Introduction
Since its commercial introduction in 1965, the scanning electron microscope (SEM) has evolved to incorporate many improvements in imaging and microanalysis capabilities, yet the problem of charging in non-conductive samples remains. The SEM user is still required to cope with the examination of non-conductive samples on a case-by-case basis. Fortunately, there are a number of strategies to aid in this process.
Charge mitigation
The problem is as follows. Negative charge builds up on a non-conductive specimen at normal electron accelerating voltages (kV), particularly above 10 kV, because more electrons land on the specimen that leave as secondary electrons (SEs) or backscattered electrons (BSEs). This can produce in the SEM image strong bright areas and scan raster shifts. These image artifacts can be so severe that the resulting image has no relationship to the object being scanned. While charging can be minimized by imaging at low beam energies near 1 keV, only recent SEM models, particularly those employing field emission electron guns (FE-SEMs), can maintain small electron beam probe sizes on the specimen at such a low accelerating voltage (kV). Alternatively, a variable-pressure SEM, operating in low-vacuum mode (specimen chamber pressure about 1 torr = 133 Pa), produces positive ions that can neutralize surface charging. A third method of suppressing charge buildup is to deposit on the non-conducting specimen surface an extremely thin conductive coating, typically a metal that adds minimal structure to the true specimen surface. The latter method is easy, dependable, and can be used with any SEM. Some coatings exhibit a grain structure that can be observed in modern SEMs, especially those equipped with field-emission (FE) electron guns. There are a range of metals for sputter coating, some for use at low magnifications and others for use at high magnifications in an FE-SEM. An additional benefit of metal coating is that the yield of secondary electrons (SEs) is usually much higher than for the bare non-conducting surface [Reference Goldstein1].
Coating selection
The coating metal should be selected to achieve optimum performance based on the type of analysis to be performed: for example, low-magnification, high-magnification imaging, or microanalysis. Most SEM sputter coaters permit quick target changes, allowing the microscopist to select an appropriate coating metal for the task at hand.
The sputtered coating should have a high secondary electron emission yield so that the signal-to-noise ratio will be high. The ideal coating should have no structure (grains or islands) that would interfere with the details of specimen features. Thus, coatings with large grains would be suitable only for low magnifications, where the structure of the coating would be too small to see. Some metals that produce fine-grained coatings suitable for high-magnification imaging, deposit at slower rates; but, this is not a problem because useful coating thicknesses are quite small, typically 1–3 nm. Some coating materials have X-ray lines that may interfere with the detection of elements in the specimen. However, at typical accelerating voltages, this should not be a problem when the coating is only 1–2 nm in thickness. If there is a serious interference, another coating metal could be selected to coat that specimen. Finally, there is a cost factor since the most useful coating materials are precious metals.
Materials and Methods
While not exhaustive, the list of materials below describes the most common metals used to sputter coat samples for the SEM. Keep in mind that this information is only valid when using a modern DC magnetron SEM sputter coater with pure argon as the process gas. Some coatings require “high-resolution” sputter coaters that operate at better vacuum to reduce the possibility of oxidation during processing; in fact, some systems employ a shutter to shield the sample while oxide is sputtered off the target itself in a pre-conditioning step. Carbon is commonly used as a conductive coating for microanalysis samples, but this material should be deposited by vacuum evaporation or ion-beam sputtering.
Instrumentation
The sputtered films for this article were produced using a CCU-010 HV (turbo-pumped) Safematic Coating System on glass slides. Pure argon was used as a backfill “process gas.” In general, there are two types of sputter coaters. The system above could be described as a “high-resolution” sputter coater because a turbo pump is employed to obtain a higher (and cleaner) vacuum environment, and pure argon gas is backfilled in the chamber to remove air and increase sputter efficiency. The second type of sputter coater may be described as a more basic unit, developing only a modest vacuum with a mechanical pump and sometimes replacing argon backfill gas with room air. This basic sputter coater may be acceptable for coating Au and Au/Pd films, but not for coatings with finer grain sizes. Use of a system with a poorer vacuum and air backfill results in lower sputter efficiency and deposited films that are not as clean. Film thickness measurements were obtained using the quartz thickness monitor (operating at 6 MHz) inherent with the system. Coatings in Figure 1 were imaged with a Zeiss Merlin FE-SEM. The images in Figure 2 were obtained using a Zeiss EVO 15 LS employing tungsten source.
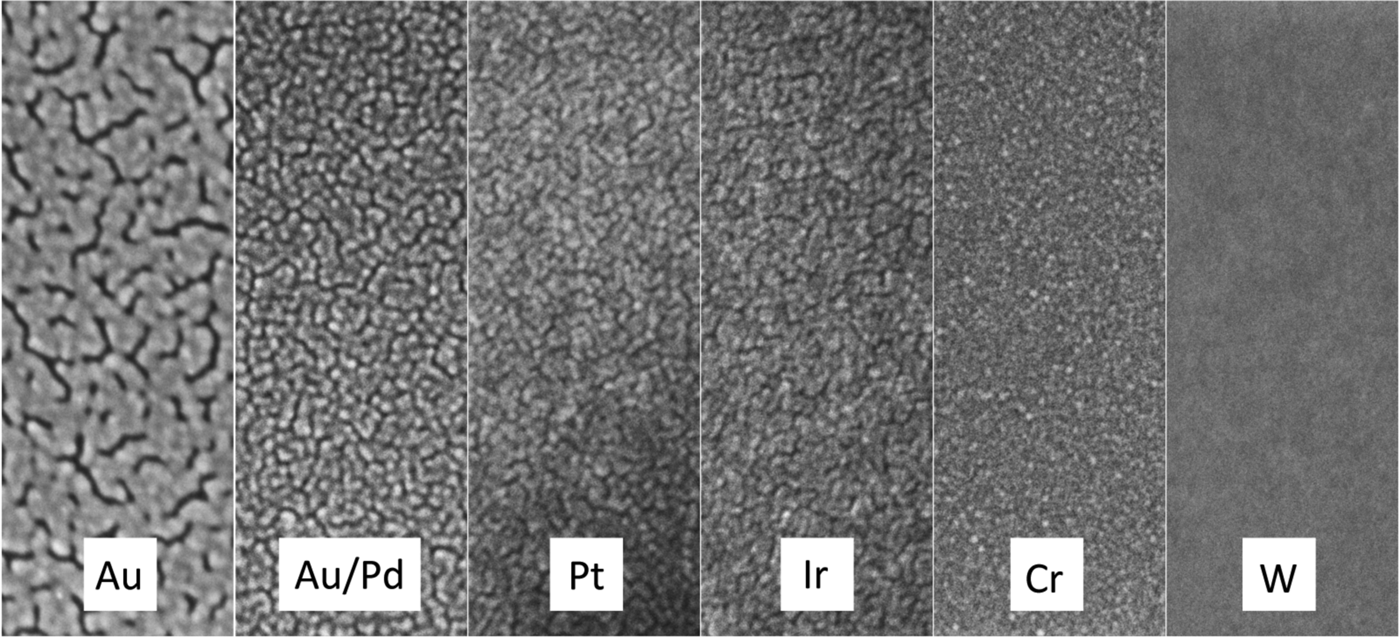
Figure 1: Secondary electron SEM images of various sputter target materials. All coatings were 2 nm thick deposited on glass and imaged at 10 keV. Image widths = 140 nm.

Figure 2: Secondary electron SEM images at 5 keV of ePTFE tape. (a) Uncoated tape shows significant charging with bright saturated area and image distortions. (b) Sputter coated with 5 nm of Au/Pd shows charging mitigated. Image widths = 50 μm.
Target Metal Selection
Gold is perhaps the most widely used coating material for non-conductive SEM samples, but it is not recommended as a sputter coating for research purposes where high-magnification images are required (see Au/Pd below). Gold has a high secondary electron yield and sputters relatively rapidly, but the coating structure is composed of large islands (grains) that can be observed at high magnifications in most modern research-level SEMs (Figure 1 and Table 1). Thus, it should only be used for imaging at low magnifications, say less than 5000×, where the coating structure will not interfere with the structural details of the sample. An advantage shared by most other precious-metal coatings, Au coatings do not oxidize in laboratory air. X-ray emission lines of the Au M-series (2.12 keV) may interfere with X-rays from S and Nb, while the Au L-alpha line (9.71 keV) may interfere with X-rays from Ge. If the Au coating is appropriately thin, however, there should not be significant problems with qualitative X-ray microanalysis.
Table 1: Some characteristics of common sputter target materials.
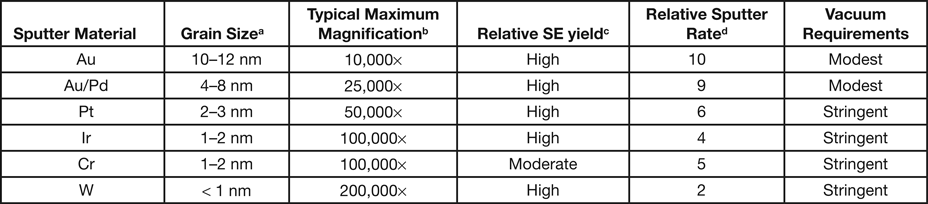
aMeasured from images similar to Figure 1, from discussions with Jack Vermeulen, and from [Reference Newbury2].
bEstimates for typical SEMs: tabletop to 10 kx; workhorse W-SEM to 50 kx; FE-SEM above 50 kx.
cEstimated from secondary electron coefficients at 20 keV given in [Reference Lin and Joy4] and the DC Joy electron database [web.utk.edu/~srcutk/database.doc].
dEstimated from data in [Reference Echlin3].
Gold/palladium sputtered alloys (60/40 and 80/20) have smaller grain size and are the recommended metal coatings for general research purposes. Secondary electron yields are high, and sputter rates for Au/Pd are only slightly lower than for pure Au. The Pd L-series X-ray lines at 2.84 keV do not overlap important lines from other elements; thus, no additional interference with X-ray microanalysis would be expected beyond that mentioned above for Au.
Platinum has a finer grain size than either Au or Au/Pd, which makes it more suitable for higher-magnification applications. A sputtered Pt coating exhibits a high SE yield, but Pt has a lower sputtering rate than Au (Table 1). Pt has been observed to crack. This effect could be “stress cracking” and could be attributed to oxygen deposition in the sputtered coating, indicating the need for a sputter coater with better vacuum. The characteristic X-rays of Pt (particularly the M-series at 2.05 keV) have the potential to overlap with lines from P and Zr, but interference should be minimal for 1–2 nm thick coatings.
Platinum/palladium alloy (80/20) has a similar small grain size and high SE yield as pure Pt, but it is less sensitive to “stress cracking.” The Pt/Pd alloy is a suitable all-round coating material for high-magnification applications.
Iridium exhibits a fine grain size on virtually all specimen materials and is an excellent all-round coating material for high-magnification applications. It is also usually the most expensive coating metal, typically about twice the price of Au/Pd and Pt. This non-oxidizing material has a high SE yield, and for some applications it has been replacing chromium for high-resolution sample coating. It sputters at a lower rate and requires the use of a turbo-pumped high-resolution sputter coater. Since specimens for microanalysis are often coated with evaporated carbon, Ir is a good alternative coating material when carbon must be analyzed by X-ray microanalysis. Interference of the Ir M-series (1.98 keV) and L-series (9.18 keV) could occur for P and Ga, respectively. Again, a 1–2 nm thick coating will provide adequate conductivity while not interfering with X-ray microanalysis.
Chromium has a very fine grain size, but the sputtering rate is only about half that of Au. Thin Cr films have proven to be a useful coating material for high-magnification imaging in FE-SEMs. Because it oxidizes easily, Cr requires the use of a turbo-pumped, high-resolution sputter coater with a target shutter for target conditioning to remove the oxide prior to coating. The better vacuum, in combination with pure argon flushing of the chamber, reduces the partial pressure of oxygen enough to avoid oxidization of the sputtered Cr layer. The thin Cr film on the sample surface will oxidize in air, and samples must be viewed immediately after coating. Samples may be stored in high vacuum. Chromium is an excellent coating material for high-resolution backscattered electron imaging of low Z materials and biological samples. Chromium can be a good choice for-Xray microanalysis because its X-ray lines do not interfere with common specimen elements except for oxygen, where a near overlap occurs between the Cr L-series (0.573 keV) and the oxygen K-line (0.525 keV).
Tungsten is an excellent coating for high-resolution coating since it has an extremely fine grain size (Figure 1 and Table 1). But W oxidizes rapidly and requires the same stringent turbo-pumped high-resolution coater described for Cr. As a refractory metal like Cr, it has a low sputtering rate, but the SE yield is high. Samples must be imaged immediately after coating because of rapid oxidization in laboratory air. The W X-ray spectrum has a wide range of potential microanalysis interferences, but the extremely thin coating (< 1 nm) minimizes the problem.
Other metals
Alternative precious metals (silver, tantalum, and palladium) and common metals (nickel, copper, and titanium) have been used for special purposes. However, the possibility of coating oxidation may still be a problem for some of them (Ag, Ta, Ni, Cu, and Ti). Silver has a particular advantage not found with other coatings: it can be dissolved with Farmer's reducer, returning the surface to the uncoated state.
Results
Figure 1 and Table 1 show the variation in grain size with the most common sputtering targets. The grain size values in Table 1 are for comparison purposes and for defining trends. The images in Figure 1 reflect the trends. Images were obtained on a Zeiss Merlin FE-SEM at the same magnification for all coatings. Figure 2 shows a practical demonstration of how sputter coating can reduce, if not eliminate, charging on a low-Z, non-conducting material such as expanded polytetrafluoroethylene (ePTFE). Figure 2a shows the severe charging that occurs with no coating applied. Figure 2b shows the same sample coated with approximately 5 nm of Au/Pd, and charging appears to have been eliminated.
Discussion
The examples shown here are only valid when using a modern turbo-pumped DC magnetron SEM sputter coater with argon as the process gas. Grain size of the coating depends on coating thickness and the coating/sample material interaction. As a rule, the thinner the coating, the smaller the grain size. If the surface has irregular topography with cavities, a uniform coating might be difficult to achieve. As a result, localized surface charging could degrade image quality. This problem can usually be rectified with a tilting or rotating sample stage deployed within the sputter-coating system. Coating thickness was determined using a quartz thickness monitor. As a rule coating thickness monitors register values that are not absolute in value. The operator sets a defined thickness end point, and the sputter process will cease. The actual thickness could be greater. If a thickness monitor is not available, the sputter coater manufacturer may have guidelines for specific targets (that is, sputter time, current setting, vacuum), which may be used a for a “ball park” thickness determination. Also visual evaluation of the film color and opacity can be useful in estimating the thickness of the sputtered film.
If X-ray microanalysis of the sample is required, select a coating (target) material that is not present in the sample. This should avoid interfering peaks in the X-ray spectrum of the sample. Also consider all the X-ray lines possible from your sample (that is, K-series, L-series, M-series) and from the sputtered film. It must be kept in mind not only what X-ray lines might be present, but also what lines could be enhanced at the electron beam accelerating voltage (kV) to be used in your study. If all possible interferences must be avoided, then classic carbon deposition (evaporation) is the recommended approach to render a non-conductive sample amenable for X-ray microanalysis.
The rule of thumb for selecting a sputter target for coating an SEM specimen is to choose the metal that produces the smallest grain size consistent with capabilities of the SEM available. Thus, Au may be acceptable for a table-top SEM for magnifications below 5000×; Au/Pd and Pt would be useful for general purpose SEM imaging; and Cr or W would be appropriate for high-resolution, high-magnification imaging with an FE-SEM (Table 2). Once the target metal has been selected, the effort should be to produce the thinnest metal film that mitigates charging effects, ideally in the range of 1–2 nm.
Table 2: Sputter target metals for various applications (indicated by x). Recommendations assume that a 1–2 nm thick film was properly deposited using appropriate equipment.

aCarbon deposited to 10 nm thickness by vacuum evaporation or ion-beam sputtering
Conclusion
The ease with which sputter coater target metals can be changed allows for flexibility in preparing SEM specimens for imaging and microanalysis. Targets are available for low-magnification and high-magnification work, and they may be changed to facilitate elemental analysis. Use the metal coating that produces the smallest grain structure consistent with the capabilities of the SEM available. Different sputter targets vary in cost, and some require additional infrastructure such as the increased pumping/vacuum capabilities of a high-resolution sputter coater.
Acknowledgments
The authors thank Jack Vermeulen of Micro to Nano, Haarlem, Netherlands, for helpful discussions.