Introduction
Investigation of snowpack physical properties has long been of interest to researchers, both for assessing avalanche potential, and for estimating the load-bearing capacity of snow pavements. Abele and Gow (1975) outline three methods of strength assessment, namely surface load tests, sample testing and probing, but only probing provides an in situ means of assessment that is time- and cost-effective.
The Swiss rammsonde, a portable impact penetrometer, has been used since the 1930s to assess snow stratigraphy and the relative resistance of snow layers. However, because of the rate dependency of snow, it is of limited use in establishing empirical or physical relationships; it is also limited in depth. Schaap and Föhn (1987) describe a manually pushed, modified 11.3 mm electric cone penetrometer for investigating alpine snow, but the manual insertion method and restricted capacity limit the usefulness of such a device in hard polar snow. Numerous other instruments have been developed for assessing snow strength and stratigraphy (Reference BradleyBradley, 1968; Reference Dowd and BrownDowd and Brown, 1986; Reference Johnson and SchneebeliSchneebeli and Johnson, 1998; Reference Mackenzie, Payten and StevensMackenzie and Payten, 2002); however, they are all limited in depth and capacity, and are not suitable for assessing dense polar snowpacks, where strength in uniaxial compression may approach 3 MPa (Reference MellorMellor, 1975).
Many factors, including penetrometer size and shape, penetration speed and material behaviour ahead of the penetrometer, affect cone penetration testing (CPT) in soil (Reference Lunne, Powell and RobertsonLunne and others, 1997), and many of these factors remain pertinent when attempting to analyse CPT in polar snow. Ice is a rate-dependent material (Reference Schulson and DuvalSchulson and Duval, 2009), so it is probable that during CPT in snow both cone resistance and sleeve friction will vary with rate; penetrative testing (e.g. Reference FukueFukue, 1977) supports this. Penetrometer size affects measured stress in soils (Reference Whiteley and DexterWhiteley and Dexter, 1981), and Johnson and Schneebeli (1999) modelled size effects in granular materials, so it is probable that both cone size and shape will affect measured stress in snow.
Observation and laboratory testing by Floyer and Jamieson (2006) and LeBaron and others (2012) show that a plug, or compacted zone of broken material, may form ahead of a cone penetrating snow, a process also identified in the indentation of brittle porous rock (Reference Leite and FerlandLeite and Ferland, 2001). This process requires investigation because such a compacted zone may act, inertly, to transfer the load and affect the depth accuracy of stress measurements. Also, in some soils the cone may ‘sense’ an approaching layer some 10–20 cone diameters before it reaches the layer (Reference Lunne, Powell and RobertsonLunne and others, 1997), supposedly via elastic deformation of the material ahead of the cone, resulting in force transferral, but not fracture of these layers or particles. An understanding of this process is necessary to assess the depth/stress relationship during CPT.
Triaxial testing of low-density snow shows no effect of confining pressure (Reference Scapozza and BarteltScapozza and Bartelt, 2003); however, many other geomaterials (including ice) do display a dependency on confinement (Reference Renshaw and SchulsonRenshaw and Schulson, 2001), so the effect that overburden may have on cone resistance in mid- to high-density snow warrants investigation; also, does sufficient frictional heating occur during penetration to cause pressure melting, and what effect might this have on test results? how does this friction (never before measured in snow) vary with density, tip resistance, etc.? and what might be extracted from the data?
Cone penetration testing in polar snow, measuring both tip resistance and sleeve friction, has not previously been performed, and there are many questions that need addressing to enable accurate estimation of parameters, such as snow strength, from CPT. This paper introduces the development of robust cone penetration test equipment, suitable for conducting penetrative testing in hard polar snow, and describes some factors that must be considered when interpreting data from such testing. This is the first description of CPT in polar snow, and, thus far, insufficient analysis has occurred to support the scientific value of such testing. However, CPT assessment of polar snow for infrastructural site investigation purposes.
Instrument Description
Typically, CPT equipment is mounted on a heavy truck or trailer-rig, primarily to ensure that sufficient reaction force can be provided when driving into hard soils. However, any equipment modified for use in Antarctica needs to be relatively lightweight, transportable and modular in nature. To address these needs, a CPT ‘box’ was manufactured with assistance from Lankelma and Gardline Geosciences (UK).
The ‘box’ provides a container in which CPT and ancillary equipment can be stored and transported, and in which a CPT operator can stand. A three-point hitch mounting plate of 25 mm thick steel provided a rigid frame upon which hydraulic rams were mounted. This plate (and thus the subsequent ‘box’ built upon it) attaches to the category-three three-point hitch of a standard agricultural tractor, such as those used by the British Antarctic Survey (BAS). A frame of box tubing was welded to the main structural steel plate, onto which 1.5 mm gauge sheeting was welded. The box (designated UK11 by Lankelma) measuring 1.7 m high × 1.45 m long × 1.35 m wide and weighing ~ 1300 kg when loaded, is shown in Figure 1.

Fig. 1. UK11 configured and fitted for CPT. Insets show rigid-link installed and data-collection equipment.
Inside the box is a rack to store 20 rods of 1 m length and a small workbench for data-gathering equipment and a laptop computer; a mounted vice assists in rod attachment and removal. The box is secured by two steel-plate top doors, and a rear door, all of which can be secured closed and padlocked, or latched open while the box is in use. The hardness of the material through which a driven cone can penetrate depends on the reaction force available from the pushing equipment. UK11 weighs only 1300 kg, and because a standard tractor three-point linkage only provides resistance to a downward, not an upward, force, an additional rigid-link was required to provide increased resistance between the base of UK11 and the top hitch of the tractor. During use the rigid-link can be left attached to the tractor, and then unscrewed and ‘trailed’ between subsequent testing sites. The maximum resistance offered by UK11 with the rigid-link in place is ~ 40 MPa, equivalent to a 4 t reaction force. The rigid-link is shown in place in Figure 1.
A pair of hydraulic rams with a stroke of 500 mm and bore diameter of 70 mm, capable of a maximum pressure of 21 MPa, were mounted within UK11 (inset Fig. 1). The rams were controlled via a two-way non-friction-controlled lever; hydraulic fluid was provided to the circuit through two external couplings to the tractor’s hydraulic circuits. The maximum permissible flow rate was 20 L min−1. No visual indication of flow rate was used, but ram penetration rate was indicated on the laptop computer display. Prior to conducting a test the hydraulic flow rate was altered until the desired ram rate was achieved. This rate remained constant throughout a test, except for small amounts of retardation that were observed but not recorded upon penetrating hard ice layers. Driving force is transferred from the rams to the rods by means of a ball-bearing-type clamp that slots into a frame attached to the top of the rams. The clamp can be manipulated to allow rods to be driven downwards but not upwards, or upwards but not downwards (for rod and cone extraction). Maximum capacity of the clamp is 20 t in either direction. Standard 36 mm diameter steel alloy rods, each of length 1 m (provided by A.P. van den Berg), were used to transfer the penetrative force from the hydraulically driven rams to the cone at depth.
Four specially produced 35.6 mm scientific cones from GeoPoint Systems BV were provided by Gardline Geo-sciences. The cones measure resistance on the cone tip and friction on the cone sleeve. They also have the capacity to measure pore pressure. Although this may be useful for assessing free water within alpine snow, in the dry Antarctic firn tested no pore pressure readings were obtained. The cone with friction sleeve is shown in Figure 2 and cone specifications are listed in Table 1.
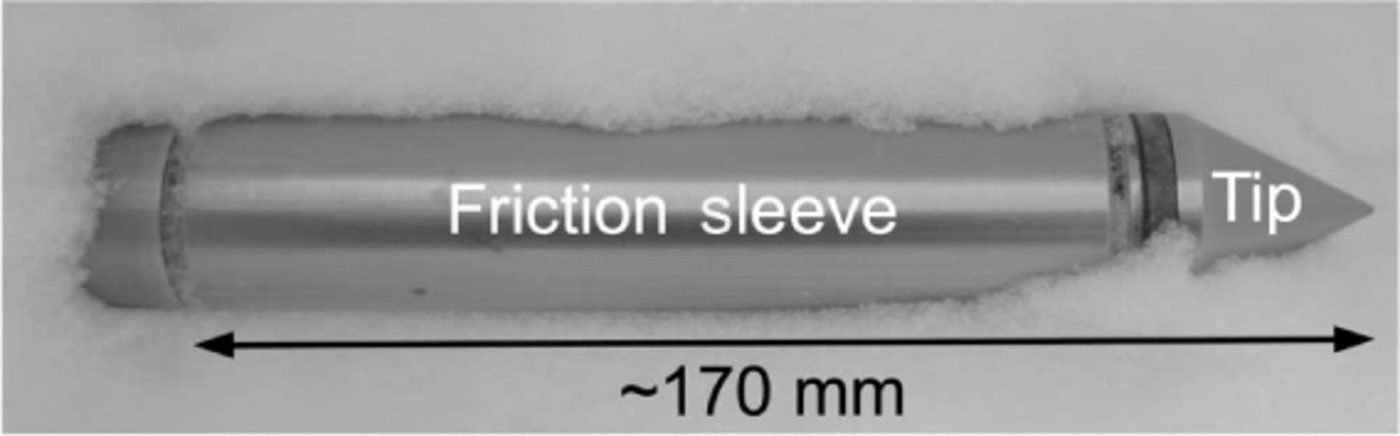
Fig. 2. Cone incorporating 35.6 mm diameter tip and 135 mm long cylindrical friction sleeve.
Table 1. GeoPoint ‘Antarctic’ cone specifications

Two cones were used during testing, as well as two manufactured flat alloy plates, of diameters 36 and 120 mm, that were occasionally used in place of conical tips for comparative testing.
Both the cone tip and friction sleeve measure the axial resistive force (N) at a rate of 5 Hz; this is then converted to a stress measurement (MPa) within the cone, based on the assumed constant dimensions of the cone tip and the friction sleeve.
A Sick Stegmann wire-draw mechanism and incremental rotary depth encoder attached to the hydraulic rams triggered the recording of cone depth every 5 mm of penetration. Data were recorded using an A.P. van den Berg ‘Golog’ data recorder, modified to allow recording at this interval. The Golog box was powered via cable connected to the tractor’s 12 V system, and connected to a laptop via a RS232/USB connection. Additional input cabling was from the cone and the depth encoder. A standard Panasonic C32 Toughbook laptop computer running A.P. van den Berg’s GOnsite (Van den Reference Van den BergBerg, 2002) Windows-based software was used to manage CPT data acquisition and initial data manipulation.
Calibration
Lunne and others (1997) comprehensively outline the checks and calibrations that should be carried out before performing CPT. The verticality of the CPT box and thrust apparatus was visually verified before the start of each test. This often involved repeated lowering of UK11 to the snow surface in an attempt to achieve a vertical drive axis. However, for more accuracy, a multidirectional spirit level, or similar, should have been used in this assessment. Excessive misalignment was noted if evident. Push rods were inspected for straightness and typically a selected five (out of the twenty rods available) were utilized for the testing. Cone-zero readings were taken at the start and end of each test, and the precision of the measurements obtained was verified through initial spatially confined tests. The cones were new, so cone dimensions were not retarded or deformed in any way, and only limited additional wear was expected during testing in snow and ice; cone end area was similarly unchanged throughout the testing. Seals and pore-water mesh were new, and were replaced as necessary between tests if any excess wear or deterioration was noted. Cones were provided with calibration data, and no additional recalibration was performed in the field. If a cone showed excessive zero-shift, then an alternative (new) cone was used. The cones were calibrated in the cold rooms of the Scott Polar Research Institute (SPRI, Cambridge, UK) prior to deployment, to verify the zero-shift and linearity of the cones over the expected operational temperature range of +5 to –20°C.
As a result of this testing, all CPT equipment, aside from the Golog box, was equilibrated to ambient temperatures before initial zero values were taken.
Field Testing
Almost 100 cone penetration tests, typically to 5 m depth, were conducted at various locations within the vicinity of the Halley V Station, Antarctica, over the period 21 January– 22 February 2010. The mean temperature at Halley is ~–308C, although summer temperatures sometimes exceed 0°C; annual snow accumulation is ~ 1.2 m. Tests were conducted at various rates between 0.16 and 55 mm s-1; the actual rate sometimes varied by ± 1 mm s−1 as hardness varied, with the cone retarding or accelerating upon entering or leaving a harder layer. The mechanical process of conducting each CPT is fairly standard and a set of standard operating procedures (SOPs) outlining this process was produced (these SOPs are not presented here). At a standard sampling rate of 20 mm s−1, a test to 5 m depth takes ~ 5 min and numerous tests could be conducted in quick succession, tractor movement taking the greatest amount of time. Tests were conducted as weather and operational commitments allowed, and were designed to investigate numerous factors affecting CPT interpretation, including local snow stratigraphy, variation with snow density, effect of penetration rate, effect of confining pressure on tip resistance and sleeve friction, existence of a compacted zone ahead of the cone, effect of compaction and ‘sensing’ ahead of the cone.
Results
Selected results are shown to illustrate particular facets of the investigation. Variations of both tip resistance and sleeve friction with snow density are shown in Figure 3. Layers were identified visually, then density was measured gravimetrically in a pit excavated adjacent to the CPT site (snow pit 1).

Fig. 3. Mean tip resistance (averaged over the 30.83 mm length of the cone) vs mean, normalized and lag-adjusted (25 mm) sleeve friction (averaged over the 135 mm length of the friction sleeve) superimposed over gravimetric snow density (snow pit 1). Both mean tip resistance and mean friction vary with density.
Effect of penetration rate
Figure 4 shows mean tip resistance (averaged over the entire test depth) for each test vs penetration rate; the solid line is a power-law fit with R 2 = 0: 97. Variation in mean sleeve friction (averaged over test depth) with penetration rate is shown in Figure 5; a possibly erroneous outlying data point at a rate of 2 mm s−1 has been removed. A power-law curve (R 2 = 0: 94) fits the data well (line of best fit extends to zero, graph is truncated for display). Each data point is the average resistance across the entire test depth (~2 m; n ≈ 390). Figure 5 almost mirrors Figure 4.

Fig. 4. Variation of mean cone tip resistance (averaged over entire test depth) with penetration rate; mean values are significantly different (p < 0.01).

Fig. 5. Variation of mean sleeve friction (averaged over entire test depth) with penetration rate (possibly erroneous point removed); mean values are significantly different (p < 0.01).
Effect of penetrometer size
Three tests were conducted to investigate whether altering penetrometer size would result in a change in measured tip resistance. Only one size of cone was available, so these tests compare resistance from different sizes of flat plates (Fig. 6); a cone test is also shown for comparison. To generate comparable resistance values, large-plate data have been normalized by 11, the area of the large plate divided by the area of the small plate. Mean resistance over the entire depth range is plotted as a straight line. From the graph it may appear that large-plate data are not recorded until a depth of 0.14 m; however, inspection of the raw data suggests that fluctuating resistance of ~ 5 to 10 kPa was measured at this time; whether this is a true representation of resistance at this shallow depth is not known.

Fig. 6. Variation in normalized tip resistance between cone and different sizes of plates, showing that normalized resistance decreases as penetrometer size increases. To generate comparable resistance values, large-plate data have been normalized by ~ 11, the area of the large plate divided by the area of the small plate; mean resistance over the entire depth range is plotted as a straight line.
Effect of cone shape
Kinosita (1964) and Johnson and Schneebeli (1999) have shown that variations in cone shape affect measured resistance values, both in snow and soils. In order to verify this phenomenon, some tests were conducted with a flat plate of identical diameter to the standard 608 cone; no other cone shapes were used. This testing revealed that a flat plate realizes significantly greater resistance than a 608 cone of the same diameter (Fig. 6).
Effect of confining pressure
To investigate the effect of overburden pressure on tip resistance and sleeve friction, three pairs of tests were conducted in close proximity, with an amount of surface surcharge removed between each pair of tests.
The six tests were conducted at a penetration rate of 25 mm s−1 to the same absolute depth of 3.0 m (relative to the initial undisturbed surface), but overburden was removed by bulldozer after the first and second pair of tests. Comparison was then made between tip resistance and sleeve friction data for the lowest 1 m of each test. Note that experimental technique may have affected these test results, because although no obvious deep fracture or compaction was observed, a bulldozer was used to remove the substantial volume of overburden, with typically two to three passes required each time. This trafficking will have had some impact in compacting and deforming the snow-pack prior to later, supposedly less confined, tests.
Variations in tip resistance for the three pairs of tests are shown in Figure 7, with a line of best fit of gradient –0.11 ± 0.078; each point on the graph is the mean of 195 data points averaged over the test depth.

Fig. 7. Inconclusive variation of tip resistance with amount of overburden removed. Each plotted point represents the average over 195 data points. Vertical bars indicate the standard error.
Variations in sleeve friction for the three pairs of tests are shown in Figure 8, with a line of best fit of gradient –0.003 ± 0. 0004; each point on the graph is the mean of 195 data points averaged over the test depth.

Fig. 8. Significant variation of mean sleeve friction with amount of overburden removed. Each plotted point represents the average over 195 data points. Vertical bars indicate the standard error.
Formation of a compacted zone ahead of the cone
Some qualitative assessment was attempted to evaluate whether a compacted zone of fractured snow formed ahead of the advancing cone or plate. No quantitative assessment was made; however, both still and video footage of an advancing cone and plate, plus examination of CPT holes post-test were used to assess this phenomenon.
To attempt to observe the physical processes as the cone penetrated the snowpack, a test was conducted at a rate of ~ 1 mm s−1. An incision was made in the snowpack parallel to the cone to enable observation of the cone tip. This enabled the advancing cone to be filmed. Similar work to this has recently been performed in the laboratory (Reference LeBaron, Miller and Van HerwijnenLeBaron and others, 2012).
Although forming such an incision compromised the behaviour of the snow, some observation of what was happening at a granular level was possible. Snow grains appeared to be displaced in a direction largely perpendicular to the advancing cone face before being forced into the sides of the borehole at the cone shoulder. Such behaviour is consistent with work in agricultural soils by Whiteley and Dexter (1981) and the statistical micromechanical model proposed by Johnson (2003). The outcome of this process can be observed in Figure 9, which shows an annulus of compacted material around the perimeter of the bored hole post-test, presumed to be formed by the compaction of snow into the wall at the cone shoulder.

Fig. 9. Compacted perimeter (~2 mm thick, tape for scale) observed in cross section of hole post-test, after fractured material ahead of the cone is compacted to the side forming an annulus.
Pressure melting
Both Federolf and others (2004) and Szabo and Schneebeli (2007) note the rapid, almost immediate, sintering of snow grains immediately after brittle fracture. Some level of pressure melting and re-sintering of fractured bonds was expected as the cone was driven into the snow, possibly sufficient to ‘freeze-in’ the cone and rods. However, no level of static friction was evident upon retrieval, nor was any free water observed, perhaps suggesting that temperature and snow-moisture conditions were sufficiently cold and dry to limit identifiable pressure melting.
Discussion
Variation with density
Figure 3 shows good qualitative correlation between tip resistance and density. The resistance trace varies within each layer, owing to the distance required to achieve steady-state resistance, but variations in resistance agree well with density variations. Particularly hard and soft layers are evident, coinciding well with very dense and less dense layers, and both resistance and density are observed to generally increase with depth.
The increase of tip resistance with density is consistent with the positive correlation between ram hardness (obtained via the rammsonde) and density (Reference GublerGubler, 1975) and is expected. Some resistance variation in snow of the same density is expected because density does not necessarily imply the level of bonding within the snow, whereas measurements made by CPT (or other hardness measurements) will vary with such changes. Although a positive correlation between tip resistance and density is expected, quantifying this relationship from data such as those presented in Figure 3 is difficult, because resistance does not vary in discrete layers (unlike density). Snow microstructural changes and cone size/shape affect the resistance data, but comparison of density and layer-averaged resistance reveals a significant positive correlation of >0.6. If the gradients of the density and resistance increase with depth are compared (0.0182 vs 0.1485), resistance is seen to vary by almost an order of magnitude more than density. This is consistent with the understanding that snow not only increases in density with depth, but that increased sintering and strengthening of bonds within the snow also occurs, without necessarily a change in density; extraction of microstructural information by comparing sleeve friction and tip resistance data may be possible. The relationship between friction sleeve data and density is perhaps more complex.
Figure 3 shows that sleeve friction appears to trend with density. The friction trace lags density by perhaps 4–5 cm, especially in the upper 2.5 m, but this lag is not unexpected, and between 2.5 and 4.5 m sleeve friction is seen to qualitatively trend with density. Both friction and density increase with depth, albeit friction (similar to tip resistance) increases at a greater rate. Lag is evident, consistent with the physical dimensions of the friction sleeve (length 135 mm), and the correlation between density and sleeve friction is ~ 0.6 (Pearson correlation significant at the 0.01 level; two-tailed).
Colbeck (1994) noted the decrease in kinetic friction with increasing density, and both Mellor (1964) and Ericksson (1955) note a decrease in friction with grain size. Grain size generally increases with depth during densification (although the increase to a depth of 5 m may only be ~ 0.1 mm; Reference Rick and AlbertRick and Albert, 2004), hence some decrease in friction with increased density is implied. This is contrary to observations made using CPT.
The observed increase in sleeve friction with density is assumed to be due to an increased normal force acting upon the friction sleeve, caused by less efficient packing of fractured particles at the cone shoulder as the density of the snow undergoing penetration increases. Such a process would cause greater sleeve friction to be measured in higher-density snow. Testing in pre-drilled holes resulted in friction values five to six times lower than standard friction values (p < 0. 0001 for unpaired t test), suggesting the influence that normal force may have on sleeve friction values. Examination of flat-plate data presented by Abele (1970) also shows that as density increases, penetration resistance increases and penetration distance decreases for the same applied pressure. These observations support the supposition that an increase in density will result in increased friction, not because of grain-size variations but because of the increase in normal force acting on the sleeve.
Effect of grain size
It is hard to isolate the effect of grain size on cone penetration results, as invariably grain size was observed to vary with density and thus probably with hardness; limited work has been reported on the effect of grain size on penetrometer testing. Floyer and Jamieson (2006) suggest that grain size affects the formation of the compacted zone ahead of a penetrometer in snow. However, because no compacted zone was observed to form ahead of the cone in Antarctic CPT (see annulus formed at side, Fig. 9), grain-size differences do not appear relevant. However, Schweizer (1999) reported that increased grain size tends to shift the brittle/ductile transition towards lower strain rates. Thus, at the same penetration rate, decreased resistance values may be expected in the brittle zone if larger grain sizes are encountered. Also, as grain size generally increases with depth, some level of decreased tip resistance may be expected. Thus, changes in grain size may have some limited effect on measured tip resistance.
Limited literature is available to guide discussion on sleeve friction measurements in snow, because no such testing is known to have previously occurred. However, from a planar friction perspective, Bowden (1953) considering grain size in snow as a measure of surface roughness suggests that smaller grain size may enable greater packing, resulting in an appreciable increase in effective firm/sleeve contact area. This would mean that sleeve friction measurements may be greater in snow of smaller grain size, all other parameters being equal. This is consistent with the work of Ericksson (1955), who also showed that friction increases with smaller grain size. Thus sleeve friction may also be expected to decrease by some amount with depth as average grain size increases.
Ideally, some measure of these variations could be extracted from the CPT results. However, because of the complicated stratigraphy and other material changes evident within each test, isolation of this phenomenon is not readily achievable. Higher-density snow often has a larger grain size and thus the effect on resistance because of density may tend to override (in the opposite sense) any variation owing to grain size. Controlled laboratory tests in homogeneous blocks of snow, where both grain size and density (as well as microstructure) can be manipulated, would appear necessary to accurately resolve this relation with regard to penetrative testing in snow. Grain size may affect the effective area of the cone.
Effect of penetration rate
Applying the one-way ANOVA (analysis of variance) test to the variable-rate CPT data in Figure 4 shows that the mean resistance values are not statistically equal (F statistic = ~ 150, p < 0.001) and the Tukey–Kramer honestly significant difference (HSD) test confirms that all mean resistance values are significantly different from one another (p < 0. 01). Figure 5 suggests that a rate effect is also apparent when measuring snow friction via a sleeved penetrometer. Application of the one-way ANOVA test to the variable-rate friction data used to generate Figure 5 shows that the mean resistance values are not statistically equal (F statistic = ~ 27, p < 0. 0001), and the HSD test confirms that all mean resistance values are significantly different from one another (p < 0.01). This suggests an inverse relationship between tip resistance and sleeve friction at varying penetration rates, although the variation differs by numerous orders of magnitude.
Johnson and Schneebeli (1998, 1999), Schneebeli and Johnson (1998) and Schneebeli and others (1999) have performed extensive investigations into penetration in snow, but do not comment on the effect of penetration rate on tip resistance measured by the snow micro-penetrometer, only stating that ‘constant-velocity penetration (1–40 mm s−1) avoids the rate-dependence associated with creep deformation’.
Kinosita (1967), in his compression tests on snow, found that once in the brittle zone, stress decreased as speed of compression increased, initially rapidly and then more gradually, almost asymptotically. Gubler (1975) showed that hardness decreased substantially as penetration rate increased (within the brittle zone) during rammsonde tests, and Fukue (1977), in tests on a penetrative blade into snow, identified the ductile/brittle transition zone and also noted a decrease in strength at an increased rate of deformation. These findings are not unexpected and are consistent with the brittle behaviour of snow’s primary constituent, ice. Variations may be expected, owing to the compaction and densification of snow, but if any level of bonded micro-structure is present within the snow then it is ice bonds that are failing, hence behaviour consistent with ice is expected.
Andersland and Ladanyi (1994) state that frozen soils are much more rate-sensitive than non-frozen soils, and Ladanyi and others (1991) (cited by Reference Lunne, Powell and RobertsonLunne and others, 1997; commenting on rate-controlled cone penetration tests in permafrost and ice) suggest that a power-law relationship can be used to express the relationship between penetration resistance, q c, and penetration rate, ν:

where n is the creep exponent and q o and ν o are the coordinates of any selected point on the straight-line plot of q o and ν o on a log–log scale. This equation is derived from tests in the ductile zone, but, because rate effects in the brittle zone also appear to follow a power-law relationship (allowing a linear gradient to be established on a log–log plot of rate vs resistance), it can also be applied to the brittle testing described herein (although n is no longer a ‘creep’ exponent). This allows estimation of CPT resistance values at various rates within the brittle regime. Buteau and others (2005), in more recent CPT in permafrost, also found a rate dependency (within the ductile range), hence dependence of stress upon rate appears well documented in snow, ice and other frozen geomaterials.
Contrary to these findings, Floyer (2008), investigating penetration of a 12 mm rounded, manually driven penetrometer, ‘found no substantial dependence of the force-response on velocity over the velocity range tested’ (velocities up to 120 cm s−1), a finding supported by additional work (Reference Floyer and JamiesonFloyer and Jamieson, 2010), where again for a round-tipped 12 mm diameter penetrometer in uniform snow, no substantial dependence of the force response on velocity over the velocity range tested was found. Discussions with J. Floyer (27 May 2009) on this matter concluded that rate effects may play a part in some types of snow and with different penetrometer configurations. Additional reasons why Floyer and Jamieson (2010) may have found these results are:
all their tests were at much higher penetration rates (velocities up to 120 cm s−1 vs my maximum penetration rate of ~ 6 cm s−1) where the variation in stress with strain rate may be observed to be diminished (see Fig. 4)
actual strain rates may be much higher and therefore also at the far end of the stress/penetration-rate curve (Fig. 4), especially noting the rounded penetrometer, which may be expected to cause greater snow disturbance than a ‘sharp’ penetrometer in dry snow.
If measured resistance in snow is rate-dependent, as I have shown here, and the rate curve diminishes with strain rate once in the brittle zone (Fig. 4 and work by Reference Renshaw and SchulsonSchulson, 2001, among others) then it may be that the penetration/strain rates examined by Floyer and Jamieson (2010) are sufficiently high that change in measured resistance may appear insubstantial. This is consistent with the observation by Kinosita (1967) that at very high rates within the brittle zone the curve asymptotically approached a constant stress. Conversely, my tests (where rate dependence is evident) were conducted at penetration rates (and possibly strain rates) only just within the brittle regime, where greater deterioration in measured resistance with increased strain rate may be expected. Thus I judge the observed variation of CPT tip resistance with rate to be real.
Figure 5 suggests that sleeve friction may increase (possibly to a limit) with penetration rate. Bowden (1953) observed a marked decrease in friction under sled runners as speed increased (up to 5 m s−1), although a reduced decrease was observed at the speed range of my CPT (~1–50 mm s−1). The mechanism at play was assumed to be lubrication by a water film generated via frictional heating. Mellor (1964) states that, in general, friction decreases as sliding rate increases, again typically because of frictional melting and lubrication. No pressure melting or refreezing was evident throughout the CPT, raising the question whether snow dryness and slow penetrative speeds may have contributed to minimal or negligible free water being generated to reduce sleeve friction.
Klein (1947) (cited by Reference ColbeckColbeck, 1988) suggests that there are three components to snow friction: solid-to-solid friction, lubricated friction and capillary suction friction, all of which depend on the prevailing snow crystal type, as well as the temperature and liquid-water content of the snow. Solid-to-solid interaction resulting in high friction will occur when the thickness of any generated water film is insufficient to prevent particle contact. If the nature of the snow tested at Halley was dry enough and cold enough to prevent any free water forming at tested penetration speeds, then only solid-to-solid interaction may have occurred.
Bowden (1953) suggests that (for plastic skis) at a temperature of –10°C, an increase in friction with rate occurs at speeds below ~ 100 mm s–1. All CPT was conducted below this speed, hence this is the realm of interest. Colbeck (1988), examining Bowden’s work, suggests that at sub-freezing temperatures (0 to –108C, my test temperatures), at rates below Bowden’s transition rate, a minimum in friction coefficient is observed, such that there is a zone where friction will rise as speed increases. This may explain the shape of the curve generated by my variable-rate friction sleeve measurements (Fig. 5). This behaviour is further supported by Shimbo (1971), who also found that the coefficient of (kinetic) friction increased towards the static value at speeds <0.1 m s−1.
The discussion thus far has concentrated on penetration rate per se, and has neglected any possible influence that rate may have on normal stress, a major determinant of friction. In all tests conducted, fractured particles are considered to have been forced into the hole wall at the cone shoulder, thus contributing to the ensuing friction measurement. The question is whether there is any difference in the residual hole wall density after completion of a test at different rates. Potentially, a slower test allows greater sintering and compaction of the side-walls to occur, whereas in a faster test perhaps less densification and compaction is possible, resulting in less compaction around the sleeve, increased normal force and greater friction.
Further work is required to assess the factors contributing towards the observed increase in sleeve friction with penetration rate. This increase, although contrary to general behaviour surmised from the literature, appears to be consistent with data obtained from tests at similar temperatures and rates. Limited frictional melting and variable normal forces on the penetrometer friction sleeve may each play their part in the observed variation of sleeve friction with penetration rate.
Effect of penetrometer size
A size effect is evident from Figure 6: penetrometer resistance decreases as penetrometer size increases. The difference between all tests is statistically significant (p << 0.0001 for two-tailed unpaired t test). The normalized average percentage decrease in resistance is 16% for a real plate area increase of ~ 1100%.
This decrease is qualitatively consistent with work by Johnson (2003), using smaller penetrometers, that showed decreased resistance as penetrometer base area increased (although Johnson showed a greater effect), and is also quantitatively similar to work by Whiteley and Dexter (1981) who, for a similar size increase in area, suggest a resistance decrease of ~ 10%; however, their work was on smaller cone penetrometers with a 30° tip angle, and not on flat plates.
Marshall (2005) notes that the size effect is greatest when penetrometer size is <40 times grain size (average observed in my snow pits was 0.7 mm) and this may explain why the differences observed were not as great as those suggested by Johnson (2003); flat plates used in testing were of diameters ~ 36 and ~ 120 mm.
Cone size can also affect the rate at which local material is strained at the head of the cone, causing variations in resistance at constant rates of penetration. Ladanyi (1982), exploring the link between probe size, strain rate and tip resistance in frozen geomaterials, derived Eqn (2) to relate representative strain rate, , failure strain in uniaxial compression,
f, penetration rate, ṗ, and penetrometer diameter, d,

and then used Eqn (3) to relate strain rates to tip resistance:

where q
c1 is tip resistance for penetrometer one, q
c2 is tip resistance for penetrometer two, is strain rate for penetrometer one,
is strain rate for penetrometer two and n is the creep exponent obtained from the slope of q
c vs strain rate in a log–log plot. (n ≈ 3 for ice at low strain rates, but may be ~ 10–20 at higher strain rates.)
Applying these equations to the flat-plate data (diameters ~ 36 and ~ 120 mm) reveals that for n = 10.3 (derived from strength of ice vs strain rate; Reference PetrovichPetrovich, 2003), a reduction in resistance owing to plate size of 14% is predicted. This agrees very well with the observed average decrease of 16%. A size effect is evident in assessing strength of snow with a penetrometer, and further techniques must be explored to enable consistent comparison between datasets from penetrometers of different size.
Effect of cone shape
Resistances are substantially greater in the flat-plate test (statistically significant with p < 0.0001 via unpaired t test); the difference in average resistance (to 5 m depth) is ~ 188%, although the difference at discrete depths sometimes rises to >200%. This is quantitatively consistent with modelled data presented by Johnson (2003), who suggested an increase in resistance of two to three times as cone angle increases from 608 towards 908. It is also consistent with the qualitative supposition (Reference JohnsonJohnson, 2003) that as the tip angle approaches that of a flat plate (a 1808 cone), the increased dimension normal to penetration and the formation of a compacted zone moving ahead of the penetrometer increase the number of snow microstructural elements mobilized and markedly increase resistance to penetration. Gill (1968), in work in soil, found similarly that the measured resistance increased as cone angle increased, primarily as a function of the cone angle. Nowatzki and Karafiath (1972), also working with soils, found that at higher relative densities, where less packing is observed, change in cone angle had a greater effect on cone resistance.
Application of Kinosita’s (1967) equation relating cone angle to penetration resistance in the brittle zone,

where F is force in kgf, ϑ is the vertical angle of the cone (°), ρ is snow density (kg m–3) and Z is distance of the cone apex under the snow surface (cm), suggests that variation between the two shapes in snow of density 450 kg m-3 may be ~ 600%. This is far greater than observed. This discrepancy may exist because Kinosita’s work essentially involved shallow penetration, in which the cone did not penetrate beneath the surface, and substantial ejection of overburden upon cone entry was incorporated, and Kinosita’s maximum rates of penetration (0.55 mm s−1) were only just within the brittle zone (>~ 0.16 mm s−1, as defined by Reference Gaméda, Vigneault and RaghavanGaméda and others, 1996), where changes in rate result in greater stress variation.
Because compacted material will form on any flat plate, altering the shape towards conical, it is surmised that the difference in resistance between any flat plate and conical test will diminish with depth. Figure 10 shows the 100-point running mean for the ratio of tip resistance from a flat-plate test to tip resistance from a standard cone test vs depth.

Fig. 10. Ratio of flat-plate resistance to cone resistance generally decreases with depth, consistent with the formation of a conical mass of compacted snow on the flat plate as the test progresses.
Although the mean ratio still exhibits large variability owing to stratigraphy, the linear trend line suggests a decrease in this ratio with depth. This suggests that the flat plate may become more ‘cone-like’ as a test progresses. Further testing is necessary to verify this behaviour, yet it appears intuitively feasible. The shape of the cone has a marked effect on the physical interaction of the penetrometer with the medium, with resultant effects on measured resistance values, and must be considered when attempting to compare or interpret penetrative tests.
Effect of confining pressure
Variations in mean tip resistances at different overburden pressures are not consistently statistically different, so it is unwise to draw firm conclusions about the effect of overburden pressure on cone tip resistance.
The rationale for a possible increase in resistance as confining pressure is increased is that crack initiation (required for brittle failure) is restricted and greater resistances are achieved (Reference Renshaw and SchulsonRenshaw and Schulson, 2001). Within shallow snow the variation in confining stress is very small compared with tip resistances, hence an insignificant or unclear trend, as evident, is not unexpected. Also, and importantly, in porous (lower-density) snow this effect will be significantly reduced as, regardless of the confining pressure, sufficient pore space exists to ameliorate this effect, enabling unhindered fracture and compaction, regardless of the applied amount of confining pressure, whereas as porosity reduces (and density approaches that of ice) the effects of confinement may increase.
Hence, although confining pressure may have some impact upon the tip resistance proffered by polar snow, the variation is complicated by the density and nature of the material, and analysis of the data is inconclusive.
It is possible that an increase in overburden stress may have a greater impact on sleeve friction (within a post-fractured granular medium) than on tip resistance (where normal stress may have less effect, owing to a bonded matrix pre-fracture). Figure 8 shows sleeve friction decreasing as overburden pressure is reduced; a ~ 40% reduction is observed after the removal of 2 m of overburden. This suggests that overburden and resultant vertical stress may affect the normal stress on the friction sleeve and thus the measured friction (in snow of the same density and microstructure). This is consistent with the evolution of friction at depth under varying overburden pressure (Reference McClung and SchaererMcClung and Schaerer, 1993) and is consistent with expectations. However, Colbeck (1988) (commenting on an observation by Reference Perla, Glenne, Gray and MalePerla and Glenne, 1981) claims that for pressures typically exerted by skiers (1–5 kPa) there appears to be negligible variation in friction with increased load, a consequence of the true contact area being proportional to the load.
This may be the case on the surface of natural alpine snow; however, during penetration it is assumed that processed, rearranged, compacted and densified snow beside the friction sleeve is of a largely uniform nature, such that any increase in normal pressure will result in an increase in friction upon the sleeve. Also, pressure upon the friction sleeve is estimated to be an order of magnitude greater than the values considered by Colbeck (1988). Although my tests were probably affected to some extent by the testing method, some decrease in observed sleeve friction owing to decreased overburden pressure (and thus normal force upon the sleeve) is apparent.
Formation of a compacted zone ahead of the cone
Observations described herein suggest that no compacted zone formed ahead of the advancing cone, and Figure 9 suggests that fractured material was pushed normal to the cone and forced into the hole walls at the cone shoulder. The hardness of this annulus of compacted snow rose from ‘finger’ to ‘pencil’ post-CPT. Similar observations were made in an attempt to identify the formation of a compacted zone ahead of an advancing flat plate. Figure 11 shows a cone of compacted snow, routinely observed on the face of the flat plate upon completion of a test.
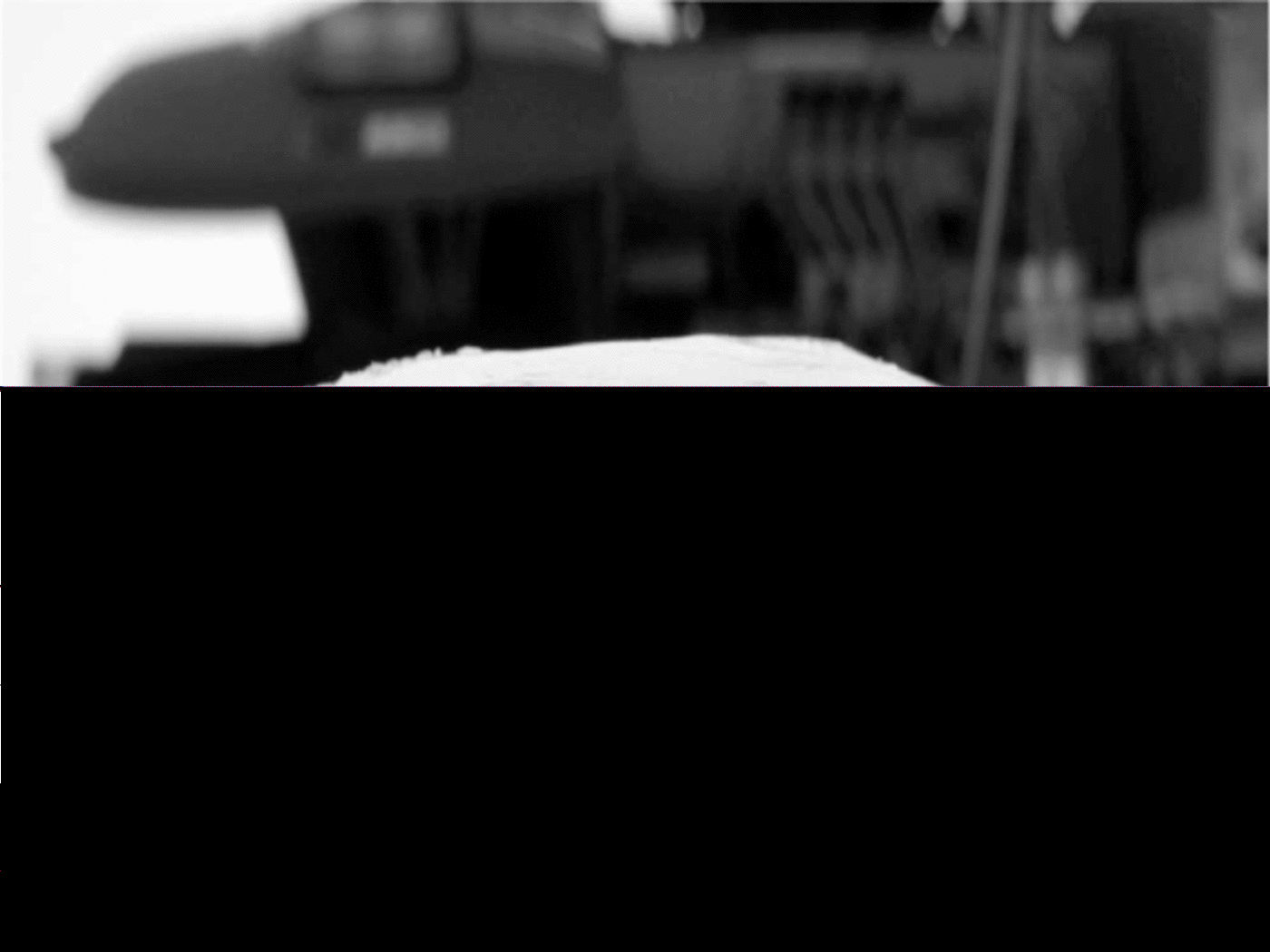
Fig. 11. Low-angle conical plug routinely observed on a flat plate post-test. The flat plate has a diameter of 36 mm.
Cross sections of the hole formed during CPT were not examined after any flat-plate tests, so the existence or otherwise of a compacted perimeter is not known; however, it is surmised that after initial formation of a conical plug on the end of the flat plate, the snow then behaves in a similar manner during penetration, being forced to the sides at the cone shoulder although deformation, destruction and reformation of the conical plug ahead of the flat plate are likely to occur as the penetration process continues, especially through layers of varying hardness.
Discussion with J. Floyer (27 May 2009) clarified that the formation of a compacted zone ahead of a penetrating object in snow is likely to depend upon the size and shape of the indentor, the nature of the snow and probably also the penetration rate. During CPT, the combination of a relatively thin, smooth, sharp penetrometer tip and extremely dry snow appears to have resulted in an immeasurable or negligible compacted zone ahead of the penetrometer, with all fractured particles forced normal to the penetrometer face and thence compacted into the sides at the cone shoulder. The compaction of fractured material into the sides of the hole at the cone shoulder appears to be the dominant displacement mechanism occurring ahead of the 608 steel cone in the dry snow tested, and is consistent with Kinosita (1964), who described the packing of broken ice grains into the compressed region beside or under the cone; snow was preferentially displaced to the side as cone angle decreased.
When a flat plate was used, a compacted zone of snow (approaching the density of ice) was formed on the plate during testing. Although the snow in question was again very dry and likely not conducive to bonding, it is surmised that fracture, compaction and then pressure melting of particles occurs ahead of the flat plate. The depression of the melting point of ice varies between ~ 0.08 and ~ 0.1 K MPa−1 (depending on the saturation state of the air; Reference HookeHooke, 2005), and pressures during flat-plate penetration approached 10 MPa, suggesting that a 1°C depression of the ice melting point may be possible. (Note also that actual pressures on the plate face may exceed those recorded, owing to the limitations of the CPT data-acquisition system.) Snow temperatures were not routinely recorded during CPT, but outside air temperatures occasionally reached >0°C, hence the existence of some pressure melting ahead of the flat plate cannot be discounted. It is surmised that this conical zone formed after a certain distance and probably deformed throughout the test, growing in size, yet also probably deflecting additional particles (because of its conical shape) as penetration continued. The formation of a similar ‘body’ is reported by Gill (1968) in his work on agricultural soils. He notes that ‘the compaction and adhesion of soil to blunt rigid bodies … results in the formation of soil bodies’; when the tool is blunt a clear and distinct soil body forms on the body of an advancing penetrometer.
The formation of compacted material on a penetrating flat plate appears possible and is consistent with observations in other geomaterials. During penetration with a 60° cone in dry polar snow it appears that fractured material is displaced preferentially to the sides and no compacted zone is formed ahead of the cone. The compaction or densification of the snow alongside the cone also has obvious implications for the friction measurement obtained via the friction sleeve.
Pressure melting
Floyer (2008) cautions against stopping during penetrometer pushes, because fractured snow could re-bond, resulting in force spikes (not related to actual snow hardness) upon recommencement of a push. Melting and re-sintering was expected, yet none was visibly or aurally evident while conducting CPT, nor does examination of CPT data suggest any freezing-in occurred. In one test, the cone was left stationary in situ for ~ 1 hour to conduct a dissipation test (a test typically conducted during CPT to measure pressure/resistance changes while the cone is held stationary). No ‘spike’ in resistance (suggesting stiction or adhesion between cone/rods and snow) was observed upon resumption of the test. This may be because of the limited data sampling of the equipment used, or may be evidence of a lack of pressure melting.
A simple quantitative assessment of this phenomenon can be obtained by consideration of melting point depression, as discussed above. Cone tip resistance values were typically <10 MPa, hence at snow temperatures of ~-10°C it is extremely improbable that melting occurred. This is substantiated by Barnes and others (1971), who found that when brass slid on ice (at maximum applied pressure of ~1 MPa) no melting occurred at speeds <100 mm s-1 at a temperature of –12°C. The increase in pressure required to generate melting during penetration does not appear likely with the testing conditions discussed herein.
Conclusion
Support from BAS, Lankelma and Gardline Geosciences enabled the development of innovative CPT equipment that can be mounted onto the three-point hitch of a standard tractor, and be used to perform CPT to depths of >5 m in polar snowpacks. The box and associated CPT equipment proved secure, robust and versatile and was very well suited to the envisaged task. CPT enabled the collection of both tip resistance and not previously recorded sleeve friction data, offering insight into many phenomena pertaining to the assessment of the stratigraphy, hardness and strength of polar snow. This paper provides an introduction to phenomena that should be considered when attempting to interpret CPT in polar snow. CPT appears very well suited to the rapid assessment of polar snow for infrastructural site investigation purposes and, with further testing, analysis and equipment refinement, CPT could prove a valuable scientific tool for rapid in situ assessment of polar snow.
Acknowledgements
This research was made possible by the generous assistance of Lankelma and Gardline Geosciences and the British Antarctic Survey and Halley Research Station. This paper was considerably improved by the suggestions of three anonymous reviewers; their time and effort is appreciated.