Nomenclature
- 3D printing
-
Three-dimensional printing
- AMM
-
Aircraft maintenance manual
- ANOVA
-
Analysis of variance
- A-scan
-
Ultrasonic amplitude scan
- ATA
-
Air Transport Association
- Cronbach's alpha
-
Cronbach’s alpha coefficient
- C-scan
-
Ultrasonic composition scan
- FOD
-
Foreign object debris
- GPU
-
Ground power unit
- Hedge’s g
-
Hedge’s measure of effect size value
- MRO
-
Maintenance, repair and overhaul
- N
-
Number of respondents
- p
-
Level of marginal significance within a statistical hypothesis test
- Spec
-
Specification
- SPSS
-
Statistical Package for Social Sciences
- SRM
-
Structural repair manual
- Tuckey HSD test
-
Tuckey Honestly significant difference test
1.0 Introduction
The application of composite materials (a synthesis of two or more materials with different mechanical properties) in aircraft structures has considerably expanded over the past decade, with the introduction of more lightweight passenger aircraft. For example, composites in primary and secondary structural parts of the Boeing 787 account for approximately 50% of the total airframe weight [1], as opposed to approximately 10% for the older generation Boeing 777 [2]. Nevertheless, composites exhibit modes of damage and failure which are not what typically observed in metals. Physical impacts at low velocity/energy can create defects on the composite materials which may promote the degradation of the integrity of the aircraft’s structure and, eventually, have the potential to lead to failures [Reference Dubinskii, Feygenbaum, Senik and Metelkin3]. That includes damage to the lightning protection layer. Impact loads may have a clearly or barely visible effect on the surface of the composite, but they can also be unnoticeable/undetectable via visual inspection, due to the subsurface nature of the induced damage [Reference Dubinskii, Senik and Feygenbaum4]. Classical subsurface damage resulting from a relatively low-energy out-of-plane impact event is dominated by matrix cracking which initiates under the point of impact spreading out in a pyramid pattern in the through thickness direction. Limited delamination may also occur between the layers. Key properties such as in-plane stiffness and in-plane compression strength are compromised due to this subsurface damage. Thus, such damage may be missed by the maintenance personnel when servicing the aircraft and when performing inspection and preventive maintenance to ensure its airworthiness condition.
Understanding low-energy impact events is critical for damage tolerance of composite structures. The Garteur programme is an example of an early initiative to predict and characterise real impact damage in composite structures [Reference Falzon5]. Of course, state-of-the-art non-destructive test technologies such as ultrasonic scanning (A-scan, C-scan) and active thermography play a key role in reliably detecting and sizing damage in polymer composite laminates prior to material removal and repair being performed. Regarding repair strategies, there is still an ongoing need to understand the recovery of structural performance. Riccio et al. recently reported that the stacking sequence of the repair patch plays the main role in the effectiveness of recovering the mechanical performance and overall behaviour of the component [Reference Riccio, Sellitto, Garofano, Ingenito and Zarrelli6]. Overall, bonded flush repairs, i.e. scarf and stepped repairs, are very suitable for the repair of composite load-carrying structures as they provide maximum repair efficiency while keeping a smooth aerodynamic surface. Recent investigations on flush repairs focus on optimisation, durability and reliability. Beyond static behaviour, recent works were reported on damage-tolerant design for bonded repairs, along with fatigue and impact behaviour, that could raise the level of confidence associated with composite bonded repairs [Reference Orsatelli, Paroissien, Lachaud and Schwartz7]. Relatively new technologies such as additive manufacturing also have a role to play going forward. For example, the load bearing capacity of thermoplastic-based open hole laminates was significantly improved through the use of 3D printed patches [Reference Li, Liu, Wang and Zhao8].
The maintenance programmes for aircraft composite structures are still evolving to become more effective, to detect reliably potential defects, and more efficient, to facilitate productivity within the maintenance, repair and overhaul (MRO) service providers. In turn, MRO personnel are expected to understand the safety implications arising from poor handling, damage reporting and repair practices on composite structures [9]. Any limitations in knowledge around these safety-related matters, which might originate from limited awareness and/or insufficient training, can have a significant impact on the effectiveness of maintenance tasks [Reference Wang and Zimmermann10]. Moreover, the relatively short in-service experience with airframe composite materials and non-standardised repair techniques have been identified as safety concerns [9]. The maintenance workforce is predominantly accustomed to inspecting and repairing metallic aircraft structures, having less appreciation on the differences between composites and metals, especially in relation to non-visible or barely visible impact damage [9, Reference Baaran11, Reference Hobbs12].
The current literature surrounding safe handling, maintenance and repair of aircraft composites is heavily focused on the technical issues affecting the inspectability and maintainability of airframe structures [Reference Groves, Beaumont and Zweben13]. Only a few studies have examined safety under the prism of the aircraft maintenance practitioner, such as by Wang & Zimmermann [Reference Wang and Zimmermann10], and these are mostly limited to reports published more than a decade ago by government and aviation regulatory bodies, for example [9, Reference Baaran11, Reference Hobbs12]. However, there is a need for further research, due to the increasing introduction of aircraft types where the utilisation of composites is substantial (especially on large surfaces, such as the outer aircraft skin structure).
The present pilot study intends to explore the level of awareness and understanding of aircraft MRO personnel around handling, inspection and repair of aircraft composite structures, as well as on damage reporting in the case of non-visible or barely visible impact damage. In addition, this research seeks to unveil issues related with the technical/engineering judgement capacity of the maintenance personnel working with composites and to explore the need for specialised education and training. To the best of the authors’ knowledge, this is the first research study attempting to shed a light on these important aspects, which have an effect not only on the safety of composites structures, but also on the productivity of maintenance staff within MRO organisations.
2.0 Materials and methods
2.1 Instrument
The quantitative survey method was selected to address the objectives of this pilot study. The survey’s questionnaire consisted of 25 items, with multiple choice and open-ended questions used. Different types of questions were used in this questionnaire to:
-
• Descriptively identify the issues that have arisen with the introduction of composite materials in maintenance and repairs.
-
• Conduct correlational statistical analysis of the participants’ attitudes and beliefs towards certain aspects and proposed changes in their practice.
For this purpose, items were grouped accordingly to address these two objectives. The 25 items were then evaluated by an academic expert for the tool’s appropriateness. The questionnaire items, as they were formed after the expert evaluation process, can be found in the Appendix. Thematically, the questionnaire was divided in the following sections:
-
• Section 1.0 (Question 1 and 2): Consent and basic demographic information were collected (namely, the participant’s job title).
-
• Section 2.0 (Questions 3 to 9): Participants were asked to answer questions about the causes of impact damage on composite structures. They were also requested to indicate the location of aircraft that the impact damage was most likely to occur, as well as the tools or objects that may get involved.
-
• Section 3.0 (Question 10 to 22): Questions about the composite materials impact behaviour were included in this section to investigate the level of knowledge on low velocity impact damage (Question 11 and 12). The participants were asked about corrective actions following the occurrence of six hypothetical scenario from an impact on the aircraft structure (Questions 10 and 18 to 22). Questions on the background and understanding of the participants on composites’ repair and non-destructive testing also form part of this section (Questions 13 to 17).
-
• Section 4.0 (Questions 23 to 25): The participants’ views were collected on other issues associated with introduction of more-composite aircraft, how impact damage risks can be mitigated within the maintenance environment and on whether there is a need for training of maintenance personnel on composites.
2.2 Sample
The questionnaire was administered to participants recruited from a single aircraft MRO facility. The questionnaire reached participants in online and paper-based formats for ease of access and to enhance participation. An ethics approval was obtained by the Faculty of Science and Engineering of the University of Limerick, with reference 2018_02_04_S&E ‘Potential issues for MRO’s (Maintenance, Repair, Overhaul Organisations) with the introduction of Composite Aircraft’. The process followed the ethics approval guidelines and participants’ confirmation, and anonymity was secured. A target population of 50 participants has been set, with 40 maintenance practitioners returning the questionnaire fully answered.
2.3 Data analysis
The evaluation of the survey results relied on the principles of both descriptive statistics and inferential analysis. In particular, a correlational research design was employed to examine the relationship of the different groups of aviation practitioners and their views and attitudes towards the introduction of composite materials into maintenance and repair [Reference Fraenkel and Wallen14]. Following data screening to address any anomalies, the reliability of similar items was measured using the Cronbach’s alpha. This was followed by descriptive statistics and analysis of variance (ANOVA). All obtained data were quantitatively analysed using SPSS V28.
3.0 Results and discussion
3.1 Questionnaire Section 1
Respondents were grouped into five different categories according to their job title (based on their responses to Question 2). Nearly half of them were licensed aircraft maintenance staff (45%) followed by the aircraft technicians and support staff who were marginally equal in size (25% and 23%, respectively), as illustrated in Fig. 1. The obtained data were screened to identify any anomalies and the reliability of similar constructs was measured using the Cronbach’s alpha. All these Cronbach’s alpha values ranged between 0.53 (for a two constructs comparison, which is acceptable for small numbers of items), 0.76 and 0.89. All results were deemed reliable and therefore acceptable for this research project.

Figure 1. Job titles of the survey respondents.
3.2 Questionnaire Section 2
When respondents were asked on the cause of impact on aircraft composite structures (Question 3), 65% of them gave the impact from ground support equipment as the most frequent one, followed by lightning strike (15%) and bird strike (8%) (Fig. 2). Furthermore, in their responses they detailed that the causes of impact are attributed primarily to cargo/catering/baggage load equipment (47%), passenger stairs/air bridges (39.5%) and aircraft servicing vehicles (11%).

Figure 2. Respondents’ opinion on the most frequent cause of impact on aircraft composite structures.
The areas most affected by impact damage in general, and those areas specifically affected during maintenance, were recorded in the responses of the participants to Questions 4 and 5 correspondingly. It is noted that, for standardisation purposes, the ATA Spec 100 classification [15] was used to identify the different zones of the aircraft. The obtained results, according to the percentile of participants for each area, are summarised graphically in Fig. 3.

Figure 3. Schematic representation of percentile (%) participants’ responses on a) the aircraft structure that most of impact damage occurs (dark grey shaded boxes) and b) most vulnerable locations of an aircraft for damage to occur by impact in maintenance environment (light grey shaded boxes). (This figure has been designed using the airplane image by macrovector available on Freepick.com (https://www.freepik.com/free-vector/airplane-realistic-icons-set_3796055.htm)).
The door area (ATA Zone 800) has been identified by the respondents as the most frequently affected by impact damage (57.5%), with the upper wing surface (ATA Zone 500 or 600) as the second most commonly referred response (17.5%). While, in terms of impact damage within a maintenance environment the responses were almost split evenly between the wing/flap area (ATA Zone 500 or 600) (35%) and the aircraft lower surface (ATA Zone 100) (35%), followed by elevator (ATA Zone 300) (19%).
The results from Questions 6 and 7, on the type of objects/implements/objects likely to lead to impact events in/outside the hangar, are provided in Table 1. Ground support equipment has been considered by the respondents as the most frequent cause, with 55% of the total response received for in-hangar impacts and 65% for outside/on the ramp impacts. Maintenance tooling was the second more probable impact-originator for both cases, nevertheless for in-hangar impacts the responses accounted for 32.5% (as opposed to 15% for outside the hangar). A large difference was anticipated, given the more frequent and more extensive maintenance activity occurring within a hangar, as opposed to lighter maintenance performed outside the hangar (i.e. aircraft servicing and other flight line tasks). Also, foreign object debris (FOD) was not recorded in the responses for in-hangar impact events, while for the outside the hangar case it ranked as the third most probable (12.5%).
Table 1. Participants’ answers on what tools/implements/objects are most likely to be involved in an impact event in the hangar and outside the hangar or on the ramp

Two open-ended questions, Question 7 and 8, were used to record the participants’ views on mitigation measures against the risk of impact damage in and outside the hangar correspondingly. The obtained responses have been summarised and are presented in Table 2. Situational awareness has been highlighted as the most important mitigator, with 39% and 34% of the participants recording that in their responses, against impact damage occurrences inside and outside the hangar correspondingly. Re-evaluation of aircraft docking practice/procedures, protective mats/pads, training and facilities/resources were the other topics of importance reported. The responses for the in-hangar case were almost evenly split between these topics, with a distribution of 18%, 18%, 16% and 9%, correspondingly. Nevertheless, the outside the hangar results are heavily skewed towards training (28%) and facilities/resources (26%). This distribution may be reflective of the different operational environment outside hangar, both in terms of the nature and the tempo of the operations.
Table 2. Participants’ answers on how they believe that the risk of impact damage can be reduced in the hangar and outside the hangar

3.3 Questionnaire Section 3
In this section of the questionnaire the respondents were requested to reflect on their immediate actions in six hypothetical occurrences during the performance of maintenance. Table 3 summarises their answers on whether they would report each one of the six incidents to their engineering manager or turn to the relevant maintenance documentation first. Across the six hypothetical scenarios, 10% to 15% of the respondents would use the relevant documentation to evaluate and report the incident, if necessary, while 67.5% to 87.5% would turn to the consultation of their engineering manager. This may be attributed to the less prescriptive character of maintenance documentation used for the assessment of structural damage of this type. However, this hypothesis needs to be further investigated, as the nature of the aviation maintenance profession and its practice within this, highly standardised, work environment requires the use of prescriptive documentation [Reference Zafiharimalala, Robin and Tricot16]. Access to aircraft type specific maintenance manuals would be required for this investigation. The lack of, or insufficient, instructions on damage assessment can have a negative impact on productivity, as implied by these responses. A higher-than-normal referral of damage cases to the engineering manager may create bottlenecks in the production.
Table 3. Summary of immediate actions taken on six hypothetical occurrences

To further evaluate these results, the Levene’s test was conducted for homogeneity. The obtained p values ranged between 0.63 and 0.75, which means that the one-way ANOVA assumptions have been met. However, the Shapiro Wilk’s test for normality failed to support the normal distribution of the study’s sample, and for this reason, an independent-samples Kruskall-Wallis test was selected. This test was used to investigate the differences of the three different groups of aviation practitioners in the way they would act in these six different scenarios of occurrences in their work practice (Table 3). The three groups are: licensed aircraft maintenance staff (N = 18), aircraft structures technicians (N = 10) and support staff (N = 9). It is noted that the groups of managers (N = 1) and aircraft training instructors (N = 2) were excluded from this analysis as they did not meet the minimum N requirement. The results indicated the differences in the mean scores of the groups’ answers across the three groups of practitioners to be statistically non-significant (p = 0.65). This means that there is 65% probability that these results occurred by random error. In this instance the null hypothesis is confirmed, therefore there is no true difference among the different groups of employees and their answers about their intentions in these different hypothetical occurrences into their practice (see Table 4, Fig. 4).
Table 4. Means and standard deviations of actions on six hypothetical scenarios for the different groups of aviation practitioners


Figure 4. Means of actions on six hypothetical scenarios for the three different groups of aviation practitioners. Extreme values represented with asterisk (*) and potential outliers with circle (○).
Similarly, to compare the responses for nonvisible and visible damages in both composite and metallic structures, independent-samples’ Kruskall-Wallis tests were conducted. The results indicated no statistical significance in the different actions of the participants’ groups when the hypothetical scenarios included the nonvisible damages (p = 0.73). Again, no statistical significance in the different actions of the participants’ groups was identified when the hypothetical scenarios included the visible damages (p = 0.5). Thus, the results from the group of surveyed personnel cannot be generalised to a wider population.
As described in Section 2.1, questions about the composite materials impact behaviour were included in this section of the questionnaire to investigate the level of knowledge of the participants around low velocity impact damage. The results from the two knowledge questions (Questions 11 and 12) are listed in Table 5. The key finding from these results is the high percentage of no responses (‘Don’t know’), accounting for approximately 50% of the participants. This indicates a lack of knowledge. Also, this percentage raises close to 60% when adding those participants who reported values outside the anticipated % of load carrying capacity lost after an impact damage on a sandwich composite (20%–40% loss) and a laminate composite (25%–50% loss).
The results from the questions on the awareness and exposure of the respondents on repair and non-destructive inspections for composites (Questions 13, 14 and 15) are summarised in Table 6.
While most of the participants responded that are not involved in the repair of composites, the results indicate that there is a general knowledge about the typical repairs and inspection techniques. However, the number of responses received between these three questions (Questions 13, 14 and 15) in the field ‘I am not involved in the repair of composite structures’ is inconsistent (Questions 26, 13 and 21 correspondingly). Therefore, these results cannot be analysed further.
Next, the respondents were asked on the frequency of hypothetical actions on two (hypothetical) scenarios on composite structures’ maintenance and inspection (Questions 16 and 17). Table 7 presents the hypothetical scenarios and the results from the responses on the actions, namely ‘Yes, always”’ (ranging from 65% to 47%) and ‘Sometimes’ (ranging from 15% to 3%).
Furthermore, the results were grouped and analysed according to personnel category (licensed aircraft maintenance staff, aircraft structures technicians and support staff), as presented in Table 8. Similarly, for the same groups, the means of actions during routine maintenance and repairs, are illustrated graphically in Fig. 5.
Table 5. Respondents’ opinion on percentage of load carrying capacity lost after a composite sandwich and laminate structure sustains a relatively low velocity impact with a blunt object

Table 6. Responses to questions on composite repair methods and non-destructive testing methods used in the hangar, and on which parts of the aircraft the respondents have performed composites’ repairs
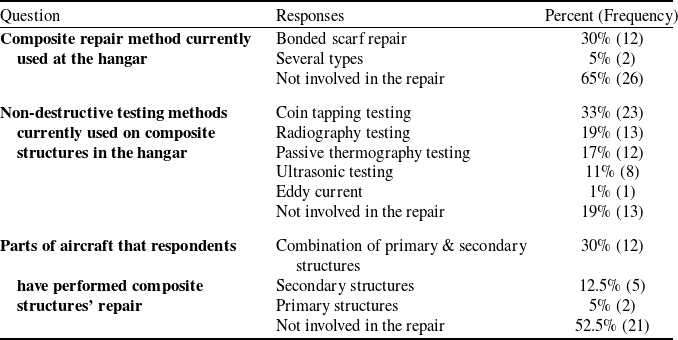
By conducting Levene’s test for homogeneity, the p values ranged between 0.86 and 1, which means that the one-way ANOVA assumptions have been met. However, the Shapiro Wilk’s test for normality failed to support the normal distribution of the study’s sample, and for this reason, an independent-samples Kruskall-Wallis test was selected as appropriate. This test was used to investigate the differences of the three different groups of aviation practitioners in the frequency of their responses to the two hypothetical maintenance and repair scenarios regarding composite structure (Table 7). The results indicated the differences in the mean scores of the groups’ answers across the three groups of practitioners to be statistically significant (p = 0.03). This means that there is 3% probability that these results occurred by random error. In this instance the null hypothesis is rejected, therefore there is true difference among the different groups of employees and their answers on the frequency of their actions regarding the two given hypothetical scenarios (Table 8, Fig. 5). Post hoc Tuckey HSD test were then conducted to identify the pairs of the three groups that appear to have statistically significant differences. These pairs are:
-
• Licensed aircraft maintenance staff – support staff (p = 0.027, Hedge’s g = 1.03), indicating a large effect size and
-
• Licensed aircraft maintenance staff – aircraft structures technicians (p = 0.053, Hedge’s g = 0.96), also indicating a large effect size.
In Table 9 are presented the percentages of the three different groups of respondents that selected the ‘Yes, always’ answer at their two hypothetical actions on composite repairs and inspection. One can observe that the staff is evenly split or almost balanced for the two scenarios (approximately 30%–35%). The low percentage and the uniformity of responses across different categories of staff imply, again, that there may be a need for higher standardisation on composites’ maintenance, repair and handling issues (stemming from a possible lack of sufficiently prescriptive and detailed documentation) [Reference Armstrong17].
Table 7. Respondents’ answers on the frequency of their two hypothetical actions regarding composite structure

Table 8. Means and standard deviations of respondents’ actions during routine maintenance and damage repair of composite structure for the different groups of aviation practitioners
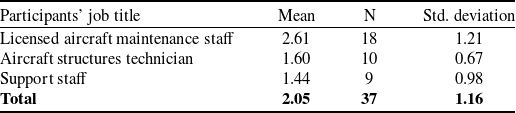
Table 9. Respondents’ answers on the “Yes, always” answer at their two hypothetical actions regarding composite structure
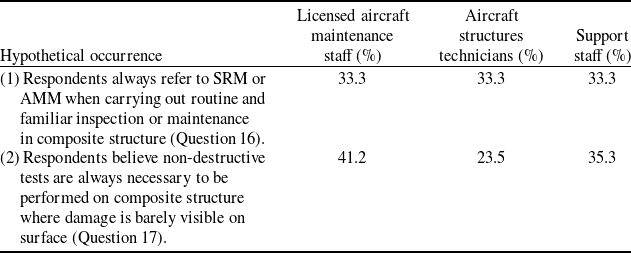

Figure 5. Means of actions during routine maintenance and damage repair of composite structure for the different groups of aviation practitioners. Extreme values represented with asterisk (*).
3.4 Questionnaire Section 4
The final section of the survey, a question attempted to collect the opinion of the participants on broader issues around the introduction of composite aircraft in service (Question 23) and views on the need of focused knowledge and training on composites for maintenance staff (Question 24 and 25). The results of the open-ended Question 23 are summarised in the graph of Fig. 6; facilities/resources are highlighted as the most important aspect (receiving almost half of the responses), followed by training and situational awareness (with 29% and 25%, correspondingly). The potential lack of special tools, apparatus and methods to inspect and maintain aircraft composites appears to be a concern among the aviation practitioners surveyed. Moreover, all identified categories of issues are considered to be indicative of the challenges typically associated with the transition to a less established technology (in this case composite materials) [Reference Derouen and Kleiner18].
Table 10. Respondents’ agreement with statements about more knowledge and training required on composite materials maintenance

Table 11. Means and standard deviations of respondents’ agreement/disagreement on more knowledge and training on composite structures for the different groups of aviation practitioners


Figure 6. Issues with the arrival of a composite aircraft in the hangar that respondents highlighted.
Following, respondents were asked on their agreement/disagreement with statements about more knowledge and training required on composite materials maintenance (Questions 24 and 25). Table 10 presents the ‘Strongly agree’ and ‘Agree’ answers, that comprise of 95% and 100% of the responses, correspondingly. This set of results were anticipated, as both knowledge and training are an important element in aviation maintenance practice. Nevertheless, the difference in the %responses received for the ‘Strongly Agree’ case between the knowledge and training question (45% versus 75%) is of note. This may be reflective of the perception of the respondents around the value of formalised and applied training on composite repairs/maintenance/inspection, as opposed to specific knowledge which may not be necessarily applied. It is also noted that specialised training is particularly important in-situ assessment of composite’s damage [Reference Garnier19], due to the lower impact these techniques have on aircraft grounding time.
Again, by conducting Levene’s test for homogeneity, the p values ranged between 0.60 and 0.64, which means that the one-way ANOVA assumptions have been met. However, the Shapiro Wilk’s test for normality failed to support the normal distribution of the study’s sample, and for this reason, an independent-samples Kruskall-Wallis test was selected as appropriate. This test was used to investigate the differences of the three different groups of aviation practitioners in their agreement/disagreement with statements about more knowledge and training required on composite materials maintenance (Table 10). The results of this analysis are provided in Table 11 and illustrated in Fig. 7, and they indicate that the differences in the mean scores of the groups’ answers across the three groups of practitioners are statistically non-significant (p = 0.09). This means that there is 9% probability that these results occurred by random error. In this instance the null hypothesis is confirmed, therefore there is no true difference among the different groups of employees and their answers about their opinion on more knowledge and training requirements when dealing with composite materials in aviation maintenance and repairs. Thus, the results – findings from this group of participants cannot be generalised.

Figure 7. Means of respondents’ agreement/disagreement on more knowledge and training on composite structures for the different groups of aviation practitioners.
4.0 Conclusion
The present pilot study has explored the views and experiences of maintenance staff working within a single aircraft MRO organisation. Despite the limitations of the sample size of the participants in the survey, this researched revealed a series of issues with an importance for safety and productivity.
The primary findings and conclusions are summarised as following:
-
• The source of impact during in-hangar and outside hangar maintenance, as well as the impacted areas on the aircraft can differ. In the hangar, wing/flap area and the aircraft lower surface are the most heavily impacted according to the responses of the participants. Situational awareness is considered the most profound mitigator against impact damage.
-
• The high percentage of participants that would refer to their engineering manager for instructions on how to handle damage on composites is highlighted (approximately 70%–90%). This may be attributed to the lack of specialised documentation, or the less prescriptive format of the existing instructions contained in aircraft manuals. However, these results cannot be generalised to wider population, due to inconsistencies found in the statistical testing.
-
• The majority of respondents (approximately 60%) did not report the anticipated value range of the load carrying capacity lost due to impact damage on typical composite structures used in aircraft. This is indicative of a lack of specialised knowledge around these topics.
-
• Facilities/resources are highlighted as the most important aspect in the transition to fleets of more-composite aircraft, followed by training and situational awareness. The potential lack of special tools, apparatus and methods to inspect and maintain aircraft composites appears to be a concern among the aviation practitioners surveyed.
-
• While most of the participants responded that are not involved in the repair of composites, the results indicate that there is a general knowledge on the typical repairs and inspection techniques. However, almost all respondents agree on the need for specialised knowledge and training for the handling, repair and inspection of composites. An inclination towards training, as opposed to knowledge has also been indicated, though, again, this cannot be generalised to a broader population.
Future work has been planned for this project, as soon as our collaborating MRO accumulates sufficient experience from composite repairs. Unfortunately, the low volume of work the industry has experienced over the past years, due to the pandemic, has no allowed MROs to gain this experience, which is necessary to expand our research project.
Funding
None.
Authors’ contributions
C. M. Jong: Conceptualisation, methodology, data curation, investigation, software, writing – review and editing. A. J. Comer: Conceptualisation, investigation, methodology, validation, project administration, writing – review and editing. A. V. Chatzi: Formal analysis, methodology, data curation, visualisation, validation, writing – original draft, review and editing. K. I. Kourousis: Data curation, visualisation, validation, writing – original draft, writing – review and editing.
Conflicts of interest
The authors have no conflicts of interest to declare.
Appendix: Questionnaire Survey
The Boeing 787 is manufactured using approximately 50% composite materials. The purpose of this survey is to identify potential issues with the introduction of this aircraft into a maintenance, repair and overhaul (MRO) facility with a particular focus on damage introduced by impact events.
This survey requires 15 minutes.
Section 1
-
1. I have read and signed the consent form associated with this study.
-
• Yes
-
• No
-
2. I am working as a:
-
• Manager
-
• Licensed Aircraft Maintenance Engineer (CAT C)
-
• Licensed Aircraft Maintenance Staff
-
• Licensed Aircraft Maintenance Technician (CAT B1 or CAT B2)
-
• Aircraft Maintenance Mechanic
-
• Aircraft Structures Technician
-
• Aircraft Electronic/Avionic Technician
-
• Support Staff
-
• Other (Please state)
Section 2
-
3. What do you think is the most common cause of impact on aircraft composite structures?
-
• Tools drop
-
• Impact from ground support equipment
-
• Bird strike
-
• Lightning strike
-
• Other (Please state)
-
4. Where in your experience does most of the impact damage occur on the aircraft structures?
-
• Upper wing surface (ATA Zone 500 or 600)
-
• Engine area (ATA Zone 400)
-
• Door area (ATA Zone 800)
-
• Landing gear area (ATA Zone 700)
-
• Other (please state)
-
5. In your opinion, what are the most vulnerable locations of an aircraft for damage to occur by impact in maintenance environment? (You may choose more than one option.)
-
• Elevator (ATA Zone 300)
-
• Aircraft lower surface (ATA Zone 100)
-
• Rudder (ATA Zone 300)
-
• Aircraft Aft Flap (ATA Zone 500 or 600)
-
• Other (please state)
-
6. In your experience, what tools/implements/objects are most likely to be involved in an impact event in the hangar?
-
• Maintenance tooling (plies, spanner, etc.)
-
• Ground Support Equipment (GPU, aircraft service stair, catering vehicle, etc.)
-
• Foreign Object Debris (FOD)
-
• Collide with other aircraft
-
• Other (please state)
-
7. In your experien ce, what tools/implements/objects are most likely to be involved in an impact event outside the hangar or on the ramp?
-
• Maintenance tooling (plies, spanner, etc.)
-
• Ground support equipment (ground power unit (GPU), aircraft service stair, catering vehicle, etc.)
-
• Foreign object debris (FOD)
-
• Collide with other aircraft
-
• Other (please state)
-
8. How can the risk of impact damage be reduced inside the hangar?
-
9. How can the risk of impact damage be reduced outside the hangar?
Section 3
-
10. A composite sandwich structure has been impacted with a blunt instrument with an energy of 14 Joules and it causes a barely visible damage on the structure. What would you do in the case of this?
-
• Report to it to the engineering manager.
-
• Report it only if serious damage is apparent.
-
• Report it when the next inspection is carried out.
-
• Don’t report it.
-
• Other (please state).
-
11. What %percentage of the in-plane load carrying capacity do you think will be lost after a composite sandwich structure sustains a relatively low velocity impact with a blunt object?
-
• 20%
-
• 40%
-
• 60%
-
• 80%
-
• Don’t know
-
12. What %percentage of the in-plane compression strength do you think will be lost after a composite laminate sustains a low velocity impact with a blunt object?
-
• 25%
-
• 50%
-
• 70%
-
• 100%
-
• Don’t know
-
13. Which composite repair methods are used in the hangar currently?
-
• Bonded scarf repair
-
• Bolted repair
-
• I am not involved in the repair composite structures
-
• Other (please state)
-
14. What are the non-destructive testing methods you use on composite structures in the hangar? (You may choose more than one option)
-
• Passive thermography testing
-
• Ultrasonic testing
-
• Radiography testing
-
• Coin tapping testing
-
• I am not involved in the repair of composite structure
-
• Other (please state)
-
15. The composite structures you have repaired are mostly on which part of aircraft?
-
• Primary structures
-
• Secondary structural
-
• Combination of both
-
• I am not involved in the repair of composites structures
-
16. Would you refer to the structural repair manual (SRM) or aircraft maintenance manual (AMM) when you carry out routine and familiar inspection or maintenance on a composite structure?
-
• Yes, always
-
• Most of the time
-
• Sometime
-
• I am not involved in the repair of composite structures
-
17. Do you think it is necessary to perform a complex non-destructive test such as ultrasonic inspection on a composite structure where damage is barely visible on surface?
-
• Always
-
• Sometimes
-
• Not sure about it
-
• I am not involved in the repair composite structures
-
• Other (please state)
-
18. If a tool accidentally drops from around 2 metres height onto a composite wing structure during maintenance, what would you do?
-
• Report to it to the engineering manager.
-
• Report it only if serious damage is apparent.
-
• Don’t report it.
-
• Other (please state).
-
19. If you identify visible damage on an aircraft structure, what would you do in the case of metallic structure?
-
• Report it to engineering manager/line manager.
-
• Not report it.
-
• Report it when the next inspection is carried out.
-
• Other (please state).
-
20. If you identify a visible damage on an aircraft structure, what would you do in the case of composite structure?
-
• Report it to engineering manager/line manager.
-
• Not report it.
-
• Report it when the next inspection is carried out.
-
• Other (please state).
-
21. If you suspect an impact event has occurred on an aircraft structure but there is not visible damage, what would you do in the case of metallic structure?
-
• Report it to engineering manager/line manager.
-
• Not report it.
-
• Report it when the next inspection is carried out.
-
• Other (please state).
-
22. If you suspect an impact event has occurred on an aircraft structure but there is not visible damage, what would you do in the case of composite structure?
-
• Report it to engineering manager/line manager.
-
• Not report it.
-
• Report it when the next inspection is carried out.
-
• Other (please state).
Section 4
-
23. In your opinion, what other issues does the arrival of a composite aircraft in the hangar give rise to?
-
24. Do you agree that the structural maintenance and structural inspection of composite aircraft requires more specific knowledge than metallic aircraft?
-
• Strongly agree
-
• Agree
-
• In between
-
• Disagree
-
• Strongly disagree
-
• Don’t know
-
25. Do you agree technicians need to be trained and certified in order to carry out the composites repair or inspection?
-
• Strongly agree
-
• Agree
-
• In between
-
• Disagree
-
• Strongly disagree
-
• Don’t know