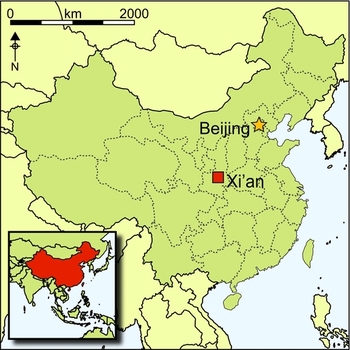
Introduction
The enormous mausoleum complex of Qin Shihuang, the First Emperor of China, is a funerary site of unparalleled importance that is thought to represent a microcosm of his imperial kingdom (Yuan Reference Yuan1990) (Figure 1a). Construction of the elaborate necropolis in Lintong, near Xi'an, Shaanxi Province, China, began when 13-year-old Qin Shihuang ascended to the throne in 247 BC, and was completed upon his death less than 40 years later (Yuan Reference Yuan1990). The workforce may have involved up to 700000 craftsmen and labourers from all corners of the Qin Empire, some of whom were slaves who may have been executed once they had fulfilled their duties (Yang & Yang Reference Yang and Yang1979; Ledderose Reference Ledderose, Blansdorf, Emmerling and Petzet2001: 273). Given that nothing of its kind appears to have existed previously in China, this project would have represented a monumental undertaking that presented numerous technological and logistical challenges.
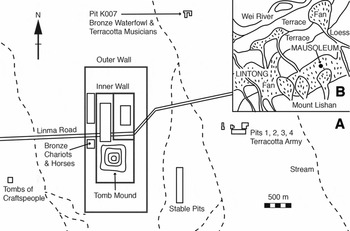
Figure 1. Emperor Qin Shihuang's mausoleum site in Shaanxi Province, China. a) Plan of the mausoleum site with the location of pits mentioned in text; b) map of Quaternary sedimentary deposits in the vicinity of Lintong (modified from Lei et al. Reference Lei, Gao and Yuan2004: 38, fig. 1).
The most renowned aspect of the site is the Terracotta Army, which comprises around 7000 individually crafted, life-sized ceramic warriors, generals and horses, equipped with real weapons and installed in battle formation in three underground pits (Figures 1a & 2a). Several decades of research into the Terracotta Army has resulted in a good understanding of the physical sequence of constructing the statues (Ledderose Reference Ledderose and Ledderose2000; Nickel Reference Nickel and Portal2007). Many questions still remain, however, about their production location(s), manufacturers and craft technology. For example, it is usually assumed that due to the size and weight of the figures, they were probably produced at or near to the mausoleum. No workshops or unequivocal production debris have, however, been discovered in the surrounding landscape; possible mismatches with local raw materials may suggest that they were manufactured elsewhere (e.g. Gao et al. Reference Gao, Zhao, Li, Xie, Han, Feng, Fan, Zhang, Chai, Li, Zhang and Zhu2003; Hu et al. Reference Hu, Zhang, Bera, Ferguson, Li, Shao and Wang2007). Firing so many life-sized clay statues, which have a wall thickness of up to 0.1m, without large numbers of failures, would have required excellent control over temperature and atmosphere, and the careful selection and preparation of raw materials. While kilns large enough to accommodate the 1.8–2m-high soldiers and horses have been found, these contained fragments of bricks and roof tiles (Li Reference Li2007a), prompting some researchers to propose that the warriors were bonfire-fired, or simply left to dry (Wiedemann et al. Reference Wiedemann, Boller, Bayer, Sayre, Vandiver, Druzik and Stevenson1988; Shan et al. Reference Shan, Zhou, Wang, Qin, Zhang, Zhu and Zhang2003). Interpretations of the paste-preparation technology used in the manufacture of the Terracotta Army are equally contradictory, with suggestions of both the intentional modification of raw materials as well as the use of unrefined local clay (Wiedemann et al. Reference Wiedemann, Boller, Bayer, Sayre, Vandiver, Druzik and Stevenson1988; Qin et al. Reference Qin, Pan and Li1989; Shan et al. Reference Shan, Zhou, Wang, Qin, Zhang, Zhu and Zhang2003).
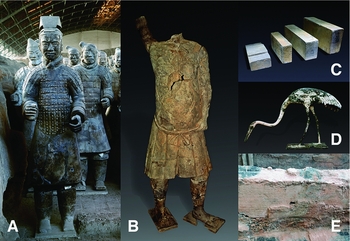
Figure 2. Ceramic artefacts analysed in this study: a) terracotta warrior statue; b) terracotta acrobat; c) bricks used to line pit 1; d) bronze waterfowl; e) rammed-earth wall. (Images b–d provided by Tianzhu Zhang.)
Determining the details of how the terracotta statues were manufactured is crucial for addressing wider questions concerning the craft logistics, standardisation and labour organisation behind the mausoleum complex of the First Emperor, and the administrative procedures of Qin-period China more generally (Barbieri-Low Reference Barbieri-Low2007; Yates Reference Yates and Portal2007; Li et al. Reference Li, Bevan, Martinón-Torres, Xia and Zhao2016). Key questions include the number, size and location of the different workshops involved in the manufacture of the approximately 7000 figures, their cultural/political affiliations, internal organisation and specific roles in the project. Also of interest are possible links between the production of the terracotta statues and other crafts at the mausoleum, and what this can tell us about the planning and administration of the project as a whole.
Study materials and analytical methods
As a first step, we studied an initial dataset of terracotta statue fragments and compared these to ceramic building materials and to clay cores used for the casting of bronze artefacts excavated from the site (Table 1; Figure 2). All samples were analysed microscopically via thin-section petrography (Quinn Reference Quinn2013) to characterise their raw materials, methods of paste preparation and firing. The resulting data has been used to address several unanswered questions concerning the ceramic craft technology and production locations of the terracotta statues and other ceramic objects.
Table 1. Details of ceramic samples analysed from Emperor Qin Shihuang's mausoleum site. QMC = Qin mausoleum ceramics.

Our sample set includes 12 fragments of terracotta warrior statues originating from the largest of the three pits, pit 1 (Figure 1a), which contained the main army. These samples represent different parts of their parent artefacts, including the leg, hand, robe and armour (Figure 2a). Two fragments of ‘terracotta acrobat’ statues (Figure 2b) recovered from pit K9901 (Figure 1a) were also made available for study. Five clay paving bricks from the floor of pit 1 (Figure 2c) were analysed for comparison with the statues, as were three samples of clay core material located within the body or neck sections of several ornate bronze statues of waterfowl (Figure 2d) found in pit K0007 (Figure 1a). Finally, a single sample of rammed-earth wall (Figure 2e) from pit K9901 (Figure 1a) was also studied.
All ceramic artefacts were prepared as 30 μm thin sections and were analysed with a transmitted polarising light microscope at magnifications of ×25–400. The samples were grouped into petrographic fabrics based on the nature of their particulate inclusions, clay matrix and voids. Quantitative modal and textural data were also collected via point counting a total of 300 evenly spaced points (Quinn Reference Quinn2013: 102–11), using a PETROG digital stepping stage and software.
Petrographic composition, raw materials and manufacturing technology
All samples appear to have been produced with a non-calcareous clay paste, rich in angular, silt-sized inclusions of quartz and biotite mica (Figure 3). Inconspicuous clay-rich inclusions occur within the samples (Figure 3e–f). These could represent poorly hydrated remnants of a fine, dark clay source and a lighter, more silty variety, which were mixed together to produce a single paste with specific functional or aesthetic properties (Quinn Reference Quinn2013: 168–71). Naturally occurring ‘argillaceous’ inclusions can, however, also occur in clay deposits and may be transferred to ceramics made from such clay (Whitbread Reference Whitbread1986).

Figure 3. Thin-section photomicrographs of petrographic fabric groups and specific features detected within ceramic artefacts in this study. a) Sand-tempered terracotta warrior statue; b) sand-tempered terracotta acrobat fragment; c) sand-and-plant-tempered core sample from bronze waterfowl; d) untempered silty brick sample; e) dark, clay-rich plastic inclusion that may indicate intentional clay mixing; f) light-coloured plastic inclusion in sample that may indicate the intentional mixing with the material in the previous image; g) granite rock fragment within sand temper; h) phyllite metamorphic rock fragment within sand temper. Image width = 0.5mm, except g and h = 0.25mm. Images taken under crossed polars, except c and f, taken in plane polarised light.
The clay used to manufacture the ceramics may have been procured from the extensive loess deposits that exist in the Lintong region (Figure 1b) and that cover much of north-western China. These represent an almost limitless supply of raw material that has been used for the production of various ceramic types (Freestone et al. Reference Freestone, Wood, Rawson, McGovern, Notis and Kingery1989; Wood Reference Wood and Crick2000; Stoltman et al. Reference Stoltman, Jing, Tang and Rapp2009). Previous compositional analyses of the Terracotta Army also concluded that they were made from local loess, which has a fine, micaceous, clay-rich character (Gao et al. Reference Gao, Zhao, Li, Xie, Han, Feng, Fan, Zhang, Chai, Li, Zhang and Zhu2003; Shan et al. Reference Shan, Zhou, Wang, Qin, Zhang, Zhu and Zhang2003; Rong & Lan Reference Rong and Lan2005). The geochemical links that have been proposed by Gao et al. (Reference Gao, Zhao, Li, Xie, Han, Feng, Fan, Zhang, Chai, Li, Zhang and Zhu2003: 68, fig. 3) and Shan et al. (Reference Shan, Zhou, Wang, Qin, Zhang, Zhu and Zhang2003: 303, fig. 4) are, however, less than convincing.
This common base clay appears to have been treated in several ways, resulting in three distinct petrographic fabrics that correlate with artefact type. The paste of the terracotta warrior and acrobat statues was prepared by the addition of sand temper (Figure 3a–b); the core material of the bronze waterfowl was produced by adding sand and chopped plant matter (Figure 3c); and the bricks lining the floor of pit 1 and rammed-earth sample from pit K9901 seem to have been fashioned from the untempered clay described above (Figure 3d).
The identification of sand temper was based on the grain-size distribution of the coarser statue and core samples, which is strongly to weakly bimodal (Figure 4), by its often uneven penetration into the base clay, and by comparison with the untempered paste used for the bricks and rammed earth, which have a finer, better sorted, unimodal texture made up of intrinsic silt-sized inclusions (Figure 3d). Naturally occurring clay and sediment samples do not usually contain bimodal grains, due to the grading of material via water or wind.

Figure 4. Grain-size distribution histograms of ceramic artefacts from Emperor Qin Shihuang's mausoleum site, based on detailed textural data collected on the inclusions in thin section. a) Bimodal grain-size distribution of inclusions in terracotta warrior statue sample; b) unimodal grain-size distribution of inclusions in brick sample.
Sand temper could have been added to control the plasticity or ‘stickiness’ of the fine clay and make it more suitable for shaping into the ornate warrior and acrobat statues. It would also have ‘opened up’ the paste, creating pores through which water could evaporate. The absence of parallel-sided elongate voids in the statue samples indicates that these thick-walled objects were dried carefully before firing. Sand temper may also have been added to give the statues greater toughness once fired, reducing the possibility of failure when impacted. The ceramic core material inside the bronze waterfowl was probably sand tempered for similar reasons.
The composition of the sand-sized temper inclusions provides important clues about their geological origin. In addition to the dominant quartz and polycrystalline quartz grains, this material contains a smaller (<50 per cent) proportion of other inclusions, such as alkali and plagioclase feldspar, perthite, amphibole, biotite mica, epidote, phyllite, slate, sandstone, siltstone, micritic limestone and granite (Figure 3g–h). This high diversity of clasts suggests that the source of the temper was a ‘polymict’ sand deposit. The absence in thin section of agglomerates indicates that the sand was collected in a loose form, rather than being produced by crushing sandstone. A possible source might, therefore, be Quaternary alluvial sand.
Fine plant matter was also added to the paste of the waterfowl cores. This carbonised and partially burned out, leaving distinctive voids that contain charred organic material (Figure 3c). It may have been added to reduce the overall weight of the core, as it would not have been possible to remove this material from the long necks of the sculptures after casting (Shao et al. Reference Shao, Mei, Yang, Chen and Sun2015). The high porosity of the internal core (7.5–13 per cent; Figure 5) could also have facilitated venting of chemically combined water from the clay as the >1000°C molten bronze was poured into the mould (Liu et al. Reference Liu, Wang, Cai and Chen2013). This may have otherwise interfered with the casting of the delicate metal object.

Figure 5. Ternary diagram of the proportion of inclusions, clay matrix and voids within ceramic artefacts from Emperor Qin Shihuang's mausoleum site, based on modal data collected in thin section.
Our petrographic analysis of 12 terracotta warrior statues has illuminated the much-debated firing technology of these artefacts. Their rigidity and long-term preservation strongly suggests that the statues were intentionally fired, rather than simply being left to dry as suggested by Wiedemann et al. (Reference Wiedemann, Boller, Bayer, Sayre, Vandiver, Druzik and Stevenson1988). The survival of pollen within two previously analysed samples (Hu et al. Reference Hu, Zhang, Bera, Ferguson, Li, Shao and Wang2007) might be explained by poor oxygen penetration into the walls of the thick ceramic samples—this is known to be critical for pollen degradation during the firing of ceramics. The presence of birefringence, or ‘optical activity’, in the clay matrix of the majority of the samples under the microscope in crossed polars suggests that the statues were not subjected to a sustained temperature >850°C (Quinn Reference Quinn2013: 190–93). Common clay minerals, such as illite, begin to melt and lose their crystalline structure at this temperature. Inclusions of the mineral amphibole, which occur in many of the statue and bronze core samples, have a green colour under the microscope in plane polarised light, indicating a maximum firing temperature of <750°C.
Suggestions of firing temperatures of 900–1050°C (e.g. Yuan Reference Yuan1990) are not supported by our data, and would not have been necessary in order to harden the ceramics. It is worth bearing in mind, however, that the burning of the wooden roofs of the subterranean pits containing the Terracotta Army during their supposed destruction by General Xiang Yu in the late Qin period (Ledderose Reference Ledderose and Ledderose2000) could have resulted in the accidental re-firing of certain statues, thus explaining the wide variation in firing-temperature estimates of different studies (Shan et al. Reference Shan, Zhou, Wang, Qin, Zhang, Zhu and Zhang2003).
Firing probably took place in a permanent structure such as a kiln, due to the slow rate of temperature increase that would have been required to drive chemically combined water from the thick-walled terracotta statues without catastrophic failure, as well as the sustained maximum temperature needed to harden them throughout. Neither of these could have been achieved by firing in an uncontrolled, ‘open’ bonfire firing (Shan et al. Reference Shan, Zhou, Wang, Qin, Zhang, Zhu and Zhang2003), where the fuel and pottery load are in close proximity and the firing temperature is affected by changes in wind conditions and air temperature.
Organisation of production
The compositional and technological links between the various types of artefacts analysed from Emperor Qin Shihuang's mausoleum complex (Figure 6) are suggestive of the way in which the production of ceramic objects for the necropolis was organised. These may indicate specifically that one or more large workshops manufactured several different types of ceramics. Such a scenario may also be suggested by the existence of similar stamps and inscriptions on both terracotta warriors and roof tiles excavated from the mausoleum (Ledderose Reference Ledderose and Ledderose2000; Li et al. Reference Li, Bevan, Martinón-Torres, Xia and Zhao2016), as well as the possible shared method of slab building between the warriors’ legs and drainage pipes from the site (Nickel Reference Nickel and Portal2007).

Figure 6. Schematic diagram of interpreted paste-preparation technology of ceramic artefacts from Emperor Qin Shihuang's mausoleum site.
The production of several quite different ceramic artefacts by the same workshop may provide tentative evidence to support the previously suggested existence of several ‘cells’ of multi-skilled craftsmen (e.g. Ledderose Reference Ledderose and Ledderose2000; Martinón-Torres et al. Reference Martinón-Torres, Li, Bevan, Xia, Zhao and Rehren2014). These could be deployed on different tasks when needed and would be more adaptable than a single production-line arrangement (Martinón-Torres et al. Reference Martinón-Torres, Li, Bevan, Xia, Zhao and Rehren2014). The connection between the clay cores used to cast the bronze waterfowl statues and the production of other ceramics excavated from the mausoleum also suggests an unsuspected degree of ‘cross-craft interaction’ between potting and metalworking artisans.
An alternative explanation for the use of similar raw materials and paste-preparation technology in the manufacture of different ceramic objects is the existence of a centralised system of clay-paste processing and distribution at the production location (Figure 6). Under this interpretation, different workshops could have been responsible for specific ceramic objects but received their raw materials from a single source (Yuan & Snethlage Reference Yuan and Snethlage2006). Such a system would make sense in terms of standardisation and quality control, given that clay was the essential ingredient of the approximately 7000 statues and a multitude of other ceramic items. As our analyses have shown, considerable care was taken to select and blend specific ingredients into the paste according to the type of artefact being produced. Strict adherence to these recipes would have been crucial in guaranteeing the successful production of such large numbers of complex artefacts. One way of ensuring this would have been to decouple raw material acquisition, processing (drying, crushing, refining) and paste preparation (clay mixing and tempering) from the processes of forming, firing and decorating the ceramics. Having a dedicated department responsible for the supply of clay to the various workshops would lead to less variability in composition than if this was left to individual production units. It would also help to ensure a constant supply of large quantities of raw material, which would have been a continual requirement (Ledderose Reference Ledderose, Blansdorf, Emmerling and Petzet2001).
Production location
Our interpretation of the raw materials used in the manufacture of the terracotta warrior figures and other ceramic objects addresses the as yet unanswered question of their production location. The origin or ‘provenance’ of archaeological ceramics can be interpreted by locating the sources of their raw materials. An assumption in such studies is that clay and temper were obtained close to the site of pottery production (Quinn Reference Quinn2013: 119), which seems probable in this case. Previous scientific investigations have used a geochemical provenance approach to demonstrate that local clay deposits were indeed used (Gao et al. Reference Gao, Zhao, Li, Xie, Han, Feng, Fan, Zhang, Chai, Li, Zhang and Zhu2003; Shan et al. Reference Shan, Zhou, Wang, Qin, Zhang, Zhu and Zhang2003; Lei et al. Reference Lei, Gao and Yuan2004). One such local candidate is the fine, silty loess that underlies much of central and northern Shaanxi Province. The similarity of this wind-blown material over large areas (Sun Reference Sun2002), however, means that distinguishing between the loess of the Lintong area and that located farther afield near Xi'an, for example, will probably be difficult. Re-examination of the statistical classification of Gao et al. (Reference Gao, Zhao, Li, Xie, Han, Feng, Fan, Zhang, Chai, Li, Zhang and Zhu2003: 68, fig. 3) and Shan et al. (Reference Shan, Zhou, Wang, Qin, Zhang, Zhu and Zhang2003: 303, fig. 4) indicates that there is, in fact, a rather poor correspondence between the local clay samples and the analysed terracotta statue fragments. This could be explained by the use of other, possibly more distant clay sources, or perhaps the modification of the local material via processes such as refining, clay mixing or tempering.
Detailed characterisation of the sand temper added to the terracotta warrior, the acrobat statues and the clay cores of the bronze waterfowl provides additional evidence for the location of their raw material sources, which was not considered in the previous provenance studies. Consideration of the Lintong and Xi'an bedrock geology indicates that the diverse mineral and rock types that occur within the temper material can be found on Mount Lishan to the south of the site (Figure 1b). This is composed of granite, gneiss, schist, amphibole, sandstone, siltstone and other lithologies, and is geologically distinct from the lowland area to the north and west. A complex arrangement of loess, river terraces from the nearby River Wei, and alluvial fans originating from Mount Lishan underlie the mausoleum complex (Figure 1b). It is possible to envisage juvenile, sub-angular to sub-rounded polymict sand of the type most probably used as temper being procured from these alluvial cones. Although no raw material sampling and analysis was undertaken in the present study, observations of outcrops of such material confirm their diverse clast composition.
Current evidence, therefore, suggests that the clay figures of the Terracotta Army were manufactured from locally available raw materials. Given that the long-distance transport of approximately 1050 metric tonnes of clay and temper seems unlikely, we can perhaps conclude that the production workshops were situated somewhere in the Lintong area. Moving the delicate 7000 or so 150–200kg warriors, generals and horses would also have been a huge operation (Ledderose Reference Ledderose and Ledderose2000); it is probable, therefore, that the production location was close to the mausoleum itself (Li et al. Reference Li, Bevan, Martinón-Torres, Xia and Zhao2016). Terracotta sculpture fragments and the remains of kilns were reported by local farmers approximately 200m from pit 1 during the construction of the site museum (Yuan Reference Yuan1990; Ledderose Reference Ledderose, Blansdorf, Emmerling and Petzet2001; Nickel Reference Nickel and Portal2007), but these were never investigated in detail. Subsequent surveys and building work inside and outside the known extent of the mausoleum complex have failed to detect further evidence of this type. One explanation may be that the ceramic workshops and kilns were dismantled after the completion of the mausoleum in 210 BC.
Stamps, inscriptions and painted symbols on certain terracotta warrior statues may indicate the activity of several different workshops, both in the Lintong area and perhaps 50km away in the Qin capital of Xianyang (Yuan Reference Yuan1987, Reference Yuan1990; Li et al. Reference Li, Bevan, Martinón-Torres, Xia and Zhao2016). Although our initial dataset does not support this idea, Gao et al. (Reference Gao, Zhao, Li, Xie, Han, Feng, Fan, Zhang, Chai, Li, Zhang and Zhu2003: 68, fig. 3) may have detected such evidence. Their compositional classification reveals that the analysed terracotta statues of pits 1, 2 and 3 differ from one another in terms of their elemental composition. Although they did not explore the specific elements responsible for this pattern, and we therefore cannot rule out the possibility of differential preservation or post-burial contamination, the idea that specific workshops were responsible for the manufacture of statues for particular pits is an attractive one. The detailed microscopic analysis of additional samples from pits 2 and 3, as well as stamped fragments, is a future research direction that will hopefully address this theory.
If we conclude that the majority of the terracotta warrior statues were produced at, or very close to, Emperor Qin Shihuang's mausoleum, then their links with other artefact types in our dataset may suggest the manufacturing location of these lesser-known ceramic objects. That the terracotta acrobats were produced close to their findspot is perhaps not surprising, given their similar size and manufacturing method to the statues of the Terracotta Army. Unfired bricks found in pit 2 suggest that these were also produced near the mausoleum (Li Reference Li2007b). The suggestion that the clay cores found within the ornate waterfowl sculptures were made on site, however, is novel, and has important implications for our knowledge of the production location of these and other ornate bespoke bronze artefacts, such as two large-scale, horse-drawn chariots found buried within the inner wall of the mausoleum (Figure 1a). It may be assumed, due to the delicate nature of the core material used to cast metal objects (particularly if they were not fired prior to use, as may be the case with the waterfowl sculptures), that they were produced at the same general location as the casing (Tan Reference Tan1999).
Conclusions
The detailed microscopic analysis of several fragments of the life-sized ceramic statues of Emperor Qin Shihuang's Terracotta Army and other clay-based objects recovered from his mausoleum has been used to reconstruct several aspects of the manufacturing technology of these impressive, numerically abundant artefacts. In particular, our analyses have indicated that instead of using unprocessed raw clay, as has been suggested previously, a surprisingly sophisticated process of raw material acquisition and treatment was employed to achieve a suitable paste for the manufacture of the figures. Clay appears to have been extracted from the extensive loess near the mausoleum site, and mixed with temper from mineralogically diverse alluvial sand eroded from Mount Lishan, a short distance to the south. This geological interpretation provides additional evidence that the 7000 statues were made somewhere within the mausoleum complex, most probably close to their site of deposition in three underground pits. Our analysis indicates that the bespoke ornate bronze sculptures unearthed from the site were also locally produced, for inclusion in the mausoleum.
Strong compositional and technological links exist between the terracotta statues and other clay-based artefacts from the First Emperor's necropolis, in terms of the use of a common base clay and other shared ingredients, which were treated in different ways according to the objects being produced. This may suggest that workshops were responsible for more than one type of ceramic product—a scenario suggested by the shared forming methods of the terracotta statues and certain architectural ceramics, and by similar inscriptions on these objects. Such an interpretation points to the existence of cross-craft interaction between potters and metalworkers at the mausoleum site.
An alternative explanation, and one that is favoured here, is that clay was procured and processed by a separate division of the 700000 strong workforce behind the building of the mausoleum, then handed out to the various ceramic workshops. This would ensure close adherence to a strict, standardised paste recipe, which surely represented a key factor in the smooth production of large numbers of statues, bricks and other objects. Centralising this part of the manufacturing operation would have enabled potting workshops to concentrate on the physical process of ceramic manufacture.
The attention seemingly given to the microscopic composition of the clay paste used to build the terracotta statues conforms to the tight control applied to other aspects of their manufacture, including the use of pre-fabricated moulds to produce a range of identical component parts, the assembly of these modules in a multitude of different combinations and the marking of the statues for administrative or quality-control purposes (Yuan Reference Yuan1987; Ledderose Reference Ledderose, Blansdorf, Emmerling and Petzet2001; Li et al. Reference Li, Bevan, Martinón-Torres, Xia and Zhao2016). A high level of standardisation also appears to have been applied to the production of other artefacts recovered from the site, such as the bundles of bronze arrowheads and crossbow triggers that were found in association with the Terracotta Army (Li et al. Reference Li, Bevan, Martinón-Torres, Rehren, Cao, Xia and Zhao2014; Martinón-Torres et al. Reference Martinón-Torres, Li, Bevan, Xia, Zhao and Rehren2014).
The construction of Qin Shihuang's enormous and highly complex mausoleum within the relatively short period between his ascension to the throne and his untimely death would surely have called for a high degree of organisation on many levels. The Qin Empire is thought to have surpassed other Chinese states in terms of mobilising masses of people and carefully coordinating their efforts towards ambitious goals (Yates Reference Yates and Portal2007). The production of ceramics, metals and other artefacts deposited in the First Emperor's mausoleum clearly reflects a degree of organisation and efficiency that characterised many aspects of the empire and laid the foundations for imperial China.
Acknowledgements
The research presented here forms part of a collaborative project between the Institute of Archaeology, University College London (UCL) and Emperor Qin Shihuang's Mausoleum Site Museum. We are indebted to the late Peter Ucko and to Wu Yongqi, who first made this co-operation possible, and to Hou Ningbin for his ongoing support and encouragement. Since 2012, the project ‘Imperial Logistics: the Making of the Terracotta Army’ has been endorsed as a British Academy Research Project. Funding for the project was generously provided by the British Academy, the UCL Provost's Office, Rio Tinto and the Institute for Archaeo-Metallurgical Studies. Shao Anding of the Shaanxi Provincial Institute of Archaeology kindly provided access to the clay core samples. The PETROG digital stepping stage and point-counting software was provided by Conwy Valley Systems Ltd, Wales (www.petrog.com). Siran Liu translated some of the Chinese publications cited herein. All prepared scientific samples from this study are housed at the Department of Conservation, Emperor Qin Shihuang's Mausoleum Site Museum.