Introduction
Shape-memory polymers (SMPs) are smart materials that are able to fix a temporary shape after a thermomechanical treatment, also denoted as ‘programming’. When applying a suitable stimulus, SMPs are able to almost completely recover the initial shape. In other words, the so-called ‘one-way (1W) shape-memory effect (SME)’ is triggered (Liu et al., Reference Liu, Qin and Mather2007; Dietsch and Tong, Reference Dietsch and Tong2007; Ratna and Karger-Kocsis, Reference Ratna and Karger-Kocsis2008; Pretsch, Reference Pretsch2010; Sun et al., Reference Sun, Huang, Ding, Zhao, Wang, Purnawali and Tang2012; Chalissery et al., Reference Chalissery, Pretsch, Staub and Andrä2019). Here, shape recovery is an entropically driven process based on entropy elasticity according to the theory of rubber elasticity (Holme, 1806). Among stimulus-responsive SMPs that have been investigated so far, thermoresponsive SMPs are the most widely investigated (Yin et al., Reference Yin, Hoffman and Stayton2006; Hoffman, Reference Hoffman2013; Kim and Matsunaga, Reference Kim and Matsunaga2017). After triggering the 1W-SME, an SMP requires another thermomechanical treatment to become thermoresponsive again. By contrast, in the case of the so-called ‘two-way (2W) SME’, an SMP is able to switch between two temperature bistable states without the need for further programming (Chung et al., Reference Chung, Romo-Uribe and Mather2008; Bothe and Pretsch, Reference Bothe and Pretsch2012; Hager et al., Reference Hager, Bode, Weber and Schubert2015; Zhao et al., Reference Zhao, Qi and Xie2015; Zare et al., Reference Zare, Prabhakaran, Parvin and Ramakrishna2019; Scalet, Reference Scalet2020; Ke et al., Reference Ke, Chen, Momo, Jiani, Xuan, Xiaojie and Xueliang2020). For SMPs, the 2W-SME has been investigated on semicrystalline polymers since these materials fulfil the necessary morphological requirements (Westbrook et al., Reference Westbrook, Mather, Parakh, Dunn, Ge, Lee and Qi2011; Zare et al., Reference Zare, Prabhakaran, Parvin and Ramakrishna2019). Here, the main driving forces for the 2W transition are the crystallisation of polymer chains and the melting of the associated crystallites, the same as entropy elasticity (Westbrook et al., Reference Westbrook, Mather, Parakh, Dunn, Ge, Lee and Qi2011; Zhao et al., Reference Zhao, Qi and Xie2015; Schönfeld et al., Reference Schönfeld, Chalissery, Wenz, Specht, Eberl and Pretsch2021). In particular, phase-segregated thermoplastic polyurethanes (TPUs; Kim et al., Reference Kim, Lee and Xu1996; Li et al., Reference Li, Zhang, Hou, Xu, Luo, Ma and Kim1997; Lee et al., Reference Lee, Chun, Chung, Sul and Cho2001; Ji et al., Reference Ji, Hu, Li and Wong2007; Huang et al., Reference Huang, Yang, Zhao and Ding2010; Müller and Pretsch, Reference Müller and Pretsch2010; Pereira and Oréfice, Reference Pereira and Oréfice2010; Pretsch and Müller, Reference Pretsch and Müller2010; Wang et al., Reference Wang, Jin, Ping, Chen, Jing and Su2010; Petchsuk et al., Reference Petchsuk, Klinsukhon, Sirikittikul and Prahsarn2012; Bothe et al., Reference Bothe, Emmerling and Pretsch2013; Liu et al., Reference Liu, Zhang, Huang, Dong, Xu, Wang, Hu and Zhu2016; Ren et al., Reference Ren, Mei, Chen, Zhuo, Chen, Yang, Zuo and Ge2016; Mirtschin and Pretsch, Reference Mirtschin and Pretsch2017), which are built up of hard and soft segments, have proven their potential over chemically cross-linked SMPs due to the capability of mechanical recycling. In the last decade, scientists have unveiled how to implement the 2W-SME into physically cross-linked TPUs (Bothe et al., Reference Bothe, Emmerling and Pretsch2013; Ke et al., Reference Ke, Chen, Momo, Jiani, Xuan, Xiaojie and Xueliang2020; Schönfeld et al., Reference Schönfeld, Chalissery, Wenz, Specht, Eberl and Pretsch2021). For instance, Schönfeld et al. (Reference Schönfeld, Chalissery, Wenz, Specht, Eberl and Pretsch2021) developed a poly(1,10-decylene adipate) (PDA)-based polyester urethane (PEU) and processed it via the additive manufacturing technique fused filament fabrication (FFF). As a result, objects could be obtained that were programmed by tensile deformation at 75°C, cooling to 23°C while holding the elongated shape, followed by unloading. Adjacently, the printed object shrank on heating and expanded on cooling with a maximum thermoreversible strain of 16% (Schönfeld et al., Reference Schönfeld, Chalissery, Wenz, Specht, Eberl and Pretsch2021)). A few years earlier, Bothe and Pretsch (Reference Bothe and Pretsch2012) applied substantial tensile deformation to achieve deformation-induced crystallisation in the soft segment phase of a commercially available PEU. Actuation was dependent on the underlying constant stress conditions. For instance, actuation of 35% occurred in the fifth measurement cycle at 1.5 MPa and of 19% in the 20th cycle at 1.25 MPa. Likewise, significant actuation was verified in other contributions on physically cross-linked PEUs (Behl et al., Reference Behl, Kratz, Zotzmann, Nöchel and Lendlein2013; Fan et al., Reference Fan, Rong, Zhang and Chen2017, Reference Fan, Rong, Zhang and Chen2018a,Reference Fan, Rong, Zhang and Chenb, Reference Fan, Huang, Rong and Zhang2020).
Despite the steadily growing number of publications on 2W SMPs in the last few years, the question arises to what extent actuation can be realised by more complex motion sequences or even by the parallel motion of several parts within a single component. The answer is the design and construction of programmable materials from SMPs and the implementation of the 2W-SME by thermomechanical treatment. Programmable materials are currently the subject of intensive research (Zhang et al., Reference Zhang, Pint, Lee, Schubert, Jamshidi, Takei, Ko, Gillies, Bardhan, Urban, Wu, Fearing and Javey2011; Restrepo et al., Reference Restrepo, Mankame and Zavattieri2016; Berwind et al., Reference Berwind, Kamas and Eberl2018; Fischer et al., Reference Fischer, Hillen and Eberl2020; Jin et al., Reference Jin, Forte, Deng, Rafsanjani and Bertoldi2020; Walter et al., Reference Walter, Friess, Krus, Zolanvari, Grün, Kröber and Pretsch2020; Schönfeld et al., Reference Schönfeld, Chalissery, Wenz, Specht, Eberl and Pretsch2021; Specht et al., Reference Specht, Berwind and Eberl2021; Chalissery et al., Reference Chalissery, Schönfeld, Walter, Ziervogel and Pretsch2022) and use mechanisms on molecular as well as mesoscopic levels to implement information processing. Here, material functionality meets structural design. Complex types of material behaviours can be realised by implementing conditional behaviour (e.g., IF…THEN…ELSE) or design functional dependencies (e.g., E, α = f(T)). Furthermore, programmable materials can be designed to be independent of external power supplies by harvesting environmental changes, for example, temperature changes. Essentially, they can be implemented as self-sufficient materials with complex behaviour based on physical computing, similar to what can be found in nature. Thus, they entail an all-in-one sensor, actuator, controlling unit, and energy harvesting functionality (Zhang et al., Reference Zhang, Pint, Lee, Schubert, Jamshidi, Takei, Ko, Gillies, Bardhan, Urban, Wu, Fearing and Javey2011; Takeuchi et al., Reference Takeuchi, Nakajima, Yoshida, Kawano, Hori and Onoe2022). In this work, a thermoresponsive material is facilitated as a programmable temperature control for a gearbox. The idea is to provide an overheating protection; in other words, the force transmission in gear units is switched from ‘on’ to ‘off’ and vice versa as a result of heating and cooling, respectively. Taking a first step in this direction, the same PDA-based PEU, which was recently developed and characterised by promising actuation (Schönfeld et al., Reference Schönfeld, Chalissery, Wenz, Specht, Eberl and Pretsch2021), was selected as the base material. After developing a gear-like design and rapid prototyping via FFF, the object was thermomechanically treated and actuation was studied while systematically varying the temperature. Following a different design, but addressing the same application, the thermoresponsiveness of a ‘bevel gearbox’ containing 2W actuating elements was examined. With the same idea of transferring a programmable material into bistable temperature states, a third demonstrator was developed and its actuation behaviour was investigated. In this context, it will be shown that the design of the thermoresponsive programmable material leads to the realisation of a considerably larger change in length compared to the pure base material in linear form, which potentially will be able to switch on and off a load bearing structure (Chalissery, Reference Chalissery2023).
Results
In this contribution, a PDA-based PEU, which was developed in our previous works (Schönfeld et al., Reference Schönfeld, Chalissery, Wenz, Specht, Eberl and Pretsch2021; Chalissery et al., Reference Chalissery, Schönfeld, Walter, Ziervogel and Pretsch2022), was selected as the functional base material.
The thermal and thermomechanical properties of the PDA-based PEU were analysed (Figure 1) by means of differential scanning calorimetry (DSC, Figure 1a) and dynamic mechanical analysis (DMA, Figure 1b).

Figure 1. Thermal and thermomechanical properties of PDA-based PEU as determined by DSC (a, second heating and cooling with temperature rates of 10°C·min−1, the enthalpies of melting ΔH m, red coloured area, and crystallisation ΔH c, blue coloured area, are included) and DMA (b, the temperature dependence of storage modulus E’, loss modulus E” and loss factor tan δ at a heating rate of 3°C·min–1).
In the DSC measurement, a broad melting transition, ranging from 29°C to 72°C, with a peak located at 65°C and a crystallisation transition spreading from 52°C to 24°C with a peak at 46°C were detected (Figure 1a). The signals were assigned to the phase transitions of PDA, which served as the soft segment in the phase-segregated PEU. In the DMA measurement (Figure 1b), a similar evolution was detected for the storage modulus E’ and for tan δ as in our previous works (Schönfeld et al., Reference Schönfeld, Chalissery, Wenz, Specht, Eberl and Pretsch2021; Chalissery et al., Reference Chalissery, Schönfeld, Walter, Ziervogel and Pretsch2022). Again, E’ exhibited a two-step decline as associated with the devitrification and melting of the PDA phase. At temperatures of about 65°C and thus above the melting transition of PDA, the hard segments of the PEU ensured that the polymer still had a sufficiently high degree of dimensional stability. The evolution of tan δ exhibited a broad signal at about 7°C, which was assigned to the glass transition temperature T g (Schönfeld et al., Reference Schönfeld, Chalissery, Wenz, Specht, Eberl and Pretsch2021; Chalissery et al., Reference Chalissery, Schönfeld, Walter, Ziervogel and Pretsch2022). The synthesised PEU was processed to filament, which was then used to manufacture demonstrators employing the FFF method.
Next, an object characterised by a gear-like design (Figure 2) was developed. The ‘gear’ was designed in such a way that a compressive load applied during thermomechanical treatment would shift the out-of-plane parts resulting in an entirely flat structure (Figure 2). Specifically, the ‘gear’ consisted of three inverted ‘V’-shaped structures in each line (Figure 2b). The structures were designed to translate any vertical motion directly into horizontal motion. When the ‘gear’ was compressed from top to bottom, the ‘V’-shaped structures bent to form a flat shape, increasing the outer diameter of the ‘gear’ (Figure 2b–g). This change could possibly establish contact with similarly designed objects in a kind of force transmission system. While the gear design obviously maximises the effect of radial change, it could be simple to improve the torque-bearing abilities by radial elements, which also need to expand with the radius. A more elaborate mechanical model will be designed in later iterations.

Figure 2. Technical drawings and an additively manufactured demonstrator for a simplified programmable gear-like object in its (a) isometric view, (b) front view including the dimensions of the original shape, (c–g) the potential shape modifications due to stepwise loading with regard to individual displacements, and (h) after additive manufacturing via FFF. In panels (b–g), the dimensions are provided in millimetres.
The next step was to develop a method for thermomechanical treatment, which later enabled almost stress-free actuation of the ‘gear’. Here, an approach of compression bending was followed by means of a DMA device, which was also used to identify the ideal actuation conditions (Figure 3). It is noteworthy that this approach did not allow the characterisation of length changes with regard to the diameter of the object. In detail, the thermomechanical treatment consisted of heating to 75°C, applying a compressive force of 17 N, ensuring that only compression bending and no pressure crushing occurred, cooling to 15°C, and holding the temperature constant for 30 min, followed by unloading to 0.01 N. In response to the applied compressive force, the height of the object was reduced from 7 mm to 1.8 mm, at which the latter corresponded to the thickness of the ‘gear tooth’. Upon temperature cycling, thermoreversible changes in the height of the object and thus an actuation could be detected in every single measurement cycle, even when the upper temperature Tmax was continuously increased from 55°C to 70°C, while the lower temperature was left at 15°C (Figure 3a). The driving mechanisms of actuation were mostly heating-induced melting of the PDA soft segment, leading to a movement out of the plane of the flat ‘gear’, corresponding to a raising of the object and thus an increase in its height h (Figure 3b), and cooling-induced crystallisation of the PDA soft segment, resulting in the movement back to the rather planar shape of the ‘gear’, along the direction of the compressive force applied during thermomechanical treatment, associated with a decrease in h.

Figure 3. Influence of the selection of Tmax on the actuation of a programmable gear made from a PDA-based PEU. After thermomechanical treatment, a weak external load of 0.01 N was applied: Evolution of (a) changes in object height h/h 0, sample height h (red and blue colour for heating and cooling, respectively) and temperature T (bottom graph) over measurement time t, (b) evolution of object height h upon temperature cycling between 15°C and 58°C, and (c) Δh depending on Tmax (all values are averaged for the second and third thermal cycles). The corresponding states of the gear in (d) its first temperature bistable state characterised by a small outer diameter at Tmax = 58°C, and (e) its second temperature bistable and mostly expanded state, characterised by a maximum outer diameter at Tlow = 15°C. In panels (d,e), the dimensions are provided in millimetres.
Only a small quantity of crystallisable segments was present when selecting a lower maximum temperature Tmax , because a larger part of the PDA phase was still in a crystalline state (Figure 1a), resulting in weak elongation on heating and weak contraction on cooling, as can be seen in Figure 3c, at which Δh describes the evolution of changes in the height of the object under a constant external load of 0.01 N. By contrast, the increase in Tmax can be associated with an increase in the proportion of crystallisable segments, because more PDA crystals were molten (Figure 1a). When selecting a Tmax of 58°C, the most pronounced actuation could be detected, characterised by a thermoreversible change in the height of 39% as averaged for the last two cycles, which can be seen in the associated diagram (Figure 3c). The respective schematic temperature bistable states of the object at 58°C and 15°C are illustrated in Figure 3d,e. They suggest that during actuation, a change in height of 1.5 mm was accompanied by a change in diameter of 4.4 mm. The further increase of Tmax above 58°C gave a decrease in actuation due to the systematic melting of PDA crystals as witnessed in the DSC measurement (Figure 1a), which resulted in the steady recovery of the original shape and thus a lower overall change in h/h 0. In other words, the elongation at the beginning of each cooling step was gradually shifted to higher values and recovered large parts of the initial shape of the object. Obviously, under these conditions, oriented PDA crystals serving as physical netpoints were molten and no longer available to support the structural integrity associated with the respective temperature bistable states of the polymer. The observed decrease in actuation with increasing cycle number is a phenomenon that has already been witnessed many times before (Behl et al., Reference Behl, Kratz, Noechel, Sauter and Lendlein2013; Bothe et al., Reference Bothe, Emmerling and Pretsch2013; Zhou et al., Reference Zhou, Turner, Brosnan, Li, Carrillo, Nykypanchuk, Gang, Ashby, Dobrynin and Sheiko2014; Fan et al., Reference Fan, Rong, Zhang and Chen2018a,Reference Fan, Rong, Zhang and Chenb).
However, for the material investigated here, it could already be shown that the actuation stabilises in a temperature regime between 15°C and 64°C after about 25 heating–cooling cycles (Schönfeld et al., Reference Schönfeld, Chalissery, Wenz, Specht, Eberl and Pretsch2021). One way to estimate thermal actuation is to carry out a temperature conditioning at the higher actuation temperature (Tmax ). In this context, it was demonstrated for the PEU that after deformation and a temperature holding time of 70 hr at 62°C, the length of the sample can be estimated in one of its temperature bistable states (Schönfeld et al., Reference Schönfeld, Chalissery, Wenz, Specht, Eberl and Pretsch2021). Repeated stretching and relaxation at the higher actuation temperature may be an option to ensure that entanglements within the polymer are broken, allowing equilibrium states to be established more quickly.
When investigating the actuation of the PEU, it is important to keep in mind that an exceeding of the upper switching temperature can erase the 2W-SME. In fact, heating to 75°C resulted in a complete recovery to the original shape (Figure 2h), so that thermal bistability was lost. In this context, it will be important in the future to have a precise understanding of the maximum possible temperature under conditions relevant to the application.
Conceptually, the object can be used wherever the change in shape can assure or interrupt the transmission of a force and thus, for example, prevent systems from overheating. An even more precise on/off switch may be realised by introducing programmable materials with structurally bistable states when selecting unit cells containing bridges, which force the material to gain either a first or a second shape (Berwind et al., Reference Berwind, Kamas and Eberl2018). In this case, the transformation between the two radii of such a gear would enable the material to switch to ‘go’ so that a clear coupling/decoupling can be achieved.
In a progressive approach a thermally switchable ‘bevel gearbox’ was developed (Figure 4).
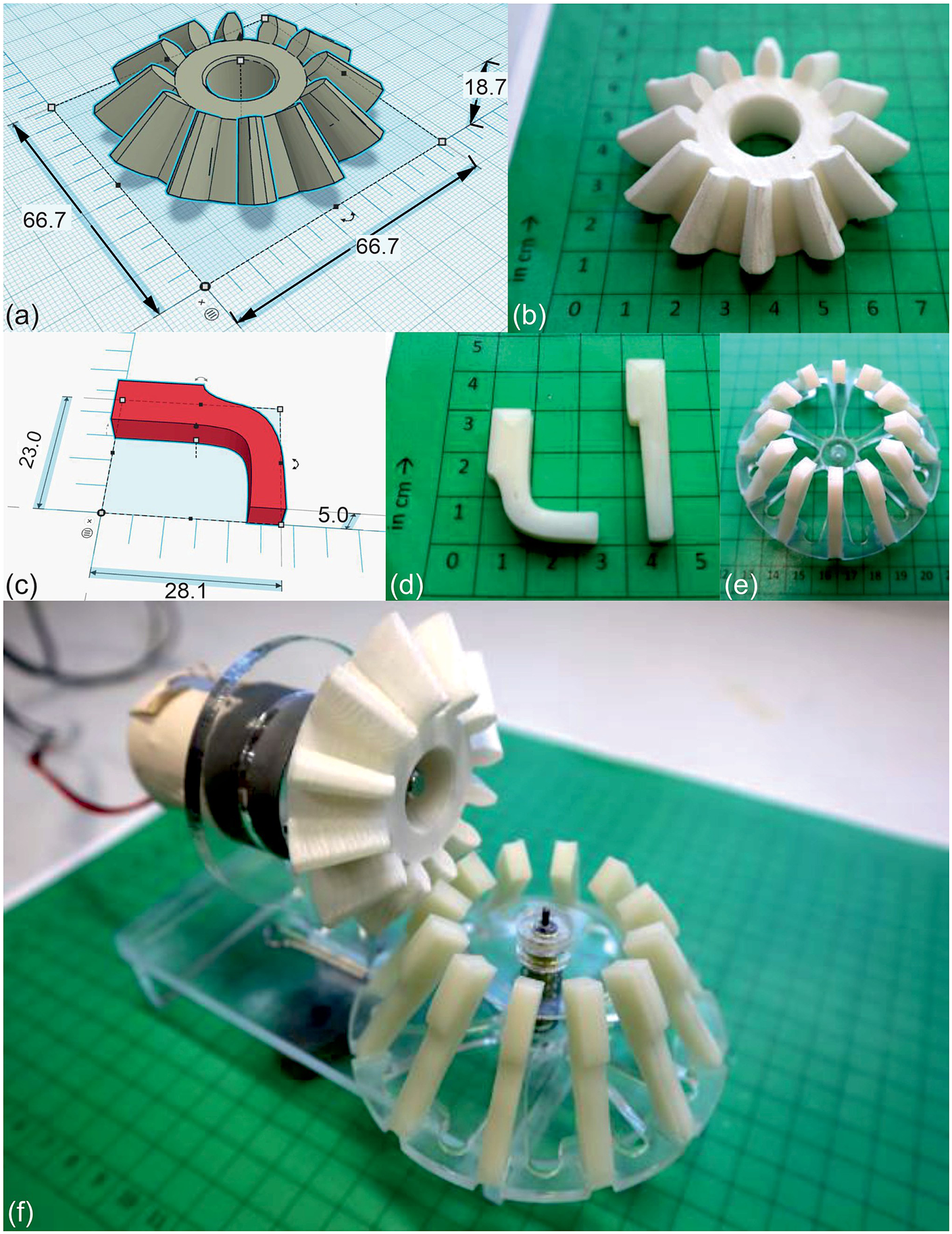
Figure 4. Thermally switchable ‘bevel gearbox’: (a) A technical drawing of the input bevel gear and (b) the additively manufactured ‘output bevel gear’. (c) A technical drawing of one of the ‘teeth’ of the ‘bevel gear’, (d, left) an additively manufactured ‘tooth’, (d, right) a ‘tooth’ after thermomechanical treatment to implement thermoresponsiveness, and (e) the assembled output ‘bevel gear’ containing 12 thermoresponsive ‘teeth’. (f) Gearbox consisting of the input bevel gear and the assembled ‘output bevel gear’. In panels (a,c), the dimensions are provided in millimetres.
The ‘bevel gearbox’ was composed of a standard bevel gear as input gear (Figure 4a,b) and an assembled actuating ‘gear’ as output gear (Figure 4c–e). The standard bevel gear was characterised by an outer diameter of 66.7 mm (Figure 4a). It was additively manufactured via FFF (Figure 4b). For the actuating gear, the individual teeth were first designed (Figure 4c), then additively manufactured by means of FFF (Figure 4d, left) and thermomechanically treated, whereupon they took a straight shape (Figure 4d, right). Later, the 12 ‘teeth’ were mounted on a gear base cut out from a 5 mm thick poly(methyl methacrylate) sheet (Figure 4e). Here, a spring-loaded disc was placed on the top of the base plate, which ensured that the actuating teeth did not completely regain their initial shape if the upper temperature was exceeded. The spring-loaded disc and the teeth were 7 mm apart at 23°C, so that the teeth were in a stress-free state. Finally, the input and output bevel gears were assembled to form a gearbox, whereupon the system was ready to use (Figure 4e). From a design perspective, full gearing was selected to ensure better safety and to allow quick re-engagement of the force at any tooth position during rotation. For functional proof-of-principle, the input gear was set in motion and the temperature was cycled three times between 23°C and 58°C (Figure 5, S1.movie in Supplementary Material).

Figure 5. A thermally switchable ‘bevel gearbox’. The actuating gear switches the power transmission on at about 23°C and off at approximately 58°C.
At 23°C, the input gear and the output gear were in contact, permitting a power transmission (Figure 5). Upon raising the temperature to 58°C, the ‘teeth’ recovered their high-temperature stable shape, which disengaged the power transmission. Later on, cooling to 23°C resulted in the return of the ‘teeth’ into their low-temperature stable shape, which was accompanied by re-engaging the power transmission.
To ensure that programming can also be used to obtain temperature bistable states in other programmable materials and thus to verify distinct actuation with regard to changes in the length of a sample, a unit cell was designed (Figure 6a–d). Additionally, a simulation was conducted to understand the sample behaviour during compressive deformation in course of thermomechanical treatment (Figure 6e,f).

Figure 6. Technical drawing of a unit cell in the perspectives (a) front view, (b) right view, (c) top view, and (d) isometric view. The von Mises stress distribution (e) before and (f) after deformation. In panels (a–c), the dimensions are provided in millimetres.
The unit cell was conceptualised in such a way that the two opposite beams protruded slightly in the middle (Figure 6a–d). When the upper and lower parts of the unit cell were pressed together, the beams pulled outward and reached the maximum bending for each beam segment, as shown in the simulation (Figure 6e,f). It can be clearly seen that the maximum von Mises stresses occurred at the middle part of the unit cell, where the beams protruded.
After three-dimensional (3D) printing, the unit cell (Figure 7a) was found to have an excellent dimensional accuracy when compared to the computer aided design (CAD) model (Figure 6a). Once programmed (Figure 7b), the new shape was stable at 23°C and showed an overall length l of 23.8 mm. Subsequently, the 2W-SME was examined. On raising the temperature to 58°C, the unit cell attained its second bistable state by expanding into the opposite direction of deformation. The resulting shape was characterised by a length of 35.6 mm (Figure 7c). Thus, a change in length Δl of about 50% could be witnessed. Once cooled back to 23°C, the initial bistable state of the unit cell was reached by contraction in the direction of deformation (Figure 7d). This resulted in a decrease in length to 24.6 mm, corresponding to a change in Δl of about 45%. The actuation was proven by another cycle of heating and cooling (Figure 7e,f) and by two further ones (S2.movie in Supplementary Material). Interestingly, the thermal expansion coefficient of an untreated PEU sample between 23°C and 58°C was quantified in a DMA measurement to be about 3.23 × 10—5°C—1 (see Supplementary Figure S1). In so far, thermal expansion made only a small contribution to the proven actuation during heating. Instead, it was the programmed material behaviour that determined the actuation. Apart of differences in the overall shape of the demonstrators, their programming and internal stress distribution, the slightly higher actuation of the unit cell compared to the gear-like object (Figure 2h) is supposed to be also supported by strand orientation during printing (Figure 8).

Figure 7. Unit cell made from PDA-based PEU in its (a) permanent shape as obtained after fused filament fabrication, (b) programmed shape, and (c–f) shapes during switching between the temperature bistable states. In the background, centimetre paper is exhibited (all the dimensions are given in mm).

Figure 8. Strand deposition orientation as obtained with Cura slicer software for (left) the gear-like object and (right) the unit cell.
Indeed, compared to the gear-like object (Figure 2h), the unit cell exhibited a higher proportion of polymer strands arranged parallel to each other and, at the same time, roughly in the direction of force application in the course of deformation during programming. This also suggests a higher degree of order in the unit cell once it had assumed one of the temperature bistable states. However, detailed studies on stress distribution in thermally actuating objects are needed to gain a better understanding of material behaviour.
In summary, the paths taken here lead to significantly higher actuation compared to solid materials, as the programmable materials approach combines the functionality of external structure with the molecular design. More specifically, in one of our previous works, the same PEU as a solid material showed only a maximum thermal actuation of about 16% after programming in which the deformation was introduced by stretching (Schönfeld et al., Reference Schönfeld, Chalissery, Wenz, Specht, Eberl and Pretsch2021). In perspective, significant actuation may assist in opening the door to new applications, for example, in the field of robotics. Reducing the size of the unit cell can help to lower the complexity in previously presented actuating systems. For example, a PEU actuator as functional component of a gripper, as presented in one of our previous works (Schönfeld et al., Reference Schönfeld, Chalissery, Wenz, Specht, Eberl and Pretsch2021), could be produced from smaller programmable materials. Ideally, this also allows material to be saved, so that such approaches can make a contribution to sustainability.
Conclusions
This work unveils that thermoresponsive programmable materials made of PEU are capable of both drastic and complex shape changes, which cannot be witnessed when using classical design approaches for 2W SMPs. This way, the melting and crystallisation of the PEU’s soft segment allowed a force transmission to be activated and deactivated by changing the ambient temperature of a ‘bevel gear’, equipped with 2W actuating elements. Such approaches could, for instance, reduce the complexity and size of grippers. In terms of the design of future thermoresponsive programmable materials, the following strategies would be worth considering:
-
1. The synthesis of PEUs with high-temperature stable switching segments may allow that the 2W-SME cannot be extinguished under clearly defined application conditions.
-
2. Deformation-induced crystallisation during programming may result in thermal actuators, whose soft segment melting temperature stability will be enhanced, when the deformation temperature exceeds the offset melting transition temperature of the switching segment. Here, it is particularly important to find out how great the improvement in thermal stability can be.
-
3. Particularly strong orientations of the polymer chains such as may be introduced by additive manufacturing processes could contribute to higher actuation capability. In this context, further potential should soon arise from activities in the field of 4D printing.
-
4. Approaches like blending of PEUs with distinct actuation could combine the advantageous properties of both partners in one programmable material.
-
5. The combination of different types of programmable materials could be a key to enable more complex switching processes, which could be supported by modifications in the design of the unit cells and their application-specific programming.
-
6. Unit cells may be equipped with wires for heating purposes. This could be done by adapting the printing process, as it creates possibilities for local heating of polymers including complex motion and, in addition, control over mechanical properties.
All of this illustrates that there are multiple opportunities to tailor the properties of thermoresponsive programmable materials for specific applications, further expanding existing capabilities.
Experimental section
Material
The same PDA-based PEU, which was synthesised recently (Schönfeld et al., Reference Schönfeld, Chalissery, Wenz, Specht, Eberl and Pretsch2021), was selected as the base material for this work. The material was used in the form of filament for 3D printing.
Virtual design and fused filament fabrication
The AutoCAD software from Autodesk, Inc., (San Rafael, CA, USA) was employed to design programmable materials in the form of a ‘gear’ and 2W-actuating teeth of a bevel gear. The programmable material in the form of a unit cell was designed and simulated by means of Solidworks from Dassault Systèmes (Vélizy-Villacoublay, Île-de-France, France). The developed CAD models were exported as standard triangle language (STL) files and later used for slicing. After finalising the design of the gears and of the unit cell, Cura 3.6.1 (Ultimaker, Reference Ultimaker2023) was used as a slicer program to generate numerically controlled codes, also denoted as G-codes. The 3D models were imported into the program and sliced into layers according to the predefined printing parameters (Table 1). The most relevant settings for additive manufacturing (AM) are listed in Table 1. To start AM, the generated G-codes were transferred to the 3D printer. The 3D printed objects were produced by FFF using the commercially available 3D printer Ultimaker 3 from Ultimaker B.V. (Utrecht, The Netherlands).
Table 1. Printing parameters selected for additive manufacturing.

Abbreviation: PEU, polyester urethane.
Characterisation of thermal properties
The phase transition behaviour of PDA-based PEU was characterised by DSC using a Q100 DSC from TA Instruments (New Castle, DE, USA). The measurements were conducted on the centre part of an additively manufactured type 5B tensile bar according to ISO 527-2:1996. The sample had a weight of 5 mg.
The PEU was thermally cycled between −50°C and 225°C. For cooling and heating, a rate of 10°C min−1 was applied. The temperature holding time at the minimum and maximum temperatures was 2 min.
Characterisation of thermomechanical properties
The thermomechanical properties of the PEU were studied by DMA. The experiments were carried out with a Q800 DMA from TA Instruments (New Castle, DE, USA) using film tension clamps on multi-frequency-strain mode. A frequency of 10 Hz, a static force of 0.1 N and an oscillating amplitude of 10 μm were selected to investigate the centre part of an additively manufactured type 5B tensile bar according to ISO 527-2:1996. At first, the sample was cooled to −80°C and held there for 5 min, before it was heated to 100°C with a rate of 3°C min−1. In parallel, the evolution in storage modulus E´ and loss factor tan δ was determined.
Programming and characterisation of 2W-SME
The programmable materials made from PDA-based PEU were both thermomechanically treated (programmed) and the actuation was analysed with a Q800 DMA from TA Instruments (New Castle, DE, USA). In order to characterise the 2W-SME, the gear-like object was initially placed between two compression clamps. The chamber was heated to 75°C at the beginning of thermomechanical treatment. After holding the temperature at 75°C constant for 30 min, the object was compressed with a force of 17 N using a loading rate of 1 N·min−1. Then, the deformed object was cooled to 15°C while maintaining the compressive force. The temperature Tmin was maintained for 30 min. Subsequently, the applied force was unloaded with a rate of 1 N·min−1, and the object was heated to 23°C and held at that temperature for another 5 min to mark the end of programming. The actuation of the programmable material was studied under a constant external load of 0.01 N by cycling the temperature. In detail, the sample was heated from 23°C to Tmax = 55°C and held there for 30 min, before it was cooled to Tmin = 15°C, at which the temperature was kept for another 30 min. Heating and cooling were carried out three times. Afterward, Tmax was increased from 55°C to 70°C with an increment of 2.5°C, and for each increment, the temperature was cycled between Tmin and Tmax for three times. Heating and cooling rates of 5°C·min−1 were used for the whole experiment. In case of the bevel gear, the ‘teeth’ were also made from PEU. Twelve teeth in their original bent shape were placed in a programming template, heated to 75°C in a UF110 heating chamber from Memmert GmbH + Co. KG (Schwabach, Germany) and deformed at the same time in order to gain the teeth in a straight state, compare Figure 4d (right). Once cooled to 15°C and unloaded, the teeth were mounted on a gear base along with a spring-loaded disc cut out of a 5 mm thick poly(methyl methacrylate) sheet with a clearance of about 7 mm, so that they were in a stress-free state at 23°C. Later, the input and the output ‘bevel gear’ were assembled in a gearbox. For functional characterisation, the setup was placed in the environmental chamber of an MTS Criterion universal testing machine (model 43) from MTS Systems Corporation (Eden Prairie, MN, USA) equipped with a liquid nitrogen Dewar vessel. The actuation was then characterised by temperature changes between 58°C (Tmax ) and 23°C (Tmin ) in three cycles. In case of the unit cell, the thermomechanical treatment was conducted with an MTS Criterion universal testing machine (model 43) from MTS Systems Corporation (Eden Prairie, MN, USA). The device was equipped with a 500 N load cell and was operated with a temperature chamber, which was controlled by a Eurotherm temperature controller unit. Two heating elements were located at the back of the chamber. Liquid nitrogen from a Dewar’s vessel was fed into the chamber under a pressure of 1.3 bar as an essential prerequisite for cooling. At the beginning of thermomechanical treatment, the thermochamber was preheated to 75°C, and the unit cell was fixed in the pneumatic clamps of the universal testing machine using a clamping air pressure of 0.4 bar. After 30 min at 75°C, the unit cell was compressed in such a way that the top part touched the bottom using a loading rate of 1 N·min−1. In the next step, the temperature was brought to 15°C and held there for 30 min to fix the new shape while maintaining the compressive load. Then, the unit cell was unloaded with a rate of 1 N·min−1. The temperature was then heated to 23°C, and the unit cell was removed from the clamps.
The 2W-SME of the programmable material was subsequently characterised by unclamping only from the upper clamp and cycling the temperature between 58°C (Tmax ) and 23°C (Tmin ).
The thermoreversible changes in height Δh and length Δl of the studied samples were quantified according to equations (1) and (2):


Herein, hTmin (N) and hTmax (N) are the heights of a programmable material in the Nth cycle of actuation at Tmin and Tmax . Accordingly, lTmin (N) and lTmax (N) are the lengths of the programmable material in the Nth cycle of actuation at Tmin and Tmax .
Thermal expansion coefficient
The thermal expansion coefficient α of the PEU was determined with a Q800 DMA from TA Instruments (New Castle, DE, USA). The untreated sample in the form of a tensile bar of type 5B according to ISO 527-2:1996 was fixed in a film clamp. The temperature was raised from 23°C to 75°C and the expansion behaviour followed. Later, the sample was cooled to 23°C and heated to 58°C, before the temperature was cycled between 58°C and 23°C for four times. At 23°C, 58°C, and 75°C, the temperatures were held for 15 min, and a heating and cooling rate of 5°C mm−1 was chosen throughout the experiment. The length of the sample at the end of holding time at 23°C and 58°C was used to determine the thermal expansion coefficient of the PEU according to equation (3)), and the mean value was determined for cycles one to five.

Here, Δl defines the change in the length of the sample, l0
is its initial length, and
$\varDelta$
T the temperature difference between 58°C and 23°C, which is here of 35°C.
Simulation
The simulation of the programmable material with regard to the unit cell was conducted using Solidworks from Dassault Systèmes (Vélizy-Villacoublay, Île-de-France, France). After CAD modelling, the simulation was carried out in a nonlinear-static study, where the bottom part of the sample (orange arrows in Figure 6e,f) was fixed while a pressure of 10 N·mm−2 was applied on its top part (green arrows in Figure 6e,f). After simulation, the von Mises stresses were analysed.
Supplementary material
The supplementary material for this article can be found at http://doi.org/10.1017/pma.2023.9. Supplementary videos: S1.movie: Thermally switchable ‘bevel gearbox’ (Figure 5) and S2.movie: Actuating unit cell (Figure 7).
Acknowledgements
The working group of Fraunhofer IAP wishes to thank the European Regional Development Fund for financing a large part of the laboratory equipment (project 85007031) and the Fraunhofer High-Performance Center ‘Integration of Biological and Physical–Chemical Material Functions’ in Potsdam-Golm for the funding of some of the FFF printers (project 630505). Dr. Mario Walter and Dennis Schönfeld are acknowledged for carrying out polymer synthesis.
Funding statement
This work was carried out in two projects within the Fraunhofer Cluster of Excellence ‘Programmable Materials’ (PSP elements 40-04068-2500-00007 and 40-01922-2500-00003).
Competing interest
The authors declare no competing interests exist.