one example, piezoelectricity—a phenomenon ordinarily reserved for ceramics—has recently been demonstrated in nanoporous gold.Reference Stenner, Shao, Mameka and Weissmüller32 As illustrated in Figure 4, electric signals are generated when the numerous metal–electrolyte interfaces in the nanoporous material are strained. Other sensing schemes explore electric-field enhancement in the pore space during illumination by visible light or infrared radiation for surface-enhanced Raman scattering.Reference Ding and Chen33–Reference Zhang, Lang, Hirata and Chen35

Figure 4. Example for sensing with a nanoporous metal-based hybrid nanomaterial. (a) Applying a macroscopic cyclic strain, ε*(t) (t: time), while holding the electrode potential, E constant, leads to a displacement of electric charge, Q. Holding Q constant leads to variation of E. Note the strong electromechanical response, analogous to piezoelectricity. Inserts illustrate local polarization of the electrochemical double layer at the surface of the ligament. (b) The ligaments of the nanoporous gold are idealized as cylindrical struts in (a). (c) Experimental setup for electromechanical response in a dynamic mechanical analyzer. Note: RE, reference electrode; CE, counter electrode; WE, working electrode (sample), respectively, in electrochemical cell. Pushrod applies the strain.Reference Stenner, Shao, Mameka and Weissmüller32
The Şeker et al. articleReference Şeker, Shih and Stine36 in this issue describes a particularly intriguing sensing scheme using nanoporous metals. Interface control is again the crucial aspect; the large effective surface area ensures that the entire material contributes to the transduction signal (either optical or electrochemical) when target biomarkers adsorb. Nanoporous gold stands out because of easy surface modification via thiol-gold linker chemistries, which afford specific functionalization by a variety of biomolecular probes. That and other recent phenomena, including biochemical and biophotonic applications, are summarized in this contribution. This article also describes device structures based on nanoporous metals that are conveniently fabricated by lithographic approaches, emphasizing the potential for applications.
The Chen et al. articleReference Chen, Ding and Chen37 in this issue summarizes current approaches that explore applications of nanoporous metals for energy storage. Each of these approaches exploits the synergy between interfacial effects, the bicontinuous microstructure, and the relatively high mass-specific surface area that can be achieved in these materials. The electrically highly conductive metal skeleton provides for fast electron transport in supercapacitors or lithium-ion storage, while the large interface area allows for efficient charge-exchange reactions. Furthermore, lithium-ion exchange with alloys represents a quasi-reversible alloying-dealloying process that is efficient and may provide a future alternative to intercalation approaches for ion storage. Current research in this field provides new perspectives on fundamental questions in electrochemistry and metallurgy, which are highlighted in this contribution.
Mechanical behavior controlled by topology and interfaces
Applications of nanoporous metals as interface-controlled functional materials require good mechanical properties, motivating strong current interest in their plastic and elastic behavior. These materials have already demonstrated good strength and ductility, encouraging their study as model systems for a new class of structural materials. As compared to engineered truss structuresReference Schaedler, Jacobsen, Torrents, Sorensen, Lian, Greer, Valdevit and Carter38–Reference Bauer, Meza, Schaedler, Schwaiger, Zheng and Valdevit40 as an alternative current approach toward load-bearing small-scale networks, dealloyed metals are distinguished by their scalability. Whereas lithographic approaches can create samples containing about 1000 struts, nanoporous metals can contain 1018 ligaments per cm3. The vision of structural materials made by dealloying is therefore not entirely out of the question. The mechanical behavior of these materials can be significantly improved when the pore space is infiltrated with a second phase, such as epoxy resinReference Wang and Weissmüller41 or a second metal.Reference McCue, Ryan, Hemker, Xu, Li, Chen and Erlebacher42
Details of the topology in the corrosion-made network of nanoscale ligaments are crucial for their mechanical behavior. Contrary to truss structures in which the network geometry can be designed, nanoscale pattern formation during dealloying is self-organized and microstructural evolution during the subsequent coarsening proceeds spontaneously. The topology of these structures as well as its connection to active processes during corrosion and coarsening are the subject of current research.
The Lilleodden and Voorhees articleReference Lilleodden and Voorhees43 in this issue describes how emerging experimental approaches enable exploration of the geometry and topology of nanoporous metals in three dimensions made by dealloying. Tomographic reconstruction based on transmission electron microscopy, focused ion-beam sectioning, and synchrotron radiation experiments are being used for this purpose. The article addresses the issue of identifying the geometric and topological parameters that control material behaviors. Information on the distributions of curvatures and interface orientation may be relevant, and the topological genus as a measure for “connectivity” emerges as an important factor. These parameters document the pathways followed by the microstructure during coarsening; their knowledge is required for deciding whether dealloyed nanoporous metals with different structure sizes are self-similar. Issues of topology are increasingly recognized as crucial for understanding the material behaviors of nanoscale network structures and their mechanical properties.
Active research on plasticity and elasticity of nanoporous gold connects to fundamental questions about mechanical properties at small length scales. The reproducible synthesis, high structural definition, and wide range of ligament size of nanoporous gold make it an emerging model material for fundamental studies of size- and interface effects.Reference Biener, Hamza and Hodge44,Reference Mameka, Wang, Markmann, Lilleodden and Weissmüller45 The Jin et al. articleReference Jin, Weissmüller and Farkas46 in this issue summarizes available observations from experiments and numerical modeling. The article highlights the role of topology, and discusses surface effects including excess surface elasticity, as well as the impact of surface stress and surface tension on plastic deformation. As a particularly promising approach in the field of small-scale plasticity, the article highlights experiments in which the surface state can be electrochemically modulated and how this affects plastic flow. Experiments with nanoporous gold are unique in enabling direct examination of surface effects on plasticity via the operando tunable plastic behavior made possible by electrochemical functionalization schemes.
Perspectives
The articles in this issue highlight selected aspects of research into nanoporous metals fabricated by dealloying. They outline a field that draws much of its appeal by connecting equally to fundamental issues in mechanics, materials, and nanoscience, as well as to tangible applications, including functional and structural materials. Besides the examples covered here, there are several other important active branches of research in the field, including intense interest in catalysis with nanoporous gold.Reference Ding and Chen33,Reference Zielasek, Jürgens, Schulz, Biener, Biener, Hamza and Bäumer47–Reference Wittstock and Bäumer51 There is also emerging interest in controlling dealloying protocols in order to evolve hierarchical porous microstructures.Reference Juarez, Biener, Weissmüller and Hodge52 This issue of MRS Bulletin provides insights into the current state of the art in a field of research that is active and that has the potential to provide an array of positive surprises in the future.
Acknowledgments
J.W. acknowledges support by Deutsche Forschungsgemeinschaft through SFB 986, Subproject B2. K.S. gratefully acknowledges the support of this work by the US DOE Basic Energy Sciences under Award DE-SC0008677.

Jörg Weissmüller is a full professor and head of the Institute of Materials Physics and Technology at Hamburg University of Technology. He is also the leader of the Hybrid Materials Systems Group at Helmholtz-Zentrum Geesthacht, Germany. He studied materials science at Saarland University, Germany, and the University of Dundee, UK. He received his PhD degree in engineering and the Habilitation degree in experimental physics from Saarland University. He has worked at the Institute of New Materials, Germany; the National Institute of Standards and Technology, and the Institute of Nanotechnology at Karlsruhe Institute of Technology, Germany. His current research focuses on interfaces and nanomaterials with interface-controlled behavior, with emphasis on the coupling between mechanics and chemical or electrochemical processes. Weissmüller can be reached by email at [email protected].

Karl Sieradzki is a professor of materials science and engineering in the Ira A. Fulton School of Engineering at Arizona State University. He obtained his PhD degree in materials science and engineering from Syracuse University, and has held previous positions at the Ames Laboratory/Iowa State University, Brookhaven National Laboratory, and Johns Hopkins University. He served as a co-chair for the 1996 MRS Fall Meeting in Boston. His current research interests include mechanics/fracture of solids, stress-corrosion cracking, thermodynamics of surfaces and interfaces, and electrochemical dealloying. Sieradzki can be reached by email at [email protected].