1 Introduction
Regardless of whether it is explicitly considered or not, engineered products generally have three impact areas tethered to them. They are economic impact, environmental impact, and social impact. These three areas are the basis for sustainable design as introduced by Elkington (Reference Elkington1997), and adopted by others (Howarth & Hadfield Reference Howarth and Hadfield2006; Buchert et al. Reference Buchert, Neugebauer, Schenker, Lindow and Stark2015; Reuter Reference Reuter2016). Sustainable design seeks to develop products that have maximum positive impact and/or minimum negative impact on the economy, environment, and society (Brundtland Reference Brundtland1987; McDonough & Braungart Reference McDonough and Braungart2002).
Economic sustainability – often tied to profitability – has long been a regularly considered area of impact in product development, while environmental and social sustainability (McDonough & Braungart Reference McDonough and Braungart2002) have not. However, growing awareness of contemporary issues such as resource depletion (Cardinale et al. Reference Cardinale, Srivastava, Duffy, Wright, Downing, Sankaran and Jouseau2006), the circular economy (Bermejo Reference Bermejo2014), and corporate social responsibility (Garriga & Melé Reference Garriga and Melé2004) has caused various organizations to consider becoming more fully sustainable in their products, services, or operating practices, while maintaining desirable economic performance.
As a way of injecting a sustainable culture into an organization, some have created a position for sustainability officers (Gacso & IEMA 2015) and have tried to implement sustainable thinking into their product development process. While this has potentially raised awareness of sustainability at all levels of the organization, it has not changed the fact that the tradeoffs between economic, environmental, and social sustainability can be obscured and not intuitively resolvable by the organization’s general body of decision makers (Tobias et al. Reference Tobias, Figge, Pinkse and Preuss2010). Unfortunately, this condition often relegates sustainable design to a philosophy that many agree with in principle but find difficult to execute (Matar, Georgy & Ibrahim Reference Matar, Georgy and Ibrahim2008; Short et al. Reference Short, Lee-Mortimer, Luttropp and Johansson2012).

Figure 1. The sustainability space, defined by the three pillars of sustainable design; economic, environmental, and social sustainability. The shape within the space, represents the set of feasible design alternatives, and the region shaded darkly represents the optimal tradeoff surface, or more formally the Pareto frontier. We seek Pareto solutions because they represent the best that can be feasibly achieved.
To support decision makers and their organization’s desire to become more sustainable, this paper presents an approach for exploring design tradeoffs as they relate to sustainability. Specifically this paper characterizes the Sustainability Space, which is a set of design alternatives positioned within a three-dimensional geometric space defined by economic, environmental, and social sustainability objectives, as illustrated in Figure 1. While potentially useful in all stages of the product development process, the framework presented here is specifically for the redesign of an existing product. As such, it is assumed that enough design information is available to construct parametric models of product performance and sustainability – which is not an unrealistic assumption for companies that have become well-established in a particular industry. From these models, however basic or rudimentary they may be, a set of design alternatives can be generated by changing the models’ parameter values and the sustainability space can be found.
To be clear, the definitions used throughout this paper for environmental impact and social impact are: the effect an engineered product has on the natural world, and the effect that an engineered product has on the day-to-day quality of life of persons or communities, respectively. For the purpose of this paper, the latter definition excludes such issues as manufacturing workers’ rights and community cohesion in the location of the production facility, as these issues are less likely to be influenced by product design decisions, and more likely to be influenced by supply chain decisions.
We note that this paper does not attempt to contribute a new optimization technique to the literature, but instead uses existing methods found in multiobjective optimization literature to characterize and navigate the sustainability space. These techniques have not been presented in the literature as a way to find the sustainable design space, but doing so can provide benefit to product design teams seeking a quantitative technique to consider the design space created by the three top-level objectives of sustainability. Along with building the design space, we also provide guidelines for converging on a final sustainable design.
Before presenting the approach, we briefly review pertinent related literature upon which the present paper is built (Section 2). In Section 3, five steps for finding and exploring the sustainability space are presented. These steps are demonstrated in Section 4 as a machine for drilling for water wells is redesigned for greater sustainability. Section 5 provides our main conclusions from the research and delineates its limitations.
2 A review of previous work
In this section, we briefly review literature in the areas of sustainable product development, multiobjective optimization, and the way these two areas have mingled in the literature.
2.1 Sustainable product development
Definitions of sustainability vary widely (Holden, Linnerud & Banister Reference Holden, Linnerud and Banister2014); however, the Brundtland report defines sustainable development as development that meets the needs of the present without compromising the ability of future generations to meet their own needs (Brundtland Reference Brundtland1987). Many have interpreted this to include economic, environmental, and social impacts (Howarth & Hadfield Reference Howarth and Hadfield2006; Buchert et al. Reference Buchert, Neugebauer, Schenker, Lindow and Stark2015; Reuter Reference Reuter2016). This paper works in harmony with these definitions and specifically looks at the impact a product will have relative to the three pillars of sustainability.
Although not always considered by design teams, engineered products often have an impact economically, environmentally, and socially (Norman & MacDonald Reference Norman and MacDonald2004). Considering this triple bottom line – as it is often referred to – we can reasonably assert that economic sustainability (when characterized by profitability) has always been a part of product development. In contrast, the same cannot be said for environmental sustainability, which emerged on the agenda in the late 1990s within the product development sector (Brezet et al. Reference Brezet, Van Hemel, Böttcher and Clarke1997; Luttropp & Lagerstedt Reference Luttropp and Lagerstedt2006; Telenko & Seepersad Reference Telenko and Seepersad2010; Yuan & Dornfeld Reference Yuan and Dornfeld2010). It was at this time that life-cycle thinking, which encourages environmental considerations at every stage of the product life cycle (from materials extraction to final disposal at the end of life), grew in popularity and it was recognized that a product’s environmental impact is most effectively influenced when considered in the early stages of the product development process (Goggin Reference Goggin1994; Bhamra et al. Reference Bhamra, Evans, McAloone, Simon, Poole and Sweatman1999). The literature now contains a wide range of methods and tools to support life-cycle thinking including LiDS wheel (Brezet et al. Reference Brezet, Van Hemel, Böttcher and Clarke1997), Eco Indicator 99 (Goedkoop, Effting & Collignon Reference Goedkoop, Effting and Collignon2000), the LEED Rating System (Al-Ghamdi & Bilec Reference Al-Ghamdi and Bilec2015), and more (Witczak et al. Reference Witczak, Kasprzak, Klos, Kurczewski, Lewandowska and Lewicki2014; Walden et al. Reference Walden, Roedler, Forsberg, Hamelin and Shortell2015).
The one branch of the triple-bottom line that has yet to receive much attention in the product development literature is social justice (Missimer et al. Reference Missimer, Robèrt, Broman and Sverdrup2010; Lofthouse Reference Lofthouse2013). Nevertheless, the products developed by organizations do impact society (McDonough & Braungart Reference McDonough and Braungart2002; Garff et al. Reference Garff, Dahlin, Ward and Lewis2014). Unfortunately, social aspects are not often integrated into product development processes and only a few leading-edge companies have progressed beyond ecodesign (Tischner & Charter Reference Tischner and Charter2001; Bhamra & Lofthouse Reference Bhamra and Lofthouse2007). There has been, however, a growing interest in the use of design by foundations and non-governmental organizations (NGOs) to assist with social change, particularly in relation to the challenges of resource-poor countries (Acharya et al. Reference Acharya, Adesina and Blair2008; Mattson, Wood & Renouard Reference Mattson, Wood and Renouard2017). While sustainable design is emerging as an important approach for industry to adopt, research has shown that current sustainable design approaches tend to focus on only a small number of environmental issues such as recyclability, material selection, and energy consumption. Consequently these have limited ability to result in large-scale sustainability improvements (Brezet Reference Brezet1997).
There has however been some progress in considering all three pillars together. For example, Buchert et al. developed an early stage method to simultaneously consider all three pillars of sustainability to assist in choosing material and manufacturing process (Buchert et al. Reference Buchert, Neugebauer, Schenker, Lindow and Stark2015). And others have successfully applied a full sustainable evaluation for a specific product (Erickson et al. Reference Erickson, Burkey, Morrissey, Reynolds, Robinson, Ronnebaum, Wagner, Singh, Natarajan and Pahwa2016).
2.2 Multiobjective optimization
As organizations seek sustainable design solutions, there will inevitably be tradeoffs between economic, environmental, and social sustainability. The field of multiobjective optimization offers existing tools and theories to support the management of tradeoffs (Jin & Azarm Reference Jin and Azarm2001; Marler & Arora Reference Marler and Arora2004; Deb Reference Deb2014).

Figure 2. The general concept of Pareto optimality for two objectives being maximized. The gray shaded space represents feasible solution space and the dark curve represents the set of Pareto solutions (non-dominated solutions).
Multiobjective optimization is fundamentally different than single objective optimization in that it must consider the tradeoffs between competing objectives before a final single solution can be chosen. As such, multiobjective optimization problems generally result a set of design alternatives that are non-dominated mathematically (Pareto Reference Pareto1927). These are called Pareto solutions, the set of which comprises the Pareto frontier as shown in Figure 2 where both objectives are maximized. Pareto solutions are defined as non-dominated because there are no other feasible designs for which all objectives are the same or better.
There are two basic optimization strategies for solving multiobjective design problems. The first strategy takes the multiple objectives and combines them into one objective and from that point treats the problem as single objective. The second strategy is to generate a set of design alternatives – all belonging to the Pareto frontier – from which the decision-making body chooses the most desirable one. Neither method is without criticism (Das & Dennis Reference Das and Dennis1997; Messac Reference Messac2000; Messac & Mattson Reference Messac and Mattson2004; Pandey, Mourelatos & Nikolaidis Reference Pandey, Mourelatos and Nikolaidis2013).
Regardless of what optimization strategy is used, the design will need to be represented mathematically in some form. Various design tools seek to simplify a product or system and represent the design in alternate formats. Tools such as matrix-based methods and axiomatic design (Farid & Suh Reference Farid and Suh2016) characterize functions and requirements allowing the designer to easily find critical parameters or features of a system. Even within matrix-based methods there are various ways to characterize a product or system. Other tools, such as characteristics property model and property driven design decompose the design and consider either the structure of the product or the functions on an individual basis (Qureshi et al. Reference Qureshi, Eisenbart, Dantan and Blessing2013; Malmiry et al. Reference Malmiry, Dantan, Pailhès and Antoine2016).
2.3 Optimization-based sustainable product development
Various publications describe the search for desirable sustainable solutions. Some are based on traditional single objective optimization techniques (Du Pont & Cagan Reference Du Pont and Cagan2012), others are based on multiobjective optimization techniques (McPhee & Yeh Reference McPhee and Yeh2004; DeVoil, Rossing & Hammer Reference DeVoil, Rossing and Hammer2006; Shahi et al. Reference Shahi, Wang, An, Bibeau and Pirmoradi2012; You et al. Reference You, Tao, Graziano and Snyder2012; Antipova et al. Reference Antipova, Boer, Cabeza, Guillén-Gosálbez and Jiménez2013), and some are not based on numerical optimization at all (Byggeth & Hochschorner Reference Byggeth and Hochschorner2006).
Despite the use of optimization techniques for sustainable design, the multiobjective characterization of the three essential areas of sustainable design is surprisingly missing from the literature. That is to say, we have found no paper that promotes the value in identifying the sustainability space, shows how to identify it, nor how to navigate through it.
A valuable review of multicriteria decision-making for sustainable design is presented by Pohekar & Ramachandran (Reference Pohekar and Ramachandran2004). This review not only examines multiobjective optimization techniques, it also reviews a variety of approaches for aggregating objectives into a single objective. This is appropriate as the overwhelming trend in the papers reviewed by Pohekar and Ramachandran is to aggregate all sustainability issues into one measure that is optimized. In nearly all of the cases reviewed, economic sustainability is one of the issues considered, while in many cases it is considered only in the context of one other sustainability area, be it environmental or social. It is important to recognize that while the tradeoff conditions are considered by the optimizer (computer) when the objectives are aggregated, they are not visible, evaluable, or explorable to the design team or decision makers. While the review carried out by Pohekar is over a decade old, it does provide valuable insight into many techniques sill used today.
More recently, a noticeable quantity of work has been done on optimization-based environmental sustainability. A variety of topic areas are present in the literature including tradeoff resolution between performance and environmental impact (Fitzgerald, Herrmann & Schmidt Reference Fitzgerald, Herrmann and Schmidt2010; Mala-Jetmarova, Barton & Bagirov Reference Mala-Jetmarova, Barton and Bagirov2014); multiobjective optimization in ecodesign (Antipova et al. Reference Antipova, Boer, Cabeza, Guillén-Gosálbez and Jiménez2013); multiobjective considerations of environmental impact (Michalek et al. Reference Michalek, Chester, Jaramillo, Samaras, Shiau and Lave2011); wind farm optimization (Du Pont & Cagan Reference Du Pont and Cagan2012); the search for sustainable systems based on a multidomain optimization formulation (Alfaris et al. Reference Alfaris, Siddiqi, Rizk, de Weck and Svetinovic2010); and the multiobjective evaluation of economic and environmental issues using evolutionary algorithms (Thurston & Srinivasan Reference Thurston and Srinivasan2003; DeVoil et al. Reference DeVoil, Rossing and Hammer2006). Some provide an explicit Pareto-based approach; Shahi et al., do this for the sustainable development of hybrid vehicles (Shahi et al. Reference Shahi, Wang, An, Bibeau and Pirmoradi2012). Others provide a strong link to life-cycle analysis (LCA) (Cortés-Borda, Guillén-Gosálbez & Esteller Reference Cortés-Borda, Guillén-Gosálbez and Esteller2013).
An additional consideration relevant to sustainable design is the role that governmental regulations have on the final design. Current literature has shown that optimization algorithms may successfully include government policies that affect the design space (Michalek, Papalambros & Skerlos Reference Michalek, Papalambros and Skerlos2004; Whitefoot, Fowlie & Skerlos Reference Whitefoot, Fowlie and Skerlos2011). Such inclusion shows great potential in combining policy regarding the environment with other design models to predict design changes based on these policies. If desired, these methods could be easily combined with the method presented herein to get a more complete evaluation of product sustainability.
Despite the large quantity of recent work in this area, few have attempted to include social issues in the optimization. Rossing et al. provide some guidelines for dealing with socio-economic constraints (Rossing et al. Reference Rossing, Jansma, De Ruijter and Schans1997). You et al. (Reference You, Tao, Graziano and Snyder2012) is one of the few papers that explicitly considers economic, environmental, and social objectives. Unfortunately, they do not provide a discussion about the sustainability space, how to find it, or what it means to sustainable product development. Matar et al. (Reference Matar, Georgy and Ibrahim2008) explores project life-cycle phases, project execution entities, and sustainability performance parameters, but like You et al. (Reference You, Tao, Graziano and Snyder2012) does not provide insight regarding the sustainability space as defined by the triple-bottom line.
2.4 Observations from the literature survey
A sizable portion of the literature of the sustainable development literature clearly advocates a triple-bottom-line approach to sustainability (economic, environmental, social sustainability) (Rossing et al. Reference Rossing, Jansma, De Ruijter and Schans1997; McPhee & Yeh Reference McPhee and Yeh2004; DeVoil et al. Reference DeVoil, Rossing and Hammer2006; Matar et al. Reference Matar, Georgy and Ibrahim2008; Michalek et al. Reference Michalek, Chester, Jaramillo, Samaras, Shiau and Lave2011; Shahi et al. Reference Shahi, Wang, An, Bibeau and Pirmoradi2012; You et al. Reference You, Tao, Graziano and Snyder2012; Antipova et al. Reference Antipova, Boer, Cabeza, Guillén-Gosálbez and Jiménez2013). Because these three elements are intrinsically linked, decisions regarding any one of them is best made in the context of all three elements together (Matar et al. Reference Matar, Georgy and Ibrahim2008; You et al. Reference You, Tao, Graziano and Snyder2012). The multiobjective optimization literature provides ways for the tradeoffs between interconnected objectives to be characterized, which lays the ground work for making sustainability decisions while considering all three sustainability elements together (Erickson et al. Reference Erickson, Burkey, Morrissey, Reynolds, Robinson, Ronnebaum, Wagner, Singh, Natarajan and Pahwa2016). Various work has been done that begins to link multiobjective optimization tools to the needs of sustainable design (Pohekar & Ramachandran Reference Pohekar and Ramachandran2004), yet the value of characterizing the sustainability space and using it for decision-making in sustainable design has not been explored (Mattson, Lofthouse & Bhamra Reference Mattson, Lofthouse and Bhamra2015). This paper introduces a deliberately quantified tradeoff space between social, economic, and environmental sustainability that can be used to evaluate all three simultaneously during the design exploration process.
3 Tradeoff exploration using a product’s sustainability space
In this section, we present a 5-step process for exploring the sustainability space. This begins with characterizing (or finding) the multiobjective sustainability space (Steps 1–4), followed by navigating through it, and finally with making a decision based on what was learned in the navigation (Step 5). The five steps are:
(1) Identify sustainability issues
(2) Link issues to parameters
(3) Aggregate parameters
(4) Find sustainability space
(5) Explore sustainability space
The 5-step process is presented as simply what could be done by an organization wanting to explore the sustainability space. We also follow the same 5-step process in the example as it serves to break up a more complex discussion into 5 manageable pieces.
The process presented herein is used to link parameters that define the design of a product to the performance of that product in each of the three pillars of sustainability. The process is built on the following assumptions:
Assumption 1. Design teams directly control independent parameters. These independent parameters define the design features. They include, for example, basic geometry and materials among other things. During the product development process, design teams choose specific values for independent parameters as a way to define a product that meets market needs.
Assumption 2. Design teams indirectly control dependent parameters. Design teams are generally aware of how independent parameters influence dependent parameters. For example, design teams know that certain combinations of geometry and materials (independent parameters) will result in more or less product mass (dependent parameter, in this case). Some design teams explicitly evaluate dependent parameters, others do not.
Assumption 3. Independent and dependent parameters can, in any combination, influence top-level dependent parameters (commonly called design objectives) that are often used in decision-making. For example, the mass of a product (dependent parameter) influences the environmental sustainability as does the material selected (independent parameter, e.g., thermoset plastic versus thermoplastic).
Assumption 4. Sustainable product development decisions can be made in the context of three top-level dependent parameters; economic sustainability, environmental sustainability, and social sustainability (Clark et al. Reference Clark, Kosoris, Hong and Crul2009). As long as the independent parameters are constrained to be within reasonable bounds, the decision should be dominated by these three dependent parameters.
Assumption 5. The following five steps assume that the initial parts of the product development process have already been carried out and a general design concept has been selected. For example, this would mean that if a team were hypothetically modeling a hypodermic needle, the following steps begin after a needle concept has been chosen rather than an open-ended drug delivery mechanism (which could include a capsule or a needle).
We follow the simple and logical 5-step process here to explore the sustainability space. We note that while economic and environmental sustainability are intuitive in nature, social sustainability is not. For this reason, throughout the explanation of the method, brief references to a hypodermic needle will be made, as needed, to clarify certain aspects of the process. A detailed explanation and results of a hypodermic needle example are presented by Michalek, Papalambros & Skerlos (Reference Mattson, Lofthouse and Bhamra2015). No equations or results are presented for the needle as a more comprehensive example of the well-drilling machine is introduced in Section 4.
3.1 Step 1: identify pertinent sustainability issues
The goal of this step is to identify the sustainability issues that pertain to the selected design concept. The output of this step is a list of sustainability issues that the chosen product can influence based on its design. Sustainability is a broad topic and issues pertaining to sustainability for a product may have nothing to do with its design parameters and more to do with distribution or company policies. Eventually impacts that cannot be related to product design parameters will not be considered in this method and must be considered in other ways. However, brainstorming all possible impact issues, regardless of their relationship to the product design, is a good place to start.
To do this, the team can start by simply asking what potential positive/negative impacts can this concept have on the economy (profitability), environment, or society? Tools such as the Design Abacus (Bhamra & Lofthouse Reference Bhamra and Lofthouse2007) can be very useful for facilitating brainstorming of this nature, as can other analysis tools such as the Eco Indicator or the MET matrix (Brezet et al. Reference Brezet, Van Hemel, Böttcher and Clarke1997). Outputs from tools of this nature can be distilled down to a smaller set of unique issues that merit inclusion in the decision-making process.
For example, in the case of a for-profit company, profitability is one of the potentially many important economic sustainability issues. Market demand, production cost, and selling price are others. Likewise, the team may identify the product’s weight, energy consumption, water usage, resource consumption, or carbon footprint to be environmental sustainability issues worth considering. Often less intuitive, but equally important, is the identification of the social impacts of the product. When considering the design of a hypodermic needle, for example, it is valuable to recognize that the needle’s design will have an influence on how painful the needle is to the patient, what vaccines can be delivered with it, and how likely it is that the needle would be used for illegal drug use. Lofthouse (Reference Lofthouse2013) and She & MacDonald (Reference She and MacDonald2014) offer some assistance in thinking about social issues related to products.
It is important to recognize that a given sustainability issue may reasonably fit in more than one of the triple-bottom-line areas (meaning the areas of economic, environmental, and/or social sustainability). For example, the selling price of a product is both an economic sustainability issue and a social sustainability issue, as it directly influences profitability and social inclusion, respectively. In such cases, it is valuable to consider the issue in both categories as it could capture important tradeoff conditions. The reason for this will become more clear in Step 3.
In addition to the three areas listed above, there are some product requirements that may be more appropriately treated as a constraint. For example, phlebotomists expect a certain axial rigidity in the needles they are using to penetrate the skin. The team may reasonably conclude that axial rigidity of a needle is not an economic, environmental, or social sustainability issue. In this case, the team can decide that a certain amount of axial rigidity is needed in order for the trained phlebotomist to do his/her job. As such, it can be categorized as a constraint.
Like all brainstorming activities, this step requires the design team to make sure this phase has considered a diversity of issues, and that the convergent phase has resulted in a filtering of the issues based on the values held by the stakeholders.
3.2 Step 2: link sustainability issues to independent parameters
For this step, the design features that influence the sustainability issues (from Step 1) are identified and mathematical relationships that link them are chosen or created. To be more precise, each dependent parameter is described as a function of independent parameters. The output of this step is mathematical relationships for each sustainability issue that links it to specific design parameters. The result of this step is one or more mathematical equations (
$d$
) that are functions (
$f$
) of independent design parameters (
$x$
). For the
$i$
th dependent parameter (or
$i$
th sustainability issue)

Notice that by Eq. (1), not all independent parameters (
$x$
) will map to all dependent parameters (
$d$
). For this, the notation
$x_{j}^{i}$
is used to mean the
$j$
th parameter in the set
$x^{i}$
, which is the set of independent design parameters pertaining to the
$i$
th dependent parameter.
There are a variety of ways to carry out this step; the mathematical relationships may be based on the physics of the product, or they may be empirically derived from a set of experiments or other data, or they may be simple mathematical relationships based on the designer’s intuition. In linking dependent and independent parameters, Kishita et al. use an ecodesign check list, then examine each checklist item and connect it to product requirements and eventually to independent parameters (Kishita et al. Reference Kishita, Low, Fukushige, Umeda, Suzuki and Kawabe2010). As is the case with many design methods, the design team must choose models and relationships that support their philosophy, such as an eco-efficiency philosophy (Zhu, Wang & Zhang Reference Zhu, Wang and Zhang2014) or an eco-effectiveness philosophy (Hauschild Reference Hauschild2015). The relationships developed should support one or both of these philosophies.
We emphasize that while higher detail, higher fidelity, mathematical models will result in more accurate portrayals of the tradeoff relationships, even low-fidelity models – if made with care – are better than no model at all. To make this clear, consider the skin penetration pain associated with a given needle design. The team could choose to not model pain, given that it is a difficult and uncertain parameter, but not modeling it would either (i) ignore that pain exists, or (ii) rely on the design team’s members to use his or her own mental model of pain. We would argue that most mental models can be sketched as a function. From these sketches simple mathematical models can be extracted using curve-fitting techniques, even those available in ubiquitous software, such as Microsoft Excel. An example of this is provided in Section 4. The value of developing a mathematical representation is that it can then be used in a computational setting to explore various parameter value combinations.
3.3 Step 3: aggregate independent and dependent parameters into single measures of economic, environmental, and social sustainability
In this third step of the process, all the models resulting from Step 2 for economic sustainability are combined into a single measure of economic sustainability (
$S_{\mathit{eco}}$
). The same is done for environmental sustainability (
$S_{\mathit{env}}$
) and for social sustainability (
$S_{\mathit{soc}}$
), separately. The output of this step is three equations, one for each sustainability category, that have been aggregated from the equations created in Step 2. For economic sustainability this can be expressed generically as

For environmental sustainability:

And for social sustainability:

where
$d$
is a set of dependent parameters and
$d\in \{d_{1},d_{2},\ldots ,d_{n_{d}}\}$
,
$x$
is a set of independent parameters and
$x\in \{x_{1},x_{2},\ldots ,x_{n_{x}}\}$
, and
$n_{d}$
and
$n_{x}$
represent the number of dependent and independent parameters, respectively. Note that these single measures are aggregations of all issues categorized as relating to economic sustainability, environmental sustainability, and social sustainability, respectively. This has been done for visualization and decision-making convenience. For issues that have been categorized into more than one sustainability area, their influence is captured in both areas by including it in both aggregate measures.
The most common aggregation approach for creating the measures represented by Eqs (2)–(4), though not without flaws (Das & Dennis Reference Das and Dennis1997), is the weighted sum approach. Some alternative approaches that are not as popular, though they overcome some of the drawbacks, are the weighted square sum method, weighted product method, compromise programing method, and analytics hierarchy process (AHP) method.
3.4 Step 4: find the sustainability space
Once Steps 1–3 are complete, the sustainability space can be identified using traditional multiobjective optimization techniques. The output of this step is a set of Pareto solutions that can be evaluated by the design team. The multiobjective optimization problem formulation in Eq. (5) seeks values of
$x$
that maximize the sustainability measures, subject to constraints:

where the only three objectives maximized are economic, environmental, and social sustainability. Recall that as a result of Step 1, some issues were categorized as constraints. As per Eq. (5), the maximization of the economic, environmental, and social sustainability is subject to those constraints.
There are at least two strategies that could be used to solve this multiobjective optimization problem. One way is to search for a single optimal design based on an aggregate objective function, such as a weighted sum of objectives. When this strategy is chosen, it is important to recognize that the choice of aggregation and weights can significantly affect the outcome. A different strategy is to identify a set of non-dominated solutions that can be considered optimal candidates for the design team to choose from. Any Pareto frontier generation method can be used to identify this set, including the normal constraint method, the normal boundary intersection method, or multiobjective genetic algorithms. This strategy allows the design team to view the whole design space and choose an optimal design accordingly. Both methods have been shown in Section 4: Step 4.
The result of this step is a three-dimensional Pareto surface, which represents the non-dominated tradeoff conditions between the three essential areas of sustainable development. This surface can be incredibly valuable in the decision-making process because it captures the intricacies of the tradeoff relationships and only presents solutions that have already been improved as much as possible without giving up anything in exchange.
3.5 Step 5: explore the sustainability space and choose a specific sustainable design
The Pareto surface resulting from Step 4 can now be explored, which means that the design team can start to understand the nature of the tradeoffs between the three main objectives. Because the space is three-dimensional, a number of traditional visualization techniques could be used to better understand the space.
Upon examining the sustainability space, it will become more clear to the product development team which parts of the sustainability space are desirable to the overall objectives for the product, and which areas are not. From the desirable areas the team should choose a few designs to present to the decision makers. The final decision can then be made based on the tradeoff conditions in the sustainability space, the condition of the constraints, the corresponding values for the independent design parameters, and importantly on the basis of any other unmodeled objective that is important to the stakeholders.
In the specific case of seeking a sustainable design, there is one special condition in the design space that is worth noting here. This condition relates to the concept of weak-Pareto optimality. While not generally of interest in traditional settings, solutions considered weakly Pareto optimal have an interesting meaning in the sustainable design space. To understand this, consider Figure 3. This figure shows two dimensions of interest: economic sustainability and social sustainability. Both are being maximized; the Pareto surface is shown as a heavy dark line. Regions of the Pareto frontier that exhibit very small change in one objective, given very large changes in another are considered weakly Pareto optimal. They are considered as such because while the solutions in the weak-Pareto region are mathematically different in the objective with small changes, they are not different in practice. The traditional view of this concept is that in the weak-Pareto region we always prefer point A. However, this characteristic has an interesting implication in the case where environmental and social sustainability are valued but not nearly as much as economic sustainability. As such, any design in the weak-Pareto optimal region would be desired over Point A because it would have better social sustainability at practically the same economic sustainability value.

Figure 3. The general concept of weak-Pareto optimality for two objectives being maximized. Large changes in
$S_{\mathit{soc}}$
correspond to small changes in
$S_{\mathit{eco}}$
.
While generally deemed useless, it is valuable for the design team to identify areas of weak-Pareto optimality as they may lead the team to decisions that have large improvements in one objective while giving up very little in the competing objective.
4 Example: Village Drill
We now provide an example of how the sustainability space can influence design. We use the 5-step process presented in the previous section as a way of breaking up the complex discussion into meaningful pieces. We do this for the Village Drill, a machine used to drill bore holes for water wells in areas of the world that do not have access to advanced drilling processes (Mattson, Wood & Renouard Reference Mattson, Wood and Renouard2016). The Village Drill is unique because it is human powered and easy to disassemble and transport to a job site. This allows the drill to reach villages in areas that are unable to create bore holes using modern drilling rigs. The drill is currently being used to provide clean drinking water to hundreds of thousands of individuals in parts of Africa, Asia, and Latin America (Mattson et al. Reference Mattson, Wood and Renouard2016).
The Village Drill was designed by Brigham Young University under the direction of WHOlives.org. Five years after its introduction in the market, the impact of this drill was critically evaluated by Mattson et al. (Reference Mattson, Wood and Renouard2016), giving WHOlives.org the opportunity to more deeply assess the drill’s sustainability.
The Village Drill has been chosen as an example in this paper for two reasons: (1) The impact of the drill is documented with data that can be used for creating sustainability relationships, and (2) the relationship between the authors and WHOlives.org allows easy access to product documents normally only accessible to the design team. In this way it creates a realistic situation similar to what a typical design team may experience when implementing the process presented in this paper.
We assume that WHOlives.org wishes to continue producing a drill similar in concept to what is currently being produced (as opposed to producing a drill with a completely new geometry and mechanisms), but the development team has freedom to change the drill dimensions and a few selected features. The general concept that will be modified for sustainable product development is shown in Figure 4.
Drill operation:
The current drill design is operated by 3–4 wheel operators, a slurry pump operator, and a winch operator. The drill is disassembled and transported by truck, cart or by hand to a new drill site. The current assembly consists of six assembly pieces for the main structure, 17 pieces to build the wheel and spokes, and over 80 lengths of pipe just under 1 meter long for the drill string. The wheel operators drill into the ground by continuously rotating the wheel assembly while a winch operator keeps tension on the drill string to prevent the string from wedging itself into the ground. Strategic use of the winch allows the wheel to turn easily while maintaining a good cut at the drill bit. After a full length of pipe has been drilled into the ground the team stops the wheel rotation and attaches another length of pipe to the drill string. They then re-attach the square cross-section kelly bar on the other end of the pipe and continue drilling. This process is continued until the drill team has reached the desired depth for the well. The winch is also used to retract the pipe at the end of the drilling process. The slurry pump is used while drilling to push a water/bentinite mixture down the drill string to remove cuttings from the hole and seal the bore hole walls.

Figure 4. The general drill concept, with drill pipe attached.
4.1 Example: Step 1 (identify sustainability issues)
The first step is to identify the sustainability issues that are pertinent to the current design. For this example, the following is identified.
(1) Economic Sustainability
(a) cost to produce the drill
(b) selling price of the drill
(2) Environmental Sustainability
(a) manufacturing process emissions
(b) shipping emissions
(c) ongoing emissions from drill operation
(3) Social Sustainability
(a) number of people served water
(b) jobs created
(c) potential for driller injury
(4) Design Constraints
(a) structurally safe
(b) geometrically feasible
Clearly this list is not exhaustive but is sufficient to illustrate the process. More importantly, however, the list represents key measures that are important to WHOlives.org and other stakeholders and users of the product. Several more factors could have been considered in each category. Undoubtedly the more detailed and comprehensive we make the list the more accurately we can characterize the design space. In many cases, the design team will need to decide between developing a high-fidelity expensive model or developing a low-fidelity inexpensive model. Both model types are valuable and for this example we have developed a medium-fidelity model to promote a discussion of ways the model could be increased or decreased in scope to meet an organization’s needs.
4.2 Example: Step 2 (link issues to parameters)
The purpose of Step 2 is for the team to link the sustainability issues identified in Step 1 to independent design parameters that define the drill. Figure 5 shows the chosen concept and basic parts of the Village Drill. We have chosen 16 independent variables which include the basic geometry dimensions (
$l$
,
$w$
,
$h$
,
$t$
) for most structural members, the angle (
$\unicode[STIX]{x1D703}$
) of the cantilever beam, the number of spokes (
$n$
) and the maximum depth the drill can achieve (
$l_{d}$
).

Figure 5. Examples of a few of the independent parameters for the Village Drill example.
In the following sections, we show how models can be created to link the identified issues to the independent parameters. These models illustrate that sustainability issues can be considered – at least in a preliminary way – without large expense or extensive expertise, both of which have deterred many from engaging in sustainable design.
For this example, we know – or can discover with a small amount of research – certain relationships that will exist between the independent parameters and the sustainability issues. Figure 6 shows the basic relationships for one of the independent parameters (wheel assembly diameter,
$d$
) to three of the sustainability issues listed in Step 2 with actual data represented by black dots. From this figure we make two essential observations: (1) simple mathematical relationships can be created, given just a few specific values for points along these curves, and (2) knowing or visualizing the relationships for realistic problems is not by itself enough to easily conclude what specific values should be given to the independent parameters. Thus, characterizing the many relationships (which go well beyond the relationships shown, to include those for the many other independent parameters and all higher order effects) is more easily carried out in a computational setting than in one’s mind.

Figure 6. Basic relationships between the wheel diameter and a few dependent parameters. The black dots represent actual available data.
4.2.1 Cost to produce the drill
The cost to produce the drill is a function of the amount of material in the final drill design (including scrap), the amount of welding that is needed for assembly, and the cost of each piece of hardware required for the drill. Specifically, the total cost (
$C_{tot}$
) is

where
$C_{mat}$
is the material cost,
$C_{wld}$
is the cost to weld the individual pieces into the final assembly and
$C_{hdwr}$
is the cost of the nuts, bolts, washers, etc. These are calculated as

where
$A_{i}$
is the cross-sectional area of the
$i$
th member,
$\unicode[STIX]{x1D70C}$
is the material density, and
$C_{i}$
is the cost per gram of the selected material for the
$i$
th member.
$C_{wld}$
is calculated as

where
$D_{wld}$
is the weld perimeter,
$C_{wld}$
is the welding cost per hour, and
$R_{wld}$
is the weld rate in units of mm/hr. Because the basic design of the drill is static we assume the number of welding locations will not change, only the amount of welding required at each location.
4.2.2 Selling price of the drill
WHOlives.org currently sells the drill for $18,000 USD (Mattson et al.
Reference Mattson, Wood and Renouard2016). Their current marketing strategy does not allow them to adjust the selling price based on the cost of goods sold. Because their goal is to bring social benefit to impoverished areas they have decided, for the time being, to hold the selling price at $18,000 USD. They may increase the selling price of the drill in certain circumstances, but for this analysis we will keep the selling price constant. Therefore the equation for
$P$
, the selling price of the drill, is

4.2.3 Carbon footprint
According to the International Organization of Standardization (ISO) the carbon footprint of products (CFPs) should consider ‘raw material acquisition, production, distribution, use and end-of-life’ (ISO 2013). Following this standard, we have summarized the drill’s environmental impact to include manufacturing, shipping, and ongoing emissions. The drill’s ‘end-of-life’ emissions only need to consider the shipping emissions to a recycling plant and from there its emissions are considered in the material acquisition for the next product.
The US Environmental Protection Agency (EPA) publishes best practices and useful data to calculate a product’s carbon footprint (EPA 2011). A general equation they recommend for using is

where
$\unicode[STIX]{x1D700}$
is the emissions,
$\unicode[STIX]{x1D6FE}$
is the activity data (e.g., fuel consumed, or material input) and
$E_{\!f}$
is an emission factor that calculates the emissions based on the activity (EPA 2011). The EPA also provides emission factors for most common processes and is the source for all emission factors used in this example. These emission factors will generate emissions in grams of
$\text{CO}_{2}$
.
Manufacturing emissions:
The major carbon contribution for manufacturing is in acquiring and forming the steel.
$E_{\!f,stl}$
, as defined by the EPA, uses the total mass of steel needed in the product to calculate the carbon footprint due to acquiring and forming the steel. A second major process in drill manufacturing is the welding required for assembly. An emission factor,
$E_{\!f,wld}$
, was used for welding to calculate emissions based on the total amount of electrode consumed. The total emissions for manufacturing the drill are

where
$m_{i}$
is the mass of the
$i$
th member and
$p_{w,i}$
is the total welding required on the
$i$
th member.
This measure is a good example of an opportunity for the design team to increase or decrease the fidelity of the model. The mass of steel being manufactured is proportional to the amount of emissions that are released. A design team may choose to simply use the total mass of the Village Drill as a surrogate model with the understanding that as the mass of the product increases so will the emissions. If this strategy is pursued it will save time on model development as the team will no longer need to choose emission factors or even create the equations needed to report carbon emissions. However by making this simplification, the measure would only show a relative impact on the environment and not the actual carbon emissions. If the parameter-impact relationships are normalized then a relative measure is sufficient for characterizing the sustainability space.
Furthermore, a team may wish to report stronger evidence of improvement to their stakeholders. In this case they may take the model a step further to discover the emission factors for the exact processes within a specific factory they wish to use. This may require several field tests at the factory to develop a true accounting of the emissions their product will have. The team may also decide to use the emission factors and manufacturing costs of several factories as independent variables. This will allow the model to choose the most economical and environmentally friendly solution. Such a model would increase the time and cost to develop, but the increased fidelity may be what the organization or investors require to show increased sustainability. Our medium-fidelity model grants a close approximation to the actual
$\text{CO}_{2}$
emissions during manufacturing, but does not have the added detail of factory-specific data.
Shipping emissions:
Vehicles used for shipping typically have relatively low fuel efficiency and have high carbon emissions. The EPA provides an emission factor for light duty trucks used in shipping. The relationship used for calculating emissions due to shipping is

where
$m_{t}$
is the total mass of the drill in metric tons, and
$D_{shp}$
is the furthest distance, in kilometers, the drill may be shipped from the factory. WHOlives.org ships the Village Drill from a factory in Kenya when the destination is within 2000 km of that factory. Therefore, we assume a worst case scenario and set the shipping distance (
$D_{shp}$
) to 2000 km.
Ongoing emissions:
The drill design implements a slurry pump used to push a water/bentinite mixture down the drill string to assist in the drilling process. This pump uses a 3.7 kW (5 hp) engine and its emissions are calculated as

where
$f$
is the amount of fuel, in liters, required to drill one bore hole and
$E_{\!f,pmp}$
is an emission factor for the pump based on the amount of fuel the pump uses. The variables
$l_{d}$
and
$n_{bpm}$
refer to the life of the drill in months and the average number of holes a drill will make in a month. This data is provided by Mattson et al. (Reference Mattson, Wood and Renouard2016).
4.2.4 Number of people served
Mattson et al. (Reference Mattson, Wood and Renouard2016) have also shown that the number of people who are served water is linearly proportional to the rate at which a drill can produce a bore hole. The measure they use is the number of boreholes produced per month
$n_{bpm}$
. There are many complex factors that determine the actual number of holes produced, many of which are beyond what the drill design can influence. The two drill parameters that influence the hole production rate are the time it takes to drill a hole and the operating costs per hole. The expression can be written as

and

where
$t_{dp}$
is the average time it takes to drill one hole, and
$C_{op}$
is the operating cost to produce one bore hole, both variables have been normalized, as indicated by the
$\hat{[\text{ }]}$
symbol. A proportionality is used here because the number of people who are served water is not equal to the number of boreholes produced each month, nor are the number of holes produced each month equal to the amount of time it takes to drill one bore hole. Instead we do know that if the time it takes to produce one bore hole decreases, then the number of boreholes produced each month will increase, and the number of people impacted will increase at the same rate (Mattson et al.
Reference Mattson, Wood and Renouard2016). Normalization for these two variables, and for normalized variables in future sections, is done after results have been found for each drill design in the population. The data is then normalized between 0 and 1 using the maximum and minimum values.
The parameters of the drill are closely tied to both elements of equation (15). The time it takes to drill a borehole is dependent on the number of operators, the rotation rate (RPM) of the wheel and the number of stops required by the team to attach additional drill pipe to the drill string. The drill time equation, in minutes, is

where
$l_{d}$
is the depth of the cut,
$R_{c}$
is the cut rate in millimeters per rotation and is provided by WHOlives.org.
$n_{\mathit{stop}}$
and
$t_{\mathit{stop}}$
are the number and length of each stop, respectively, and
$t_{\mathit{setup}}$
is the time taken to assemble the drill at the well site before drilling begins. For reference, additional equations and constants used to calculate the borehole drill time are given.







The cost for operation (
$C_{op}$
) considers fuel cost for the slurry pump and worker wages. The equation can be expressed as

where
$C_{\mathit{fuel}}$
is the cost of fuel in dollars per liter and
$W_{\mathit{labor}}$
is the labor rate in dollars per hour. The number of jobs that the Village Drill provides is a social measure in and of itself and is discussed in more detail in the next section.
4.2.5 Jobs created
The number of jobs that the drill creates can be expressed as

The drill needs two workers in addition to the wheel operators for each job. The extra people are required to monitor the slurry pump and operate the winch. This also allows the team to take shifts operating the wheel versus the winch or pump. The number of operators can be expressed as

where
$d_{w}$
is the diameter of the wheel. This equation says that 90% of the wheel circumference is available for operators to use and each operator requires at least 1.2 radial meters to operate the drill. The other 10% of the wheel is unavailable space for operation because this is where the base structure attaches to the wheel. This equation is conditional because we will assume that there will always be space for at least one operator to turn the wheel.
4.2.6 Risk of injury
Injury is an inherent risk found in all machinery, especially machines that require such close human interaction. That injury negatively effects the social impact of the drill. We have, in conjunction with WHOlives.org, identified four failure modes of the drill that may potentially cause injury. They are; (i) the number of stops required during operation, (ii) the potential for the cable to fail, (iii) exposed spoke ends, and (iv) excessive force required to operate. Injury, or risk, ‘may be defined as the measure of probability and severity of an unwanted event’ (Grabowski et al. Reference Grabowski, Merrick, Harrold, Massuchi and van Dorp2000). We use the injury severity score (ISS) as developed by Baker et al. (Reference Baker, O’Neill, Haddon and Long1974) to model severity on a scale of 1 to 6 (minor to maximal/untreatable). Probabilities have been based on data from WHOlives.org.
Required stops:
With the current drill design, the team will drill for about 10 minutes then stop to add another pipe length to the drill string. During this process a few situations arise that could cause injury. First, the coupler used to attach pipes to each other has sharp edges that could cause cuts or abrasions. Second, the nature of the process means there are heavy sections of pipe being handled. Any time heavy pieces of equipment are being moved there is a potential for pinching, wedging, muscle strain, etc. The model for injury during drill stoppage is expressed as

where
$n_{\mathit{stops}}$
is the number of stops required during one drill job and
$\unicode[STIX]{x1D70C}_{1}$
is the probability of injury occurring and
$S$
is the severity of injuries that may occur. Under this scenario, most injuries will be minor (a 1 on the ISS) but it is likely that injury severity up to 2 (moderate) may be experienced. We used
$S_{1}=2$
to ensure the most severe cases would be considered.
Cable failure:
The cable has been included in this model because the event of a cable failure often introduces an unknown and dangerous situation, especially when the cable is under variable tension as it is in this case. When a cable fails catastrophically its behavior is unpredictable and could potentially cause severe injury to nearby operators. Injury due to cable failure is expressed by

where


Spoke end cap exposure:
The original drill design had a plate welded to the end of the spoke, near the handle that operators would grab to spin the drill wheel, see Figure 7a. Later, this plate was removed for manufacturing simplicity, but it leaves the area vulnerable to injury as a finger may get caught in the end of the spoke, see Figure 7b. The potential for injury in this location is expressed as

where


$E_{p}$
is simply a binary value to identify if the end plate is present or not. If it is, then the potential for injury in that location is 0. If there is no plate then the potential for an operator to get a finger caught in the spoke is 1 times the probability (
$\unicode[STIX]{x1D70C}_{3}$
) of an injury occurring.

Figure 7. Spoke and handle design; (a) shows the design with the end cap on the spoke while (b) shows the exposed features without the end cap. This exposed region poses a potential injury risk for fingers.
Force exertion:
The force required to spin the wheel is dependent on the diameter of the wheel. Principles of mechanical design indicate that as the diameter of the wheel increases the force required to produce the same amount of torque decreases. As the wheel diameter shrinks, the operators will have to exert a higher force on the wheel to maintain the required torque on the drill bit. A higher force will result in higher risk of injury which can be expressed as

where


As mentioned earlier, a benefit to developing models in this way is the simplicity in which we can find individual relationships between independent design variables and dependent sustainability impacts. Figure 8 visualizes equations (27), (28), and (34).

Figure 8. Basic relationships between the dependent design parameters and three dependent injury parameters. The black dots represent actual available data.
The potential for injury is the aggregate score of each of the individual injury models. Each equation is normalized and aggregated into the following equation

where
$w_{i}$
represents the weight assigned to the specific injury case. In this model each weight is 1.
Comments on social measures:
It is apparent that these social measures do not have firmly defined methods of measurement as is the case for economic and environmental impact. For example, economic measures can universally be modeled using dollars, and environmental measures may use grams of carbon emissions as a common unit, but social impacts do not have any common units of measure. Additionally, predicting the exact number of people served requires more factors than simply looking at the number of boreholes a drill can produce, most of which do not involve the drill design at all. Furthermore, the potential for, or the impact of, an injury is another measure that simply cannot encompass all possibilities, nor does it have a generally accepted numerical value to quantify it. The purpose of this paper is not to provide the best social measures, but to provide a means for design teams to include social measures in tradeoff analysis, when considering the sustainability of their products.
4.3 Example: Step 3 (aggregate parameters)
With the mathematical relationships identified in the previous step, we can now prepare to carryout the numerical search for the non-dominated designs by establishing the objective functions of the optimization problem. To do this, we revisit the sustainability issues identified in Step 1 and declare that we wish to maximize revenue as the economic measure, we want to minimize emissions as the environmental measure, and for the social measures we want to maximize the number of people served and jobs created while minimizing injury potential. Let us now consider each one.
4.3.1 Aggregate measure of economic sustainability
We chose to define economic sustainability for this example as revenue. Where revenue is represented as the difference between the selling price of the drill and its production cost. Using Eqs (6) and (9) this is represented by

4.3.2 Aggregate measure of environmental sustainability
Environmental sustainability is represented as the sum of the drill’s emissions throughout its life cycle. Therefore, using Eqs (11), (12), and (13), the single measure of environmental sustainability is

4.3.3 Aggregate measure of social sustainability
We aggregate the three social sustainability issues into one measure using a weighted average. Equations (15), (25) and (37) are first normalized and then aggregated as shown.

where
$w_{i}$
has a value of one in each instance.
There are a variety of ways we could have aggregated these issues into single measures. There are various resources available in the literature to help development teams choose appropriate methods of aggregation (Messac Reference Messac2000). While it is not our intent to review these here, we simply wish to point out that indeed the issues can be aggregated into three measures that represent the triple-bottom line.
In the case of the Village Drill, economic and environmental issues have common units of measure ($,
$\text{lbs}-\text{CO}_{2}$
), therefore combining them was a simple task. The same cannot be said for issues regarding social sustainability. This makes weighting these relationships challenging and subjective in many cases. For example, one stakeholder may feel that it is most important to reduce injury as much as possible, even if that means radically decreasing the amount of water provided. This person would then weight injury reduction higher than water provided. Varying opinions on the proper weighting may exist even within a single design team. The challenge of weighting social impact issues is still up for much debate and we do not seek to solve it here. Suffice it to say that much work could be done to develop a method for objectively weighting social impacts. Here we simply allow each issue to have an equal weight of 1 within the aggregation.
4.4 Example: Step 4 (find sustainability space)
Given the outputs of Step 3 we can now carry out the numerical search for non-dominated designs within the sustainability space. The problem formulation captures the details:

where the objectives are normalized between 0 (worst) and 1 (best), and where
$x$
represents the design variables and
$c$
represents the constraints. For this model we have 16 design variables and eight constraints. The constraints are summarized in Table 1. The constraints are enforced to ensure the functionality of the drill and manufacturing feasibility is maintained throughout the optimization process.
Table 1. These eight constraint equations are used to filter out infeasible designs in the Monte Carlo simulation


Figure 9. Sustainability space, normalized between 1 (best) and 0 (worst), with non-dominated solutions represented by the darker point. The solutions with a square and diamond around it are the drill designs that received the best social and economic scores, respectively. The solution with the triangle around it is current Village Drill design shown here for the purpose of comparison, while the solution with a circle around it is used for discussion.
The relationships in Eq. (41) are then used to optimize the drill design. Two separate techniques were used to optimize and a Monte Carlo simulation was used to visualize the design space. The sustainability space is shown in Figure 9. Here, the light gray points represent feasible designs as generated by the Monte Carlo simulation with two million data points. The darker points represent non-dominated design alternatives (Pareto points) as generated by the optimization. Additionally, separate optimization routines were run for various weights between the three objectives. An optimal solution is found for each pillar of sustainability individually as well as an optimal solution for the condition where all the weights are equal in each category. For simplicity of presentation (scaling, and additional parameter discussion), the data is presented in a normalized space where 1 is the best, and 0 is the worst. In a publication setting, three-dimensional spaces can be difficult to visualize, so two-dimensional snapshots of the three-dimensional space are provided in Figure 10.

Figure 10. Two-dimensional snapshots of the sustainability space. The solutions with a square and diamond around it are the drill designs that received the best social and economic scores, respectively. The solution with the triangle around it is current Village Drill design shown here for the purpose of comparison, while the solution with a circle around it is used for discussion. Non-dominated solutions are not highlighted.
4.5 Example: Step 5 (explore sustainability space)
Figures 9 and 10 represent data sets that can be easily interacted with by the development team as a means of exploration. In doing so a significant understanding of the sustainability can be easily understood. Figure 10 shows two-dimensional views of the sustainable design space for the Village Drill. The point with a triangle around it represents the current Village Drill design. This figure also shows that, according to our model, the current Village Drill has a potential to improve in each of the three categories of sustainability.
One key benefit of this approach is discovering the tradeoffs between each pillar of sustainability. In any design setting, tradeoff information can be a tremendous benefit to decision makers, and in this case it is informative to the designers of the Village Drill. For example, Figure 10 shows three points that are the optimal designs in regard to one specific pillar. These points are represented by a diamond, representing the best economic point, circle (best environmental) and square (best social). If WHOlives.org desired to focus only on a drill that maximizes economic profits, then the data suggests choosing the design with a diamond around it. However, this results in giving up performance in the other two sustainability pillars, as shown in the right-most image of Figure 10. This design performs poorly in regards to social and environmental sustainability. As WHOlives.org is a nonprofit organization they may be inclined to select the highest performing design for social sustainability, shown with a box surrounding it. Similar to the best economic design, choosing this design also has its tradeoffs.
The design identified as the Averaged best (shown in Figure 10 with a star) performs reasonably well in each of the three categories. When compared to the best economic point, this design only gives up a minimal amount in economic sustainability while making significant improvements in social sustainability. While it is not the optimal choice for any of the three pillars of sustainability alone, the tradeoff in each is relatively small. Decision makers may be inclined to choose this design over others because it performs well in each of the three categories despite not being the best option in any of them. The key insight gained by this design space exploration approach is that the current drill can improve in each category simultaneously, with significant improvements being realized in economic and environmental sustainability.
Identifying these tradeoff conditions offers a design team an intuitive way to view the sustainable design space for the drill. In turn, they can then use the information to choose a design that best represents the values of the company and society. Figure 11 shows each of the five identified designs and their performance in a few selected sustainability issues.
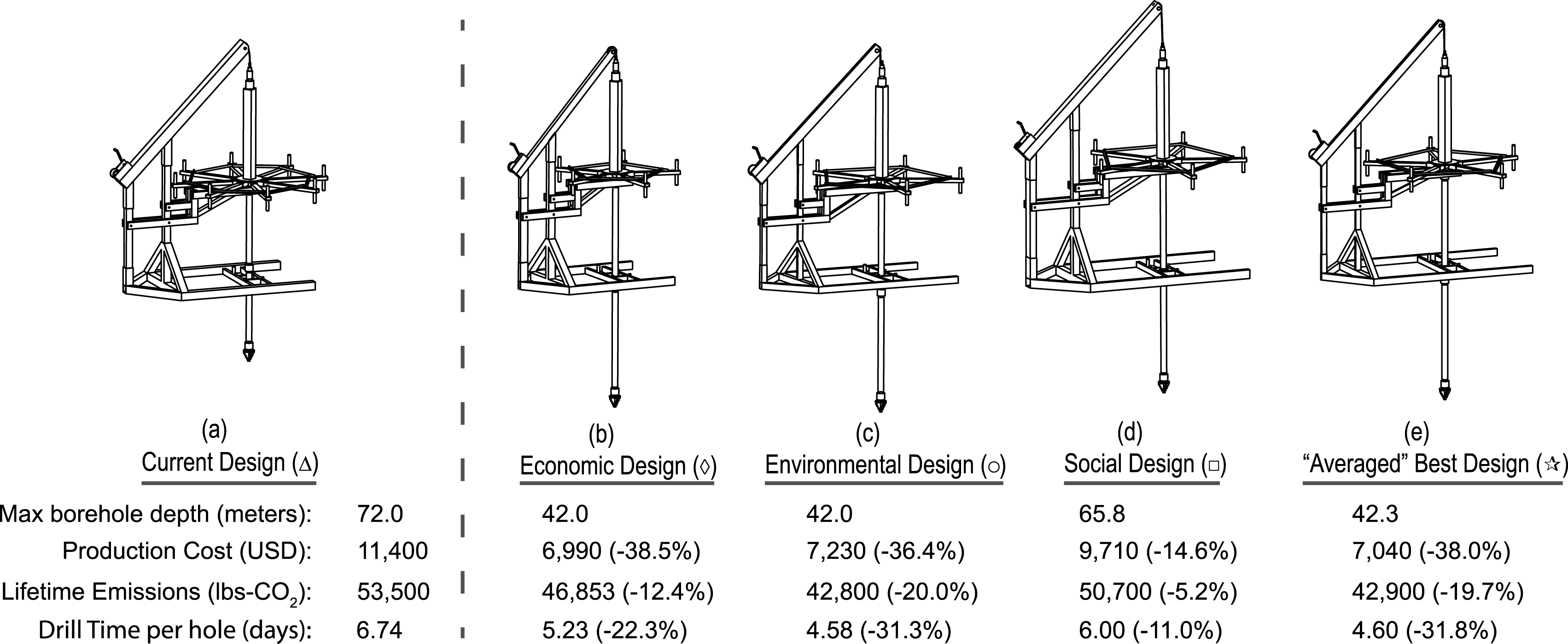
Figure 11. Computer generated drill designs resulting from optimization. Additional statistics are also shown for performance comparison.
The purpose of step 5 is to determine the best potential designs for the drill. This is done by viewing the sustainability space and evaluating the tradeoffs for each design. A few important observations can be made about the exploration:
(1) While it is valuable to visualize the entire sustainability space (as it is easily represented by using the Monte carol approach), the development team will only need to focus on the Pareto solutions as they are by definition the optimal tradeoff surface, where any point on that surface can only improve in one objective by worsening in another. As a side note, the distinct segments in the design space are caused by using discrete values for many of the design variables in the Village Drill.
(2) When examining two-dimensional snapshots as in Figure 10 it is important to recognize that a highly desirable design alternative in one plot, is not always desirable in the other plots. For example, Figure 10 shows two designs – one marked with a square around it and another with a circle. As seen in the center plot, the square point is the design alternative with the best social sustainability. Because there is a natural tradeoff we would expect this point to not be the best design in terms of economic sustainability nor environmental sustainability. This is shown in the left-most and right-most figures.
(3) Figure 10 shows a design with a triangle around it. This solution is the current Village Drill design. The sustainability space shows that there are several designs that are more sustainable than the design that WHOlives.org is currently manufacturing and selling. This kind of understanding, gained by characterizing the sustainability space and exploring it, can be a valuable part of decision-making in sustainable design. This model also implements standard sizes for tubing and hardware, which is important for an optimization model like this because a design team will not be required to round the solution’s beam sizes up or down to the nearest standard size, which if done, will immediately affect the optimal solution.
(4) For this particular problem formulation, there are a few areas of weak-Pareto optimality. These are most easily observed in the center plot of Figure 10. Here we see nearly the same condition described in Figure 3, which, if identified, can significantly affect the decision-making. Similarly, the solution with a circle around will likely be preferred over the one with a diamond around it even though the diamond design is slightly more economically sustainable.
(5) The decision makers can also consider the values of the independent parameters that result in certain designs; this is easily extracted from the computational tool used to characterize the space. For example, the design with the circle around it is a drill design with completely new dimensions from the original drill and increases its performance in each of the three pillars of sustainability.
4.6 Example: discussion
The example of the Village Drill shows that (i) a sustainability space exists for the drill, (ii) it can be characterized with mathematical models, and some experience in numerical optimization. An important message of the example is that the sustainability space is valuable in decision-making. The complexities regarding the sustainability tradeoffs are too great to be understood without computational assistance. Decomposing the sustainability of a product into smaller more manageable issues is an essential part of the presented method. It allows the development team to consider issues of sustainability that can be modeled simply; then it allows the computer to examine all of those simple models simultaneously – leading to insights that may not have been understood by intuition alone.
The results found for the Village Drill specifically are interesting and valuable. All four of the optimal designs recommend reducing the depth capacity of the drill, which results in a smaller segment of villages that can be served by the drill. This seems counterintuitive at first glance, but the optimizer has discovered that it may be more beneficial to drill two holes in two different villages at 42 meters in the roughly two-thirds of time it takes to drill just one hole in a single village at 72 meters. More obviously, the optimizer has been able to reduce emissions, costs, and drill time in every case. These are results that WHOlives.org can use immediately to adjust the design of their drill to maximize their positive impact in each sustainable category.
5 Concluding remarks
In this paper, we have presented a 5-step process for finding and using the sustainability space to support sustainable design decisions. Having worked closely with the ideas presented herein, we can make the following observations:
(1) The identification and use of the sustainability space can bring new insights to decision-making in sustainable design that may not be intuitively discovered otherwise. Its value is significant because it characterizes the tradeoffs between economic, environmental, and social impact – which are the three areas of sustainability our products will influence whether we explicitly evaluate it or not.
(2) The nature of the sustainability space is too complex to characterize and understand by intuition alone. To an extent, this has stalled many sustainable design efforts over the past two decades, which has caused many to believe in the concept of sustainability but abandon fully pursuing it in practice.
(3) While too complex to manage by intuition alone, sustainability can be decomposed into smaller more manageable sustainability issues that can be understood intuitively. This understanding can lead to simple mathematical models (for each sustainability issue) that can be invoked simultaneously in a computational setting to characterize the complex sustainability space.
(4) Although the basis for the ideas presented in this paper center on the multiobjective optimization principle of Pareto optimality (or the principle of non-domination), no complex multiobjective optimization algorithm is necessary to generate the results presented in this paper. In its basic form, very similar results can be achieved using simple Monte Carlo simulations and Pareto filtering. This is significant because it means that little-to-no experience in multiobjective optimization is needed to identify and use the sustainability space. On the other hand, using multiobjective optimization, the design team can guarantee that it has completely and rigorously identified the boundaries of the sustainability space.
This method has limitations and perhaps the greatest of which is that it requires a design concept that can be parameterized (recall that the drill design was defined by the geometrical dimensions of its members:
$l$
,
$w$
,
$h$
, etc). This limits the use of the specific method presented here to product improvements and product redesign as defined by the Brezet model (Brezet et al.
Reference Brezet, Van Hemel, Böttcher and Clarke1997).
A related limitation is that the correctness of the identified sustainability space is based on the correctness of the models used to find it. We must recognize however, that (i) this is true for any model-based design method, (ii) all models exist on a fidelity spectrum, and (iii) a basic part of the product development process includes evolving the models to an appropriate level of fidelity – often over the course of the product development. While the models presented for the Village Drill example are not of the highest possible fidelity, even a model of low fidelity – if made with care – is higher fidelity than no model at all.
Another limitation regarding the mathematics is that we suggest aggregating all social issues (for example) into one measure of social sustainability, and so on. Ultimately we believe that making decisions based on the three-dimensional space defined by single measures of economic, environmental, and social sustainability, justifies this limitation. Nevertheless, any aggregation has the potential to reduce decision-making transparency because it generally requires decision makers to assign preference to the aggregation’s constituent parts. Future work should address the aggregation of impact metrics for each category in the triple-bottom line to improve the value of this model.
Many organizations currently do not approach decision-making for sustainable design in a manner that is compatible with the method presented in this paper. For example, some organizations consider each pillar of sustainability individually and in a hierarchical manner. Generally, applying the method described in this paper to a hierarchical situation eliminates the opportunity to explore the sustainability space as thoroughly. This is simply due to the design space reduction that occurs for each level in the hierarchy, which is caused by the decisions made one level up in the hierarchy. The method presented in this paper is offered as an alternative process that would likely require a cross-functional assessment and consideration of sustainability, resulting in models that accurately reflect multiple impact categories. Notwithstanding the cost of cross-functional collaboration, the presented method provides a powerful opportunity to characterize tradeoffs amongst the three pillars of sustainability, and simultaneously optimize each.
In a real sense, the proposed method requires an appreciation for the multidisciplinary aspects of design. It requires engineers, for example, to consider non-engineering areas more deeply such as those related to the social impact of the product. It requires those who are disinclined toward using mathematical models to value how the models can be used to support design efforts. And it requires those who use the mathematics to translate the outputs into a language and format that decision makers and design teams will engage with. It requires business leaders to distill an organization’s sustainable design goals down to a manageable set that can be reasonably achieved given the organization’s resources. In each of these cases, the individuals involved must be open to expert guidance, as needed.