Impact statement
The proliferation of microplastic fibres into waterways during the laundering of synthetic textiles and apparel has become a well-known pollution source. There is a current lack of consensus between research communities about which fabric parameters and production techniques are favourable to reduce pollution released from textiles during laundering. With upcoming restrictions, legislations and a push to meet international Sustainable Development Goals on the environmental impact of the textile and apparel industry, there is a need to establish clear and robust textile production processes that can reduce the amount of microplastic fibres shed when washing synthetic textiles. This research addresses source interventions of microplastic fibre pollution through design and manufacturing techniques in the production of the fabric with systematic in-house fabric creation and standardised wash tests.
Introduction
Every time we wear and wash synthetic clothing, microscopic particles are released or broken off from a textile and secondary microplastics are released into the air and wastewater (Browne et al., Reference Browne, Crump, Niven, Teuten, Tonkin, Galloway and Thompson2011). Due to the synthetic source, these microscopic particles are often referred to as ‘microplastic fibres’ which coincided with researchers categorising microplastic pollution found in environmental samples using size and shape to characterise them (Chubarenko et al., Reference Chubarenko, Bagaev, Zobkov and Esiukova2016; Napper and Thompson, Reference Napper and Thompson2016; Frias and Nash, Reference Frias and Nash2019). However, whether the textile is produced of man-made synthetic material, man-made regenerated cellulosic material or a natural material, all textiles release microscopic fibres during wear and washing; and thus, the term ‘microfibres’ has evolved as this encompasses pollution from synthetic, semi-synthetic and natural fibres (Athey and Erdle, Reference Athey and Erdle2021). As this is an emerging pollutant within an interdisciplinary area of research, the terminology used is not consistent (Yan et al., Reference Yan, Henninger, Jones and McCormick2020). For this research, the term microfibre will be used when discussing the environmental pollutant of microscopic fibres of synthetic, semi-synthetic and natural polymers that are below 5 mm in length (Browne et al. Reference Browne, Crump, Niven, Teuten, Tonkin, Galloway and Thompson2011; Napper and Thompson, Reference Napper and Thompson2016; Athey and Erdle, Reference Athey and Erdle2021). Microplastics will refer to any synthetic solid particle or polymeric matrix, with regular or irregular shape and with size ranging from 1 μm to 5 mm, which includes the pollution released from washing of synthetic textiles (Frias and Nash, Reference Frias and Nash2019).
It is estimated that around 200–500,000 t of microfibres enter the oceans annually and the washing of synthetic clothing has been named as the largest contributor of microplastic pollution to our oceans (Boucher and Froit, Reference Boucher and Froit2017; EEA, 2023). However, there is still a lack of consensus within research on the release mechanisms of microfibres during washing alongside the exact production and manufacturing parameters that could be utilised during the design and manufacturing processes that could reduce the amount of pollution released as the textile is washed over its lifetime (EC, 2022; EEA, 2023).
It is of great importance to tackle this pathway of waste to our environments as microfibre pollution has been identified in numerous marine and terrestrial environments, including deep-sea trenches (Jamieson et al., Reference Jamieson, Brooks, Reid, Piertney, Narayanaswamy and Linley2019), within ice and snow in the Artic (Ross et al., Reference Ross, Chastain, Vassilenko, Etemadifar, Zimmermann, Quesnel, Eert, Solomon, Patankar, Posacka and Williams2021), and at the peak of Mount Everest (Napper et al., Reference Napper, Davies, Clifford, Elvin, Koldewey, Mayewski, Miner, Potocki, Elmore, Gajurel and Thompson2020). These studies emphasise the pervasive distribution and global environmental impacts of microfibre pollution (Jamieson et al., Reference Jamieson, Brooks, Reid, Piertney, Narayanaswamy and Linley2019; Ross et al., Reference Ross, Chastain, Vassilenko, Etemadifar, Zimmermann, Quesnel, Eert, Solomon, Patankar, Posacka and Williams2021).
Alongside the pollution’s persistence and pervasiveness, microfibres are of concern due to the ability to act as vectors for toxins from production, manufacturing processes and environmental adsorption (Athey et al., Reference Athey, Carney Almroth, Granek, Hurst, Tissot and Weis2022). For synthetic, semi-synthetic and natural fibres, numerous chemicals are used within the production process of the yarns and textiles (i.e., petrochemicals and additives for synthetic and semi-synthetic fibres and pesticides for natural fibres); additionally, chemicals are intentionally added during the production of garments for favourable characteristics and functionality such as dyes, anti-wrinkle properties, water resistance and thermal stabilisers (Carney Almroth and Athey, Reference Carney Almroth and Athey2022). Furthermore, microfibres have been shown to have the ability to adsorb toxins within the environment such as endocrine-disrupting chemicals readily found in waste-water treatment plants, which allows microfibres to act as a vessel for transport for toxins (Frost et al., Reference Frost, Bond, Sizmur and Felipe-Sotelo2022).
Due to these concerns, coupled with the proliferation of microfibre pollution and the chemical and physical effects, microfibres and related research to assess the release has been made a key priority within the EU circular economy plan (EC, 2022; EEA, 2023).
To provide more contextual information, when looking at textiles there are multiple stages at which microfibres can break off and enter the environment. For simplification purposes, garments are created in three broad stages: yarn production, fabric creation and garment production. Raw fibres of various lengths (staple fibres) or continuous threads (filament fibres) are spun or twisted together to create yarn. This yarn can then be woven or knit together to form a fabric. Garments are produced via cut and sew methods whereby fabric is cut into panels and joined together to form a garment that is applicable to knit of woven fabrics, seamless garment technology where complete garments are created from minimal panels of fabric (thus little to no cutting and sew process), which is generally applicable to knit fabrics only. When textiles are subject to mechanical and chemical stress, such as laundering, it can lead to fibre damage, fragmentation, pill formation and ultimately microfibre pollution, which is detached and released from the surface or edge of the fabric (Figure 1).

Figure 1. Schematic of shedding mechanism of microfibres.
Note: Photos: authors own.
The chemical and mechanical stress can also be adjusted during the laundering factors or settings such as how water volume relates to release of microfibres (Kelly et al., Reference Kelly, Lant, Kurr and Burgess2019), how washing load affects wettability and mechanical stress placed on fabrics (Volgare et al., Reference Volgare, De Falco, Avolio, Castaldo, Errico, Gentile, Ambrogi and Cocca2021) or how detergent, fabric softener or temperature of wash can provide consumer-facing practical actions relating to microfibre pollution (Zambrano et al., Reference Zambrano, Pawlak, Daystar, Ankeny, Cheng and Venditti2019; Cotton et al., Reference Cotton, Hayward, Lant and Blackburn2020). Opposingly, this research aims to assess how source-directed interventions within the design and manufacturing process can influence microfibre pollution released, to be implemented before or alongside consumer-based mitigation strategies. This work will be conducted through systematically changing the structure of the fabric as well as the edging technique to assess how microfibres are released.
To combat the release of pollution from washing of clothing and textiles “focus needs to be placed on the design and production stages in order to avoid fibre fragmentation and, therefore, the potential for microfibre release in the first place” (Ellen MacArthur Foundation, 2021, p. 10). This has been echoed in upcoming international regulations. The European Commission has proposed several laws targeting sustainability within the textile and apparel industry, including regulations to tackle the unintentional release of microfibres into the environment (EC, 2022). Extended producer responsibility policies have been named as one possible way to advocate through cost–benefit analysis that innovation, technological adoption or intentional textile design to reduce or limit microfibre pollution during fabric washing and use is of up-most importance and is economically viable (Eunomia, 2022).
Prevention of microfibre pollution centres around the eco-design of products to release less fibre pollution during the product’s lifetime (Ellen MacArthur Foundation, 2021; Eunomia, 2022). A few studies have established that there are particular fabric constructions or parameters that lead to reduced microfibre loss during wear and washing (Carney Almroth et al., Reference Carney Almroth, Astrom, Roslund, Petersson, Johansson and Persson2018; Zambrano et al., Reference Zambrano, Pawlak, Daystar, Ankeny, Cheng and Venditti2019; De Falco F et al., Reference De Falco, Cocca, Avella and Thompson2020). Yang et al. (Reference Yang, Qiao, Lei, Li, Kang, Cui and An2019, p. 6) stated “more studies are needed to better understand the role of textile structure which can be re-designed to prevent (microfibre) release”.
For instance, Berruezo et al. (Reference Berruezo, Bonet-Aracil, Montava, Bou-Belda, Díaz-García and Gisbert-Payá2020) identified for woven fabrics that different weave patterns may correspond to different amounts of microfibres shed due to differing interlacing coefficients and weft density. Density of fabric was also explored by Raja Balasaraswathi and Rathinamoorthy (Reference Raja Balasaraswathi and Rathinamoorthy2021), in which different knit fabrics were analysed, and stitch density and tightness factor were shown to have potential implications for microfibre shedding. In contrast, Yang et al. (Reference Yang, Qiao, Lei, Li, Kang, Cui and An2019) identified that with increasing the tightness of the structure, and therefore increasing the yarn count per cross section this could increase microfibre shedding. However, within previous work, fabric samples were bought from local markets or stores and thus the production process or textile history may be different between samples, alongside multiple fabric parameters being changed such as yarn twist and polymer type (Yang et al., Reference Yang, Qiao, Lei, Li, Kang, Cui and An2019; Raja Balasaraswathi and Rathinamoorthy, Reference Raja Balasaraswathi and Rathinamoorthy2021). This is further emphasised by Zambrano et al. (Reference Zambrano, Pawlak, Daystar, Ankeny, Cheng and Venditti2019), in which fabric types of differing polymers but the same knit construction had varying amounts of microfibres released during laundering. This was due to the fabrics neither being from the same brand, nor being made in the same way nor purchased from commercial retailers. Therefore, fabric and yarn constructions “should not be generalised” (Zambrano et al., Reference Zambrano, Pawlak, Daystar, Ankeny, Cheng and Venditti2019, p. 6).
This research assesses how source-directed interventions within the design and manufacturing process can influence microfibre pollution released from textiles during washing. Selected textile structures will be assessed to analyse the potential to reduce the amount of microfibres released from the structures during the life cycle of the garment and therefore the potential environmental impact. Fabric parameters such as yarn used, production and wash conditions were kept constant to assess the influence of textile structure on the release of microfibres. Additionally, the use of laser cutting during the production process compared to scissor cut-overlock edged fabrics will be analysed to understand how fibres are released from the edge of fabric swatches, as these are commonly used techniques within the textile and apparel industry (Cai et al., Reference Cai, Mitrano, Heuberger, Hufenus and Nowack2020). This research is necessary to accelerate and encourage cross-industry collaboration, combat microfibre pollution and meet sustainability and environmental goals.
Methodology
Fabric creation
Polyester yarn (polyethylene terephthalate [PET]) was chosen as this is a synthetic yarn derived from petroleum and washing of synthetic clothing has been named as the largest contributor to ocean microplastic pollution (Boucher and Froit, Reference Boucher and Froit2017). PET constitutes around 80% of global polymer production, 60% of which is used within the textile industry (Majumdar et al., Reference Majumdar, Shukla, Singh and Arora2020; Palacios-Marín et al., Reference Palacios-Marín, Jabbar and Tausif2022).
For this research, fabrics were created in-house within the Department of Materials at The University of Manchester, this allowed us to gain full control and knowledge of the fabric’s history (Carney Almroth et al., Reference Carney Almroth, Astrom, Roslund, Petersson, Johansson and Persson2018).
All knit fabrics were created on a Dubied knit machine with 10-gauge using 1 cone of undyed intermingled polyester filament yarn (2 ply, 167 dtex with 48 filaments in each end) purchased from J. H. Ashworth and Sons Ltd. Initially, single jersey fabric was created to mimic that of a top-weight fabric such as that found in a T-shirt, which is a popular knit structure that has been studied in previous research and makes up 8% of apparel sold in Europe, North America and Australia (Kelly et al., Reference Kelly, Lant, Kurr and Burgess2019; Cesa et al., Reference Cesa, Turra, Checon, Leonardi and Baruque-Ramos2020; Cotton et al., Reference Cotton, Hayward, Lant and Blackburn2020; Frost et al., Reference Frost, Zambrano, Leonas, Pawlak and Venditti2020; Volgare et al., Reference Volgare, De Falco, Avolio, Castaldo, Errico, Gentile, Ambrogi and Cocca2021). For woven fabrics, the same undyed intermingled polyester filament yarn (2 ply, 167 dtex with 48 filaments in each end) was used to ensure that the yarn parameters were kept constant. The woven fabric was created using an ARM AG CH-3507 BIGLEN semiautomatic hand weaving machine connected to ScotsWeave software to create a 2-by-2 twill woven fabric that was selected to mimic fabric commonly found in bottom weight fabrics, for example denim jeans and workwear trousers, which are the most worn items of clothing globally and cover around 5% of the total textile market (Raina et al., Reference Raina, Gloy and Gries2015; Athey et al., Reference Athey, Adams, Erdle, Jantunen, Helm, Finkelstein and Diamond2020).
Following the fabric creation, both the knit and woven fabric were heat set at 180 °C for 45 seconds to remove residual shrinkage.
Eight single jersey fabric and eight 2-by-2 twill woven fabric swatch samples were created using a laser cutter (FB1500) with a maximum power of 75 and maximum velocity of 300. Then, 9 cm × 9 cm size swatches were chosen due to being the most common size used within previous work (e.g., De Falco et al., Reference De Falco, Di Pace, Cocca and Avella2019).
To test edging effects and adoption/substitution of technology and the effect on microfibre release during laundering another eight single jersey fabric swatches were created. These were cut to size with a scissor cutting technique and edged with an overlock serging technique using a Brother 3–5 thread DB2-B755 industrial sewing machine. Then, 100% polyester Isacord thread was used for the overlock serging. Seaming and finishing of fabric swatches is necessary for neatening the edges of woven fabrics alongside stabilising the structure in knit fabrics, especially as knit fabrics are liable to unravel or ladder (Spencer, Reference Spencer2001).
The edging effects of woven fabrics was omitted within this work due to woven fabrics being explored within the early stages of research before knit fabrics and the reduction on pollution during laundering was focused due to their potential higher shedding rates.
The physical properties of the fabrics are shown within Table 1. For ease, abbreviations of the fabric swatches will be used, that is, single jersey knit fabrics edged with overlock will be referred to as SJK-O, the single jersey knit fabric swatches that were laser cut to size referenced as SJK-LC and the 2-by-2 twill fabrics laser cut to size as TW-LC.
Table 1. Fabric characteristics and specifications of sampled textiles

Note: Raised yarn length measure using ImageJ software as outlined by Raja Balasaraswathi and Rathinamoorthy (Reference Raja Balasaraswathi and Rathinamoorthy2021) which is shown in Supplementary Figures S1 and S2 in the Supplementary material.
Washing and quantification of shed microfibres
To remove residual contamination such as airborne microplastics, dust and other residue, the fabrics were prewashed in distilled water prior to the microfibre shedding analysis. The fabric swatches were dried overnight within the laminar flow cabinet before the pre-wash weight of each swatch was recorded using a Fisher PS-60 balance with a readability of 0.1 mg.
The fabric swatches were washed in accordance with the microfibre shedding test standards AATCC TM212–2021 and ISO 4484-1:2023 (AATCC, 2021; BSI, 2023). In short, individual fabric swatches were put into preheated stainless-steel canisters (550 mL capacity) with 360 mL of MilliQ water and 50 stainless steel balls (diameter = 6 mm). The fabric swatches were washed in a wash stimulator (Washtec, Roaches UK) for 40 minutes at 40°C. In accordance with ISO 4484-1:2023, detergent was omitted from the wash method because of its potential of clogging the filter or attaching to fibres and distorting results (BSI, 2023).
Following the wash cycle, the wash liquor was filtered through a pre-weighed Whatman GF/C 55-mm glass microfibre filter with a pore size of 1.2 μm, with the aid of a vacuum filter apparatus. The filter membranes were placed into individual petri dishes and placed within the laminar flow cabinet to dry. Once a constant weight was reached, a post-wash weight of each filter membrane was recorded.
As with previous studies, statistically significant differences between test samples were shown with a one-way analysis of variance, acknowledged with P values less than 0.05 (Cui and Xu, Reference Cui and Xu2022; Palacios-Marín et al., Reference Palacios-Marín, Jabbar and Tausif2022).
As this work uses microscale changes in weight and microscopic fibres, contamination control is essential (Prata et al., Reference Prata, Castro, da Costa, Duarte, Rocha-Santos and Cerqueira2020). Similar to other microplastic work, decontamination controls were taken such as cleaning of surfaces and floors before use and prior to wash tests, canisters, steel balls, filter funnel and glass petri dishes were triple rinsed with filtered water before use (Woodall et al., Reference Woodall, Gwinnett, Packer, Thompson, Robinson and Paterson2015; Prata et al., Reference Prata, Reis, da Costa, Mouneyrac, Duarte and Rocha-Santos2021). For this study, the researchers also wore white cotton lab coats and worked within laminar flow cabinets to reduce potential self-contamination of laboratory environment and samples from clothing (Scopetani et al., Reference Scopetani, Esterhuizen-Londt, Chelazzi, Cincinelli, Setala and Pflugmacher2020). Procedural blanks were undertaken, and results were subtracted from test results (Özkan and Gündoğdu, Reference Özkan and Gündoğdu2020; BSI, 2023).
Images of the edges of the fabric were taken on a Canon EOS 2000d camera with MP-E 65 mm macro lens.
Detailed description of washing parameters, filtering mechanism and contamination control is available within the Supplementary material.
Results and discussion
To compare fabric structure on the amount of microfibres released during laundering, the wash test results of the SJK-LC fabric swatches are compared to the TW-LC fabric swatches. From the wash tests, the SJK-LC swatches released over three times more microfibres than the TW-LC swatches. On average, the eight SJK-LC swatches show 21.44 mg/kg of microfibres shed during laundering, compared to 6.64 mg/kg from the TW-LC fabric (Figure 2). Statistical analysis showed a significant difference between these two fabric types (P < 0.0001). As these fabric swatches were created with the same yarn and edged with laser cutting, the differences in microfibres shed indicate that fabric structure does have an impact on the amount of microfibre pollution released during laundering. This is supported by previous findings, whereby looser structured knitted fabrics shed more microfibres during washing processes compared to tightly woven structures (Yang et al., Reference Yang, Qiao, Lei, Li, Kang, Cui and An2019). This has been attributed to “greater elasticity due to its coil and snare structure” of the knit fabric compared to the woven fabric made of “interwoven warp and weft yarns, which have more interweaving points and tighter structure” (Cui et al., Reference Cui and Xu2022, p. 9). Future work could also aim to assess compactness of fabrics through other avenues such as permeability.
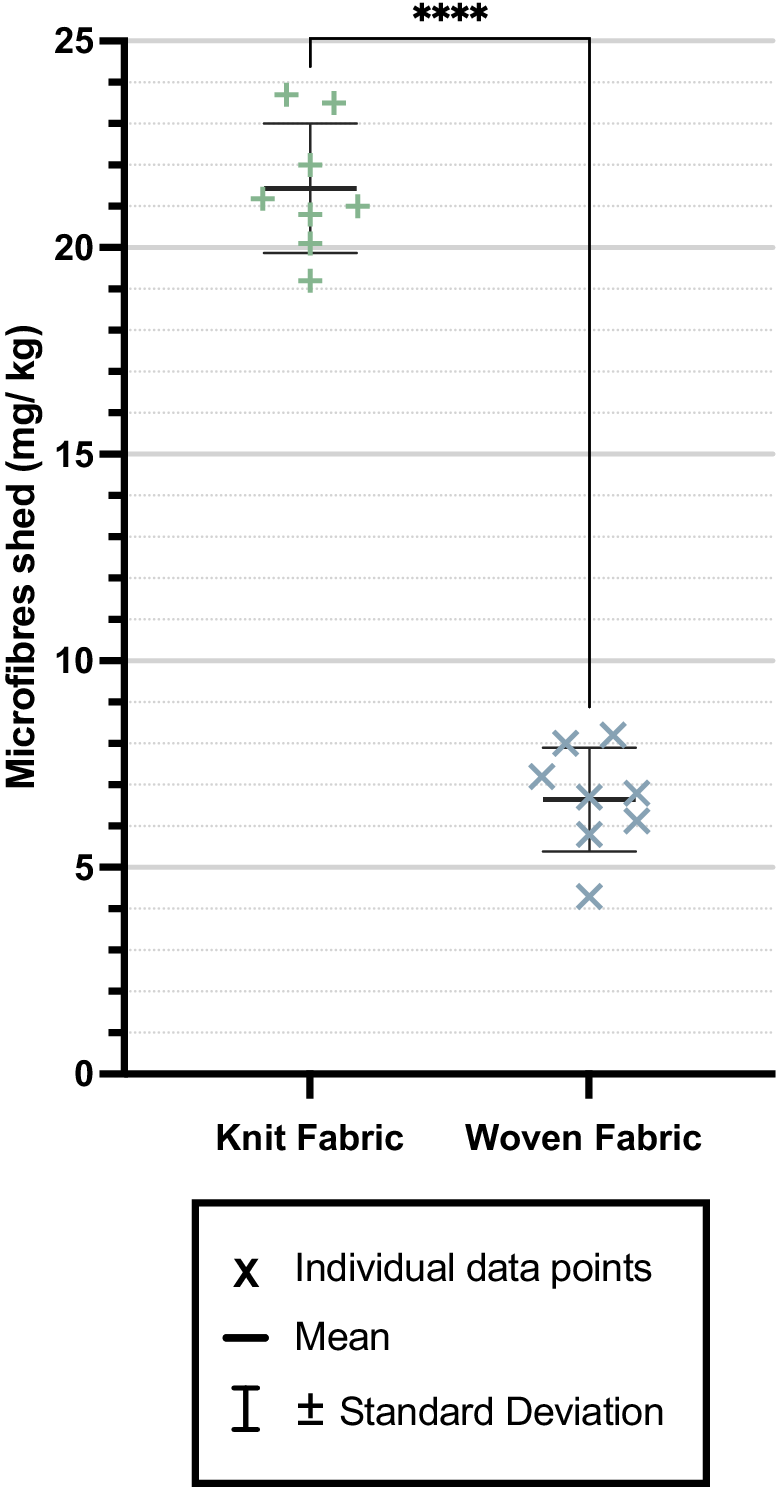
Figure 2. Microfibre shedding from single jersey knit fabric swatches (n = 8) and 2-by-2 twill woven fabric swatches (n = 8) during laundering fibre fragment test.
Note: Statistically significant differences (P < 0.0001) detected by statistical analysis shown with ****.
This research agrees with other research that there is an ‘optimal’ structure for garment creation to reduce microfibre shedding. For example, “very compact woven structure and highly twisted yarns made of continuous filaments” released less microfibres when compared to those with a looser structure such as knit fabrics, made of short staple fibres and lower twist (De Falco et al., Reference De Falco, Cocca, Avella and Thompson2020, p. 1). Several studies show that fabric characteristics are influential in fibre shedding, however, as multiple fabric or yarn parameters are changed at the same time and therefore “very little information is available on which specific parameters of the textile have the greatest influence and more research is needed to help guide interventions to reduce microfibre emission” (Napper and Thompson, Reference Napper and Thompson2022, p. 140). This work advances previous work as the fabrics for this study were created in-house and yarn parameters were kept constant which has allowed individual fabric structure parameters to be explored.
The 2-by-2 twill woven structure had several differences to the single jersey knit fabric, including the woven fabric having a significantly shorter raised yarn length of the woven fabric compared to the knit fabric (Table 1). A negative correlation is shown with the shortening of the raised yarn length relating to a lower rate of releasing microfibres during laundering. This supports similar results whereby tighter fabrics, such as woven fabrics, released less microfibres (Yang et al., Reference Yang, Qiao, Lei, Li, Kang, Cui and An2019; Raja Balasaraswathi and Rathinamoorthy, Reference Raja Balasaraswathi and Rathinamoorthy2021).
In contrast to this, Carney Almroth et al. (Reference Carney Almroth, Astrom, Roslund, Petersson, Johansson and Persson2018) noted that “more tightly knitted fabric results in more fibres in the same area of fabric resulting in greater fibre loss” (pg. 5). However, this was dismissed by other work that showed that fabrics with higher number of fibres present per unit area and the greatest weight released the least amount of microfibres (De Falco et al., Reference De Falco, Gullo, Gentile, Di Pace, Cocca, Gelabert, Brouta-Agnesa, Rovira, Escudero, Villalba, Mossotti, Montarsolo, Gavignano, Tonin and Avella2018). As shown in Table 1, the woven fabric is also the heavier of the two fabric samples, and yet has released the least microfibres of the two fabrics supporting the findings of De Falco et al. (Reference De Falco, Gullo, Gentile, Di Pace, Cocca, Gelabert, Brouta-Agnesa, Rovira, Escudero, Villalba, Mossotti, Montarsolo, Gavignano, Tonin and Avella2018). By taking this into account, the textile and apparel industry could adopt designs that allow for lower raised yarn lengths and more tightly constructed fabrics as a source-directed intervention of microfibre pollution release. Nevertheless, the complexities of fabric parameters and their influence, or proportional influence, on microfibre shedding is an area for continued research efforts that will be aided by systematic studies using a standardised methodology.
From a design point of view, there are methodical reasonings of why garments are created from knit or woven structures have loose or tight constructions such as comfort, breathability and aesthetics (Hari, Reference Hari2012). Thus, it might not be economically and logistically feasible to switch fabric structures for environmental pollution reasons. Therefore, this work also investigated the use of how garments may be constructed, such as either using scissor cutting techniques followed by overlock serge stitching, or laser cutting to finish the raw edge of fabric and prevent fraying. These are two techniques commonly used within the textile and apparel industry within garment making, and this work shows that depending on the technique used, the environmental pollution released over the garments lifetime could be impacted (Nayak and Padhye, Reference Nayak and Padhye2016).
Scissor cutting and overlock serging of seams (SJK-O fabric) released statistically significant amounts of microfibres (average of 30.61 mg/kg) compared to laser cutting (SJK-LC, Figure 3, 19.63 mg/kg). As the fabric creation, yarn and fabric parameters were kept constant, it can be indicated that the hemming technique significantly influences the number of released microfibres during laundering (indicated with a P value less than 0.0001). This also highlights that a significant amount of microfibres is released from the edges of fabrics, as the yarn and fabric structure were kept constant.

Figure 3. Microfibres shedding from a wash cycle of eight fabric swatches of single jersey polyester fabrics created in the same structure but with differing hemming techniques, that is, laser cutting versus overlock serge.
Note: Average amount of microfibres released (mg/kg) is shown with thick line. Statistically significant differences (P < 0.0001) detected by statistical analysis shown with ****.
From further analysis, it was shown under microscope imaging that the laser cutting of the edges of the synthetic fabric created a seal of molten fabric, compared to raw edges that were displayed by the scissor cut samples (Figures 4 and 5). This was caused as the synthetic fabrics melted under the laser, causing the edge to seal (Nayak and Padhye, Reference Nayak and Padhye2016). The raw edges would allow for the fraying of the fabric and consequentially release fibres from these edges, which was displayed by an increased release of microfibres compared to the molten heat-sealed edges created by the laser cutter (Cai et al., Reference Cai, Mitrano, Heuberger, Hufenus and Nowack2020). During the overlock serging, the edges were single folded once, which permitted the raw edge of the fabric to be exposed and allow for fibre fragments to protrude (Dalla Fontana et al., Reference Dalla Fontana, Mossotti and Montarsolo2021). These findings are consistent with previous studies where laser cut versus scissor cut fabric swatches showed that the latter increased microfibre pollution by 3–31 times (Cai et al., Reference Cai, Mitrano, Heuberger, Hufenus and Nowack2020) and that fabrics hemmed with overlock serge compared to heat sealing shed more microfibres (Dalla Fontana et al., Reference Dalla Fontana, Mossotti and Montarsolo2021). However, with fabric samples examined in the aforementioned research, the fabrics were obtained directly from different manufacturers (Cai et al., Reference Cai, Mitrano, Heuberger, Hufenus and Nowack2020; Dalla Fontana et al., Reference Dalla Fontana, Mossotti and Montarsolo2021). Within this research, the yarn and manufacturing techniques were kept constant to allow for a more direct comparison of the influences of microfibre detachment during laundering.

Figure 4. (a) Microscopic images of single jersey knit fabrics cut and hemmed with laser cutting technique. (b) X5 magnification images shows molten edge of the synthetic fabric fused from the laser.
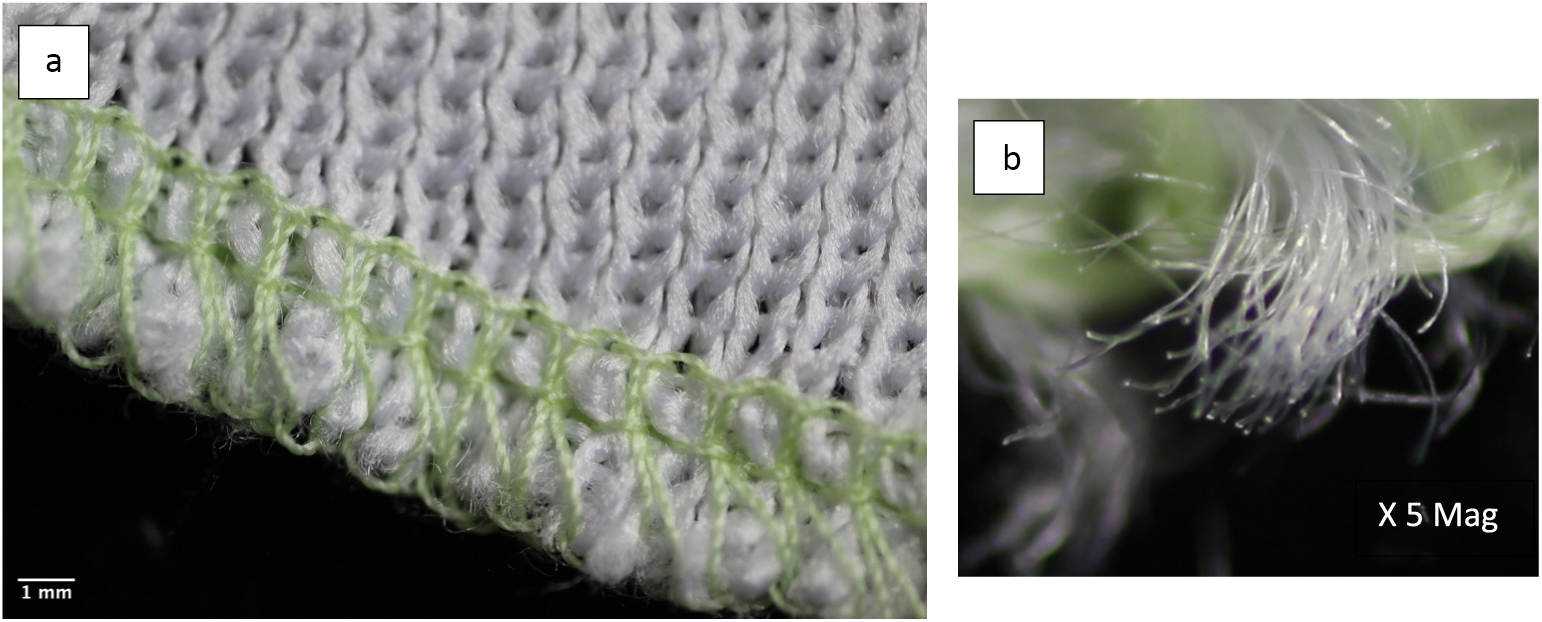
Figure 5. (a) Microscopic images of single jersey knit fabrics scissor cut and hemmed with overlock serging using 100% polyester yarn. (b) X5 magnification images shows loose fibres protruding from the edge of the fabric.
To continue this research, further systematic studies are needed to assess different types of hemming techniques such as double folded or piped hem could also be assessed, alongside influence of laser cutting settings such as speed or power used. It should be noted that careful monitoring of the impact of these changes from a consumer comfort perspective is essential, for example, double folded edges may cause bulky seams, or the laser cut edges may provide discomfort when wearing. For future microfibre shedding wash tests, it is crucial to explain how, and which manufacturing technique is used to create fabric swatches to size, as this can have a significant impact on the fibres shed from the fabric (Cai et al., Reference Cai, Mitrano, Heuberger, Hufenus and Nowack2020; Dalla Fontana et al., Reference Dalla Fontana, Mossotti and Montarsolo2021).
The international standards suggested for determining material loss from fabrics during laundering such as AATCC TM212-2021 and ISO 4484-1:2023 use hemming techniques of single fold overlock serge (AATCC, 2021; BSI, 2023). However, previous studies have frequently used laser cutting to create fabric swatches for microfibre shedding tests due to benefits such as saving time and heat sealing of edges (Carney Almroth et al., Reference Carney Almroth, Astrom, Roslund, Petersson, Johansson and Persson2018; Kelly et al., Reference Kelly, Lant, Kurr and Burgess2019; Yang et al., Reference Yang, Qiao, Lei, Li, Kang, Cui and An2019; Cai et al., Reference Cai, Mitrano, Hufenus and Nowack2021). In the interest of future comparability to gain greater knowledge of textile articles that may minimise shedding during the textile lifecycle, it is our suggestion that all research should outline hemming techniques used. A caveat to direct comparison of microfibre washing tests and understanding attributes of textile parameters has been highlighted with this work and shows that care should be taken when comparing fabric with differing hemming techniques. In the future, comparisons of microfibre shedding should acknowledge hemming and tailoring techniques of fabric swatches or garments.
Although the fashion industry has shifted to become more sustainable, with concepts of the ‘circular economy’ becoming prominent, these focus predominantly on re-looping sources in open- and closed-loop systems and do not necessarily address the microfibre pollution issues. For instance, Majumdar et al. (Reference Majumdar, Shukla, Singh and Arora2020) investigated how common waste such as PET bottles may be recycled into textile-grade polyester fibres for clothing. However, there are challenges associated with this in that recycled PET implies a lowering of tensile strength when compared to virgin polyester fibres, which has been linked to higher microfibre release during washing (Frost et al., Reference Frost, Zambrano, Leonas, Pawlak and Venditti2020), thus, highlighting potential complications when addressing microfibre pollution.
As such, policies that interact cross-industrially with producers and manufactures of textiles and apparel could have the potential to reduce microfibre pollution from the source as “at the top of the waste hierarchy is prevention, followed by minimisation and reuse” (Kentin and Battaglia, Reference Kentin, Battaglia, Weis, Falco and Cocca2022, p. 275). While this research attempts to “design out” microfibre pollution, with current techniques and finishes on the market, due to the nature of yarn, polymers and the fabrics themselves, there will never be zero pollution released from textiles during washing. Therefore, to advance the industry towards a circular economy for textiles, it is suggested that pre-washing of textiles at the manufacturing stage and the capture of these microfibres could play an important role as “synthetic fabrics tend to release the highest amounts of microfibres in the first 5–10 washes” (EEA, 2023). By addressing this pollution in a collaborative manner with the whole design and production pathway in mind, it would allow a ‘known source’ of microfibre pollution to be captured and allow for more efficient recycling and re-looping of valuable materials.
As the UNEP and UNFCCC call for the textile and apparel industry to market their products towards the “true cost across environmental and social factors” (UNEP and UNFCCC, 2023, p. 52) in order to meet the UN Sustainable Development Goals, it can be suggested that design and manufacturing processes incorporate tightly constructed fabrics that are tailored to size with laser cutting technology.
Conclusion
This work has demonstrated that significant amounts of microfibres are shed from the structure of the fabric itself as well as the edges of the fabric. The design of textiles and apparel can be manipulated as an upstream intervention of the release of microfibres from textiles during laundering. Tight structures such as woven fabrics were shown to release less microfibres than knit due to the structure of the fabric and the tightness that lead to less fibres slipping from the structure. Additionally, the cutting and hemming technique can be utilised to reduce the amount of pollution released during laundering, with laser cutting of synthetic fabrics creating a molten edge that seals the edge of the fabric and thus permitting less microfibres to be released than that of the raw edge created from scissor cutting of fabrics and hemming with overlock serge technique. As the textile and apparel industry moves towards being holistically responsible for products environmental impact through voluntary and involuntary actions, these techniques and innovations should be communicated to the industry and implemented to reduce the amount of microfibres released during laundering and thus reduce the amount of microfibre pollution flowing into our marine and terrestrial environments.
Open peer review
To view the open peer review materials for this article, please visit http://doi.org/10.1017/plc.2024.20.
Supplementary material
The supplementary material for this article can be found at http://doi.org/10.1017/plc.2024.20.
Data availability statement
The data that support the findings of this study are available from the corresponding author, Elisabeth Allen, upon request.
Acknowledgements
The authors gratefully acknowledge the contributions of Laura Kavanagh, Elizabeth Carlton, Hannah Rampley and Damindi Jones of the University of Manchester and Dr. Celina Jones of Manchester Metropolitan University for their support within the creation of the fabrics and washing experiments. The authors would also like to extend their gratitude to Professor Andrew Mayes of the University of East Anglia for his generosity in training and supplying the imaging equipment used within this work.
Author contribution
This manuscript was written through contributions of all authors.
Elisabeth Allen: Conceptualisation, investigation, methodology, writing – original draft.
Claudia E Henninger: Conceptualisation, methodology, writing – review and editing.
Jane Wood: Writing – review and editing.
Edidiong Asuquo: Writing – review and editing.
Arthur Garforth: Conceptualisation.
Financial support
This research is funded by Engineering and Physical Sciences Research Council (EPRSC) through grant No EP-T517823-1 under UK Research and Innovation (UKRI).
Competing interest
The authors declare none.
Comments
Dear Cambridge Prisms: Plastics Editors,
It is with great pleasure to submit our article entitled “Designing Out Microplastic Pollution Released from Textiles and Apparel During Laundering” for consideration in Cambridge Prisms: Plastics Special Issue Innovative and Creative Solutions to Plastic Pollution. Based on the meet the editors’ event at PlasticsFuture2023 conference, we believe that this research article fits well with the journal’s scope.
This research article critically examines how the design of fabric and the edging effects used within the production process impact the amount of microplastic fibres released from textile swatches during wash cycles. As the washing of synthetic textiles is said to be the largest contributors to microplastic pollution in our marine environment, this manuscript focuses on preventative solutions to plastic pollution through source-directed interventions. Within this work we provide insight into how improvements in textile design and adoption of technology within manufacturing processes will aid the production of synthetic textiles with a lower tendency to generate microplastics during washing.
This work is of societal and academic significance due to global environmental concerns on microplastic fibre pollution into our marine and terrestrial environments. Furthermore, as the rate of creation and consumption of synthetic textiles continues to rise, we hope this work sheds light on the creative and innovation solutions within the industry to control the pollution source and highlights the need for further research in this area. With increased concern from the European Commission and European Environment Agency on the release of microplastic fibres from textiles, this work is of industrial and political interest by enhancing and emphasising the opportunities for voluntary and involuntary regulation of microplastic pollution through eco-design. We feel this work is of high impact and would be well suited for Cambridge Prisms: Plastics.
We wanted to thank you in advance for your consideration of our manuscript.
Best wishes,
Elisabeth Allen, on behalf of the authors
University of Manchester, Oxford Road, Manchester, United Kingdom
[email protected]